试验电应力检测:核心检测项目详解
一、电应力检测的核心项目
- 目的:验证绝缘系统在短期高电压下的抗击穿能力。
- 方法:施加高于额定电压的测试电压(如2倍工作电压+1000V),持续时间通常为1分钟。
- 标准:
- 家用电器:IEC 60335-1规定测试电压范围1kV~4kV(依设备类别)。
- 电力设备:GB/T 16927.1要求依据额定电压分级测试。
- 设备:耐压测试仪(输出范围可达0~15kV)。
- 目的:量化绝缘材料在直流电压下的导电性能,预防漏电风险。
- 方法:施加500V或1000V直流电压,测量电阻值(通常要求≥100MΩ)。
- 应用场景:
- 电缆、变压器绕组:GB/T 3048.5规定测试时间1分钟。
- PCB板:IPC-A-610标准要求关键节点绝缘电阻≥100MΩ。
- 目的:确认设备接地路径的完整性,保障人员安全。
- 方法:施加25A交流电流,测量接地端与外壳间电阻(一般≤0.1Ω)。
- 标准:IEC 60950-1规定接地电阻需在0.1Ω以下。
- 目的:评估设备在正常运行时的电流泄漏水平,防止触电风险。
- 类型:
- 接触电流(Touch Current):模拟人体接触时的泄漏电流(≤0.25mA)。
- 保护导体电流(PE Current):通过接地线的泄漏值(依设备功率而定)。
- 设备:泄漏电流测试仪(精度±2%)。
- 目的:模拟雷击或开关浪涌对设备的冲击耐受能力。
- 波形参数:
- 标准雷电波:1.2/50μs(波头/波尾时间)。
- 操作波:250/2500μs。
- 典型应用:
- 电力避雷器:GB 11032规定耐受10次标准雷电冲击。
- 汽车电子:ISO 7637-2模拟车载瞬态脉冲。
- 目的:检测绝缘材料内部微小放电现象,预防渐进性失效。
- 方法:施加接近击穿电压的交流电,监测放电量(pC级)。
- 应用:高压电缆(IEC 60885-3)、GIS开关设备。
二、测试流程与设备选型
- 预处理:清洁被测物,消除表面导电杂质。
- 环境控制:温度(23±5)℃、湿度≤75% RH(IEC 60068-1)。
- 分级加压:逐步升高电压至目标值(避免瞬时过载)。
- 数据记录:记录击穿电压、泄漏电流峰值等关键参数。
测试项目 | 关键参数 | 推荐设备示例 |
---|---|---|
耐压测试 | 输出电压0~15kV,精度±3% | Chroma 19032 |
绝缘电阻测试 | 测试电压1000V,量程10GΩ | Megger MIT410 |
局部放电检测 | 灵敏度≤1pC,带宽100MHz | Omicron MPD 600 |
三、典型失效模式与对策
-
- 原因:材料缺陷(气泡、裂纹)、设计余量不足。
- 对策:采用CT扫描分析缺陷位置,优化绝缘厚度。
-
- 原因:潮湿环境下绝缘电阻下降,滤波电容失效。
- 对策:增加防潮涂层,更换X2/Y2级安规电容。
-
- 原因:连接点氧化、螺钉松动。
- 解决方案:使用镀银端子,定期维护检查。
四、行业应用案例
- 新能源领域:光伏逆变器需通过IEC 62109-1标准,耐压测试电压高达4kV(输入-输出端)。
- 汽车电子:ISO 16750-2规定车载设备需耐受±8kV静电放电(ESD)。
- 医疗设备:IEC 60601-1要求患者接触部分的泄漏电流≤10μA(正常状态)。
五、未来趋势
- 智能化检测:AI算法实时分析局部放电模式,预测绝缘寿命。
- 在线监测系统:集成传感器实现设备运行状态下的持续电应力评估。
- 新材料测试:针对宽禁带半导体(SiC、GaN)开发专用高压测试协议。
上一篇:锂离子蓄电池及蓄电池检测下一篇:特性电压检测
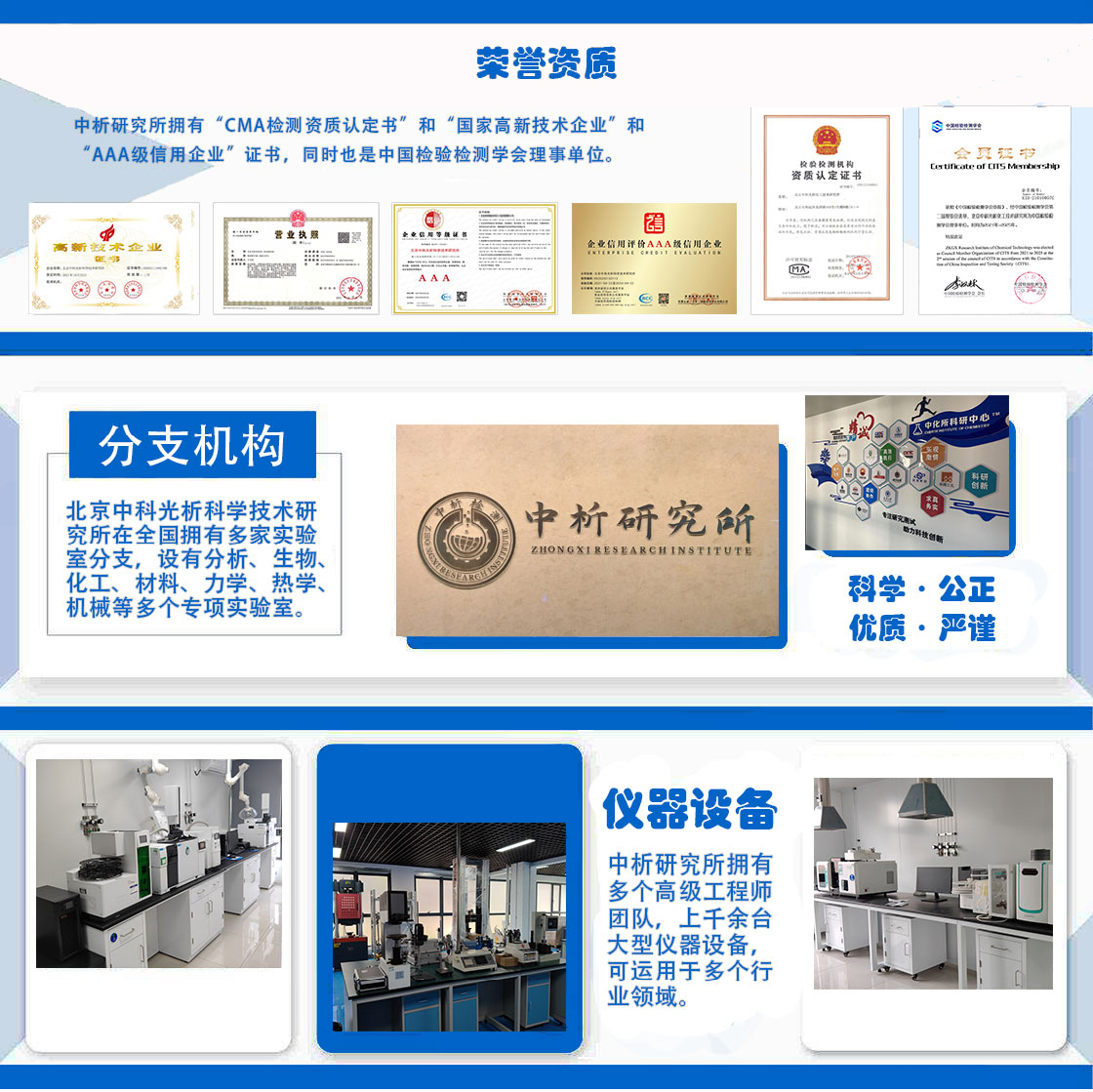
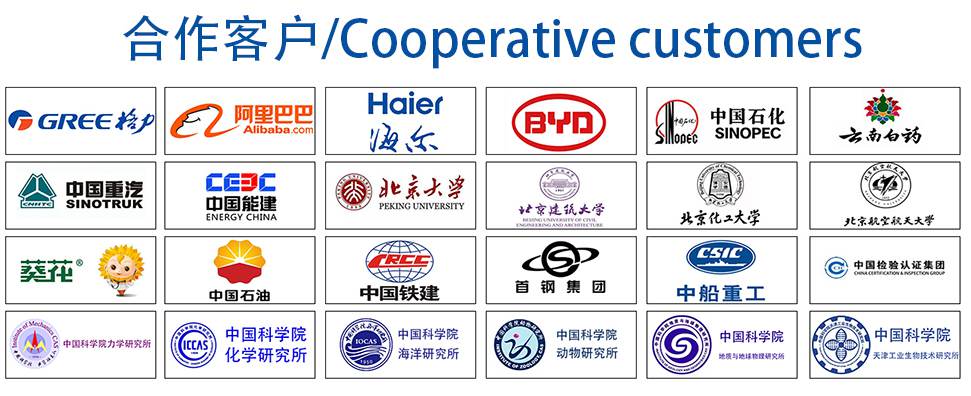
材料实验室
热门检测
29
32
31
32
51
45
54
47
50
52
43
55
44
52
45
48
43
49
45
45
推荐检测
联系电话
400-635-0567