元件耐溶剂性检测:核心检测项目与实施方法
一、检测目的
- 外观完整性(无溶胀、裂纹、变色、起泡等);
- 机械性能稳定性(硬度、拉伸强度、弹性模量等);
- 功能性保持(导电性、绝缘性、密封性等);
- 化学兼容性(无溶解、析出物或化学反应)。
二、核心检测项目与测试方法
1. 浸泡测试
- 目的:模拟元件长期浸泡在溶剂中的极端情况。
- 方法:
- 将元件完全浸入选定溶剂(如乙醇、丙酮、二甲苯等)中,按标准(如ISO 2812或ASTM D543)规定控制温度(常温或高温)和时间(24h~168h)。
- 取出后清洗干燥,评估外观和性能变化。
- 关键参数:
- 溶剂类型(极性与非极性溶剂组合测试);
- 浸泡温度(通常为23℃±2℃或根据实际工况设定);
- 浸泡时间(分阶段测试,如24h、72h、168h)。
2. 擦拭测试
- 目的:评估元件表面涂层或材料在溶剂擦拭后的耐擦洗性。
- 方法:
- 使用无纺布或棉布蘸取溶剂(如异丙醇、丙酮),以固定压力(如1kg)和频率(如10次/min)擦拭元件表面。
- 记录涂层脱落、变色或表面损伤情况。
- 标准参考:ASTM D5402(涂层耐溶剂擦拭性测试)。
3. 温度循环溶剂暴露测试
- 目的:验证溶剂暴露与温度变化协同作用下的材料稳定性。
- 方法:
- 将元件交替暴露于溶剂浸泡和高温干燥环境(如-40℃~85℃循环)。
- 循环次数通常为10~50次,观察材料疲劳或分层现象。
4. 化学兼容性测试
- 目的:分析元件材料与溶剂的化学相互作用。
- 方法:
- 通过红外光谱(FTIR)、气相色谱-质谱(GC-MS)检测溶剂浸泡前后材料的成分变化。
- 计算质量变化率:质量变化率=�2−�1�1×100%质量变化率=W1W2−W1×100%
- �1W1: 浸泡前质量;�2W2: 浸泡后干燥质量。
- 判定标准:质量变化率≤5%(依行业要求调整)。
5. 长期老化测试
- 目的:评估元件在溶剂环境中的耐久性。
- 方法:
- 将元件置于密闭容器中,注入溶剂并保持高温(如70℃)加速老化。
- 定期取样测试机械性能(如拉伸强度、硬度)和电性能(如绝缘电阻)。
三、检测结果评估标准
-
- 无可见裂纹、起泡、脱落或明显变色(目视或显微镜观察);
- 表面光泽度变化≤20%(使用光泽度仪测量)。
-
- 拉伸强度、断裂伸长率等指标下降≤15%;
- 硬度变化(邵氏硬度)≤5%。
-
- 电子元件:绝缘电阻≥1×10⁹Ω,导通电阻变化≤10%;
- 密封件:泄漏率符合设计要求(如≤1×10⁻⁶ Pa·m³/s)。
四、测试溶剂的选择原则
- 实际使用场景匹配:优先选择元件工作环境中可能接触的溶剂。
- 标准溶剂列表(参考IPC-TM-650或ISO 1817):
- 极性溶剂:去离子水、乙醇、丙酮;
- 非极性溶剂:二甲苯、正己烷、矿物油;
- 腐蚀性溶剂:盐酸(5%)、氢氧化钠(5%)。
五、案例分析
- 测试要求:连接器在汽油、防冻液环境中需保持密封性和导电性。
- 检测项目:
- 浸泡测试(120h,40℃汽油环境);
- 擦拭测试(异丙醇,50次循环);
- 绝缘电阻测试(≥100MΩ)。
- 结果:连接器表面无膨胀,绝缘电阻下降≤8%,判定合格。
六、总结
上一篇:最大发射极-基极截止电流检测下一篇:气候序列-低温试验检测
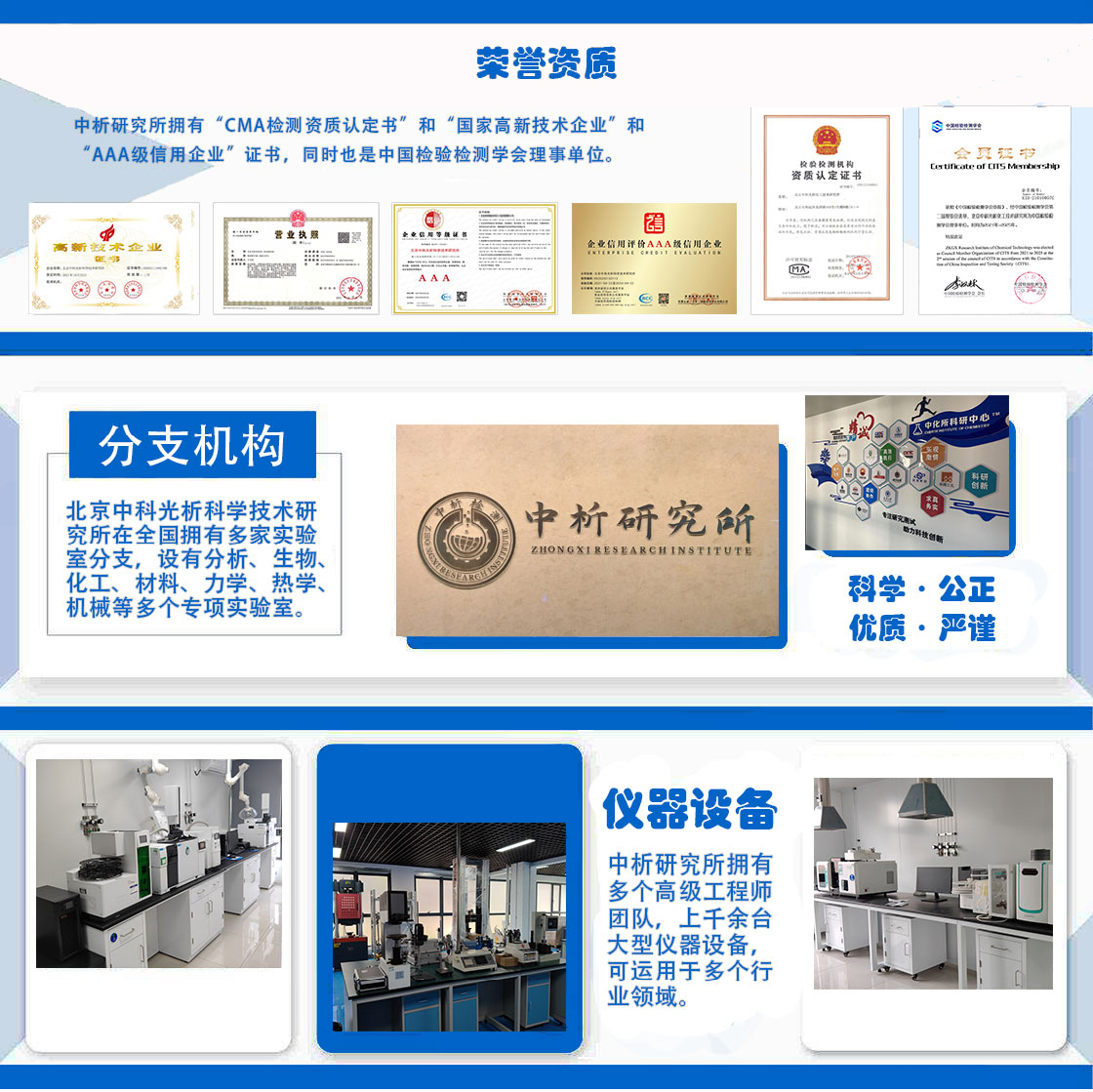
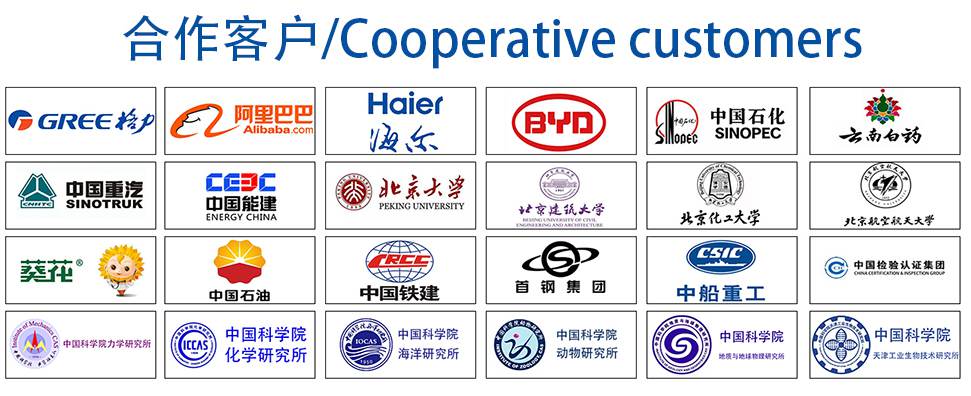
材料实验室
热门检测
269
227
202
211
208
211
222
216
228
228
212
212
215
213
206
204
221
207
219
213
推荐检测
联系电话
400-635-0567