螺纹接端检测项目及技术要点详解
一、几何尺寸检测
-
- 大径(外螺纹)/小径(内螺纹):使用螺纹千分尺、三坐标测量机(CMM)或光学投影仪测量,需符合GB/T 196、ISO 724等标准公差范围。
- 中径(节径):通过三针法或螺纹中径规检测,中径偏差直接影响螺纹配合松紧度。
- 螺距:采用螺距规或影像测量仪逐牙比对,偏差需小于±0.01mm(高精度螺纹)。
- 牙型角:60°(公制螺纹)、55°(英制管螺纹)等,利用投影仪轮廓比对或专用牙型角规验证。
-
- 牙顶/牙根形状:检查是否因加工磨损导致平牙或圆弧过度,影响啮合强度。
- 螺纹锥度(管螺纹):使用锥度规检测圆锥螺纹的锥角一致性(如NPT螺纹锥度为1:16)。
二、表面质量检测
-
- 裂纹、折叠、毛刺:10倍放大镜或工业内窥镜检查,重点排查螺纹根部应力集中区域。
- 锈蚀、镀层剥落:盐雾试验(如ASTM B117)评估防腐性能,镀层厚度通过XRF或金相切片法测量。
-
- 粗糙度仪测量Ra值(典型要求Ra≤3.2μm),过高导致摩擦增大,过低影响密封剂附着。
三、力学性能测试
-
- 模拟装配过程,记录拧入扭矩曲线,对比标准值(如DIN 13或ISO 898),检测异常扭矩波动(可能由螺纹变形或异物卡滞导致)。
-
- 万能试验机施加轴向拉力至螺纹断裂,计算极限载荷;扭转试验机测试螺纹抗扭屈服强度。
-
- 高频交变载荷下(如10^6次循环),评估螺纹在振动环境中的耐久性。
四、功能性验证
-
- 使用通止规(GO/NO-GO规)判定螺纹旋合性:通规(GO)应顺畅旋入,止规(NO-GO)旋入不超过2圈。
-
- 气压/水压试验:加压至1.5倍工作压力,保压5分钟无泄漏(如ISO 7-1标准)。
-
- 振动台模拟工况,检测预紧力衰减率,评估防松结构(如尼龙嵌件、双螺母)有效性。
五、材料及热处理检测
-
- 光谱仪(OES)或ICP检测碳钢、不锈钢等材料的元素含量,确保符合牌号要求(如304不锈钢Cr含量18-20%)。
-
- 维氏硬度计测试表面硬度(如8.8级螺栓要求HV 250-320);金相显微镜观察淬火马氏体比例及脱碳层深度(脱碳层需≤0.05mm)。
六、特殊环境适应性测试
-
- 高低温箱循环测试(-50℃~200℃),评估螺纹尺寸热稳定性及材料脆化倾向。
-
- 酸性盐雾(如CCT循环腐蚀试验)模拟恶劣环境,检测镀锌、达克罗涂层耐蚀等级。
七、检测流程管理
- 抽样方案:根据GB/T 2828.1执行AQL抽样,关键螺纹(如航空件)采用100%全检。
- 数据追溯:采用二维码或RFID标记工件,关联检测数据至MES系统实现质量追溯。
- 不合格处理:设置返修区隔离缺陷品,分析根本原因(如刀具磨损、夹具偏移)并校准工艺。
结语
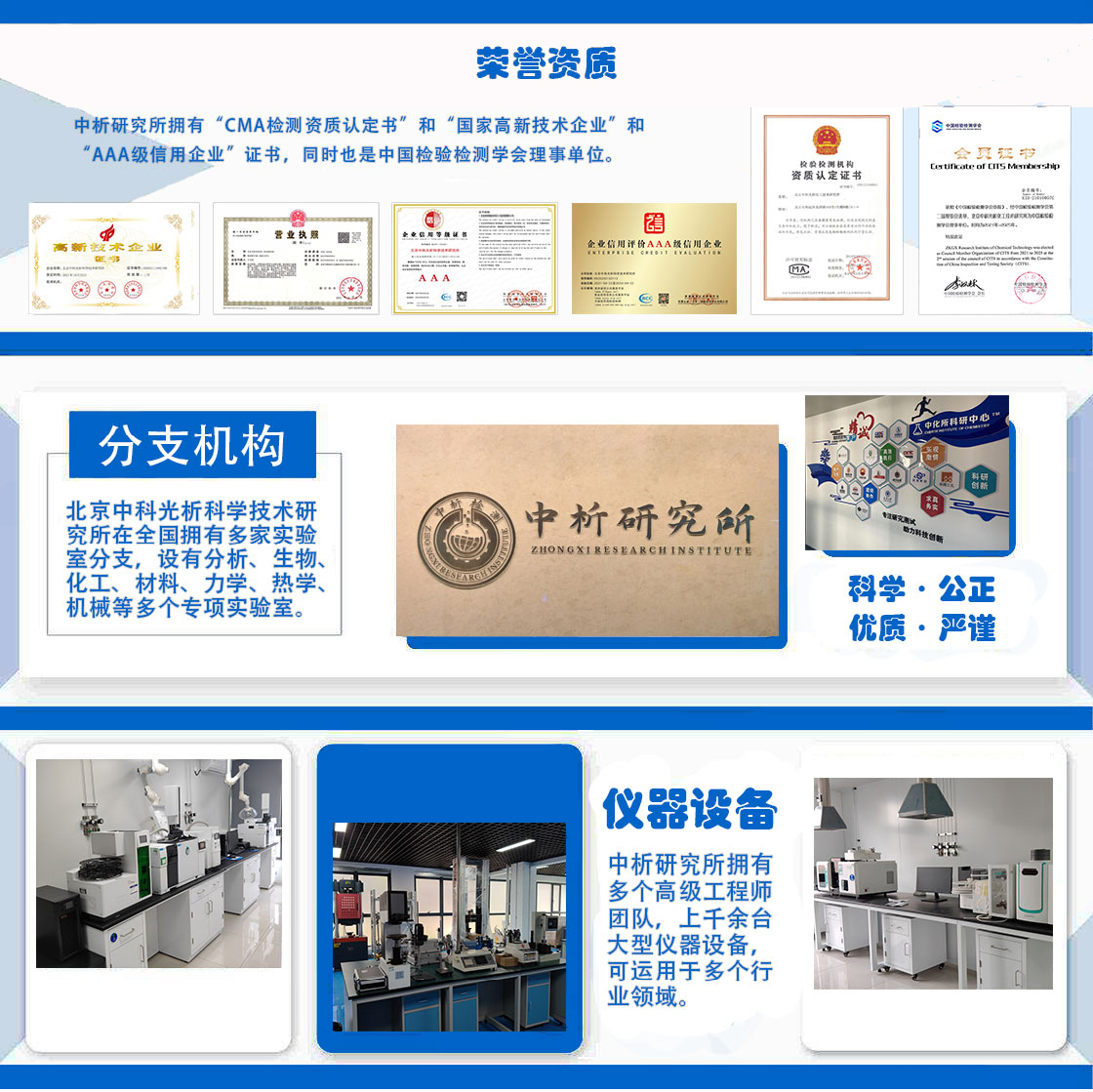
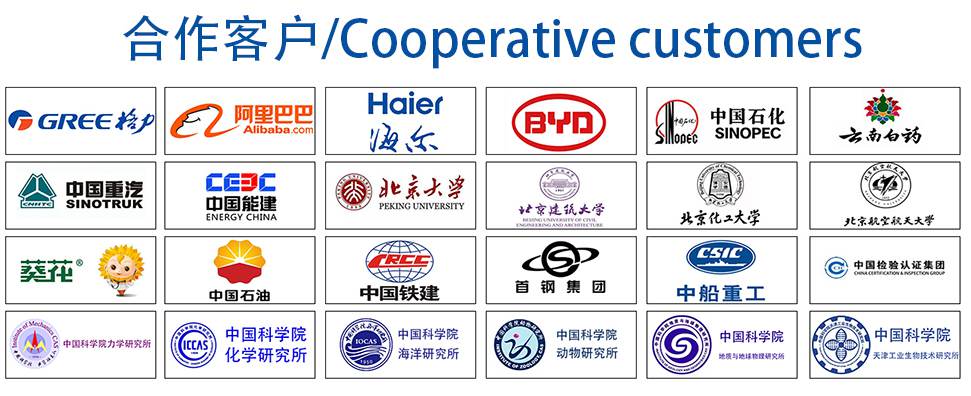
材料实验室
热门检测
22
25
24
24
26
23
21
17
15
20
23
25
22
22
22
18
21
21
26
19
推荐检测
联系电话
400-635-0567