热滥用检测:核心检测项目详解
一、热滥用检测的核心项目
-
- 目的:评估产品在长期高温环境下的稳定性。
- 测试方法:将样品置于恒温箱中,在设定温度(如60°C、85°C或更高)下存储数小时至数周。
- 关键指标:观察外观变形、材料老化、容量衰减(如电池)、密封性等。
- 标准参考:IEC 62133(电池)、GB/T 2423.2(电子设备)。
-
- 目的:验证产品在剧烈温度变化下的耐受能力。
- 测试方法:在高温(如85°C)和低温(如-40°C)间快速切换,每个极端保持30分钟至1小时,循环多次。
- 关键指标:材料开裂、焊接点脱落、电子元件失效等。
- 应用案例:汽车电子部件需通过1000次以上循环测试。
-
- 目的:模拟电池内部短路引发热失控的极端情况。
- 测试方法:
- 针刺测试:用金属针刺穿电芯,观察是否起火或爆炸。
- 过充测试:以高于额定电压充电至热失控。
- 安全标准:UN 38.3(航空运输)、GB 38031(电动汽车电池)。
-
- 目的:检测产品在高温下持续工作的可靠性。
- 测试方法:在高温环境中(如70°C)进行满负荷运行,持续数小时。
- 评估重点:性能衰减、散热效率、是否触发过热保护。
-
- 目的:评估热失控在模块或系统中的扩散风险。
- 测试方法:局部加热电池模组,监测相邻电芯温度及是否引发连锁反应。
- 行业要求:电动汽车电池系统需确保热扩散时间≥5分钟(国标要求)。
-
- 目的:检测材料在高温下的化学稳定性。
- 测试方法:
- TGA(热重分析):测量材料质量随温度的变化,确定分解温度。
- DSC(差示扫描量热法):分析材料相变或反应的热量变化。
- 应用领域:塑料、绝缘材料、粘结剂等关键组分。
二、检测方法与设备
-
- 高低温试验箱(温度范围:-70°C至+200°C)
- 热成像仪(实时监测表面温度分布)
- 充放电测试仪(电池专用)
- 数据采集系统(记录温度、电压、形变等参数)
-
- 预处理:样品在标准环境中稳定24小时。
- 测试执行:按标准设定温度曲线或触发条件。
- 结果评估:检测泄漏、膨胀、起火等失效模式,并进行性能复测。
三、行业应用与标准差异
- 消费电子产品:侧重高温运行和存储测试(如手机在50°C下充电)。
- 动力电池:需通过针刺、过充、热扩散等强制性安全测试。
- 航空航天:材料需满足MIL-STD-810G极端温度循环标准。
四、未来趋势
- 智能化监测:嵌入温度传感器和AI算法,实现热失效预警。
- 仿真技术应用:通过COMSOL等软件模拟热滥用场景,减少实测成本。
- 更高测试标准:随着快充技术发展,测试温度可能提升至150°C以上。
五、结语
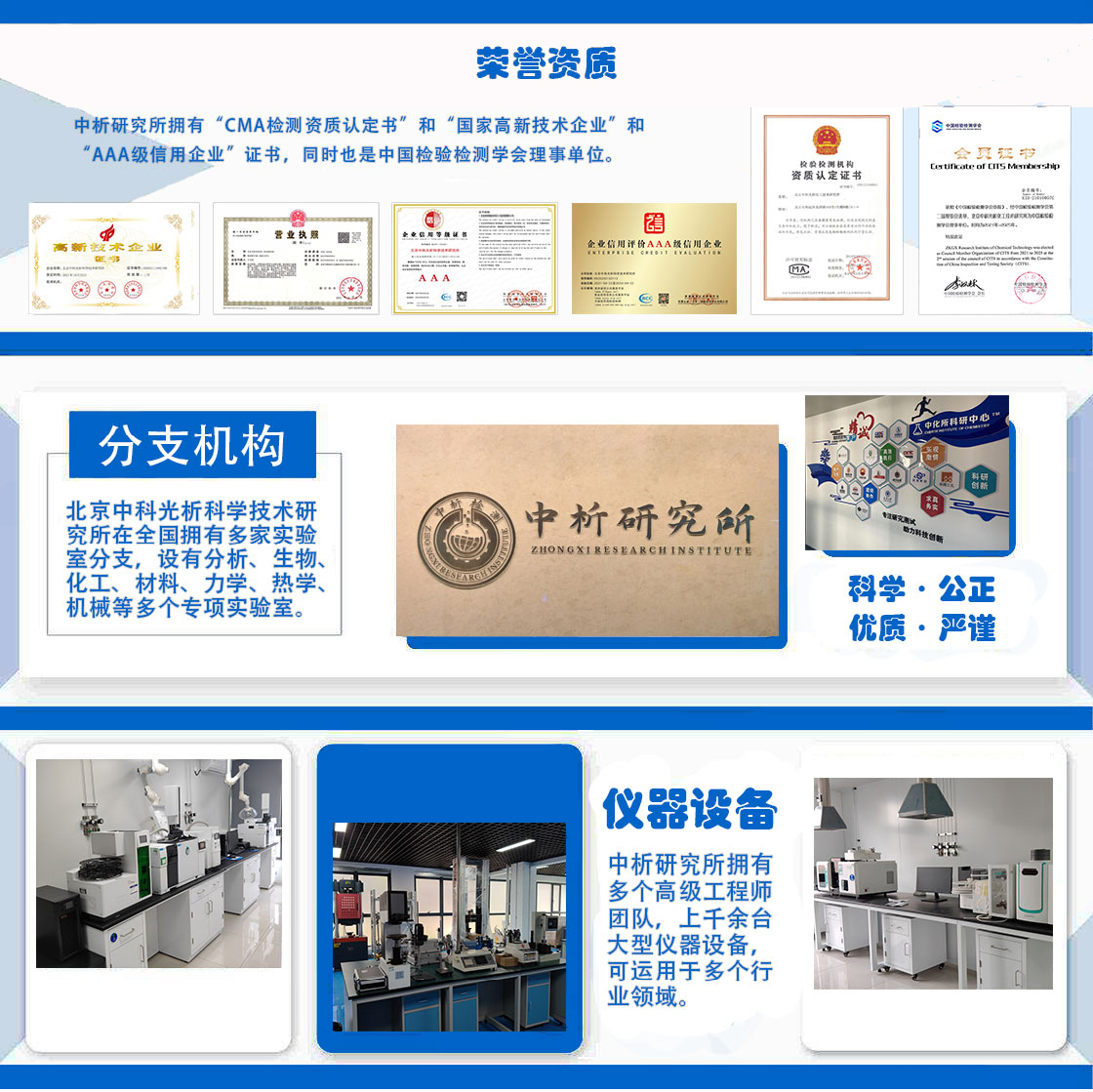
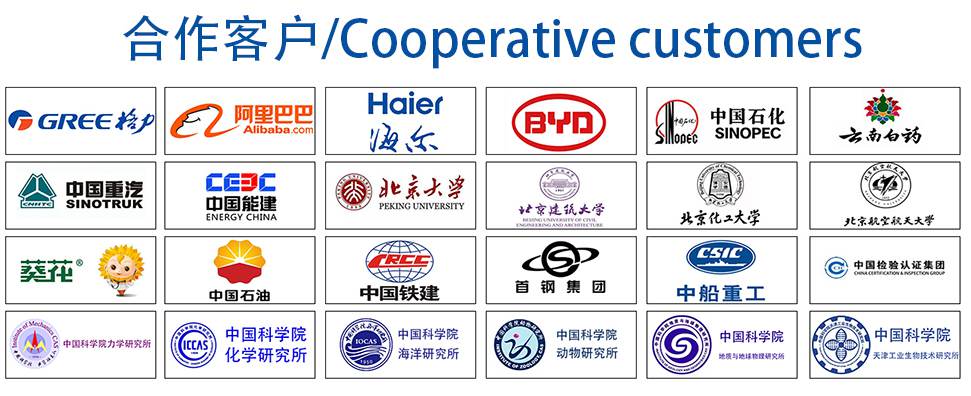
材料实验室
热门检测
254
215
189
203
197
204
209
201
207
217
203
199
197
203
196
195
207
199
209
201
推荐检测
联系电话
400-635-0567