元件耐溶剂检测:关键检测项目与实施规范
一、耐溶剂检测的核心目的
- 物理稳定性:外观无腐蚀、变形或分层;
- 化学兼容性:材料不发生溶胀、溶解或化学反应;
- 功能保持性:电气性能、机械强度符合要求。
二、核心检测项目及方法
-
- 常用溶剂:异丙醇(IPA)、丙酮、乙醇、甲苯、二甲苯、去离子水等;
- 特殊溶剂:根据应用场景选择(如医疗设备需测试消毒用乙醇、汽车行业测试燃油添加剂);
- 测试原则:覆盖元件可能接触的全部溶剂类别。
-
- 方法:将元件完全浸入溶剂(常温或加热至指定温度),持续1~24小时;
- 评估指标:
- 质量变化率(溶胀率≤5%为合格);
- 表面光泽度、颜色变化(与标准色卡对比);
- 电气性能(如绝缘电阻、导通性)。
-
- 适用场景:元件表面涂层、印刷线路的耐擦拭性;
- 方法:用溶剂浸润的无纺布以固定压力(如500g/cm²)往复擦拭表面50~100次;
- 评估重点:涂层脱落、文字模糊、金属暴露等缺陷。
-
- 仪器检测:使用SEM(扫描电镜)观察表面微观结构变化;
- 成分分析:通过FTIR(红外光谱)检测材料是否发生化学降解。
-
- 模拟严苛环境:在高温(如85℃)和低温(-40℃)下交替暴露,测试溶剂与温度共同作用的影响;
- 典型标准:IPC-TM-650 2.3.3。
-
- 重复暴露测试:多次循环“浸泡-干燥”过程(如100次循环),评估材料疲劳特性;
- 加速老化测试:通过提高溶剂浓度或温度加速老化(如85℃/85%RH环境)。
三、检测标准与结果判定
-
- IPC-TM-650:电子行业通用测试方法;
- ISO 2812-1:涂层耐液体测试标准;
- ASTM D543:塑料耐化学性评估;
- IEC 60068-2-45:环境试验标准。
-
- 外观:无裂纹、起泡、脱落(通过10倍放大镜检查);
- 电气性能:绝缘电阻下降不超过20%,导通电阻变化<10%;
- 机械强度:抗拉强度、硬度变化率≤15%。
四、行业应用案例
- 汽车电子:燃油泵电路板需通过120小时汽油浸泡测试;
- 医疗设备:内窥镜元件需耐受75%乙醇反复擦拭500次;
- 消费电子:手机按键涂层需通过50次异丙醇擦拭无脱落。
五、检测流程优化建议
- 预处理:测试前对元件进行24小时恒温恒湿(25℃/50%RH)处理;
- 数据记录:记录溶剂浓度、温度、暴露时间等参数,确保结果可追溯;
- 失效分析:对不合格样品进行断面分析,定位材料或工艺缺陷。
六、
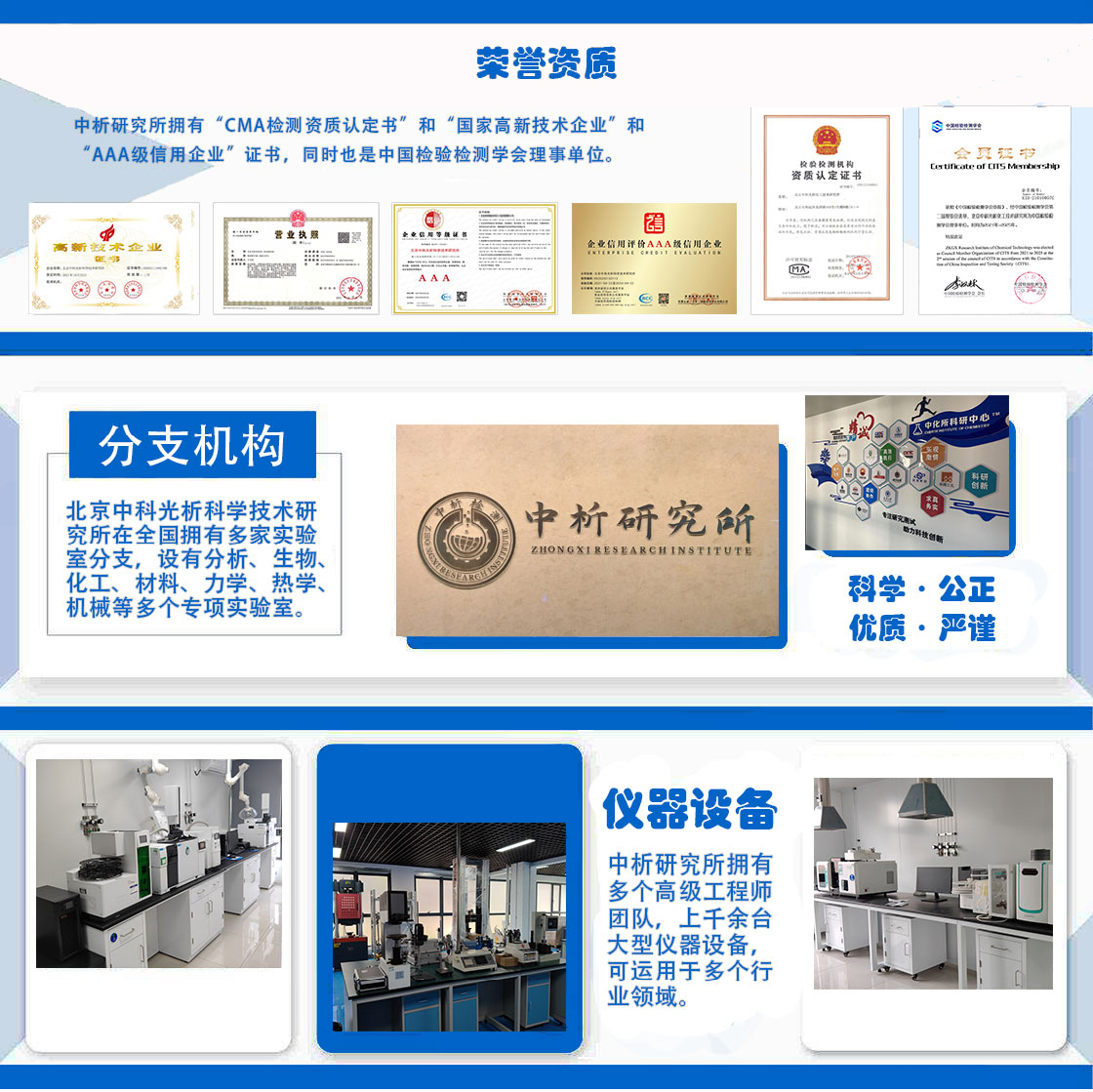
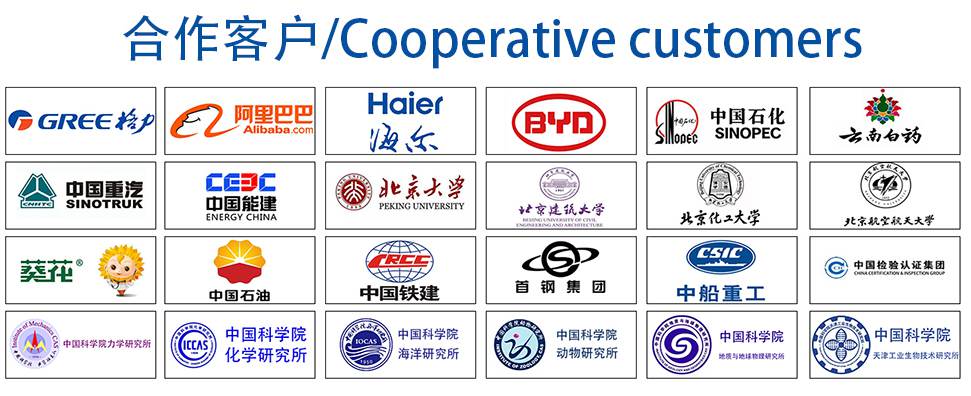
材料实验室
热门检测
271
227
202
211
210
213
225
218
228
229
213
213
218
216
210
205
221
207
220
214
推荐检测
联系电话
400-635-0567