外形尺寸及外观质量检测指南
一、概述
二、外形尺寸检测项目
1. 关键尺寸测量
- 长度/宽度/高度:使用卡尺、千分尺或三坐标测量仪(CMM)验证关键部位尺寸是否符合公差要求。
- 直径/圆度:轴类、孔类部件的直径公差检测,圆度偏差需≤0.01mm(视行业标准)。
- 角度/弧度:斜面、弯曲部件的角度公差检测(如±0.5°),利用角度规或光学投影仪。
- 位置公差:
- 同心度:旋转部件的轴心偏移量;
- 平行度/垂直度:平面间相对位置偏差;
- 对称度:对称结构中心偏移量。
2. 轮廓匹配度
- 3D轮廓扫描:通过三维激光扫描仪对比实际产品与CAD模型的匹配度,生成偏差色谱图(如±0.05mm为合格)。
三、外观质量检测项目
1. 表面缺陷检测
- 划痕/凹痕:长度>0.5mm或深度>0.1mm视为不合格(电子行业标准)。
- 裂纹/气泡:通过显微镜或工业内窥镜检测内部隐形缺陷。
- 毛刺/飞边:注塑或冲压件边缘毛刺高度需≤0.05mm。
- 腐蚀/氧化:金属件表面锈斑面积超过5%需返工。
2. 涂层与镀层质量
- 颜色一致性:使用色差仪(ΔE<1.5为合格)。
- 光泽度:60°角光泽度仪检测,偏差≤10%标准值。
- 附着力测试:划格法(ASTM D3359)或胶带剥离试验,涂层脱落面积<5%为合格。
- 厚度均匀性:涂层测厚仪检测,如电镀层厚度公差±2μm。
3. 标识与印刷质量
- 字符清晰度:目视或OCR系统识别,字符缺损率<3%。
- 条码/二维码:扫描成功率需达100%,对比度≥70%。
- 标签贴合度:无翘边、气泡,位置偏差±1mm内。
4. 装配完整性
- 间隙检查:塞尺测量装配间隙(如车门缝隙≤2mm)。
- 错位/偏移:视觉检测系统判定部件对齐度(如PCB元件偏移<0.1mm)。
四、检测方法与工具
检测类型 | 常用工具 | 精度范围 | 适用场景 |
---|---|---|---|
传统测量 | 游标卡尺、高度规 | ±0.02mm | 简单几何尺寸抽检 |
光学测量 | 影像测量仪、激光扫描仪 | ±0.001mm | 复杂轮廓全尺寸检测 |
自动化检测 | 机器视觉系统、机器人CMM | ±0.005mm | 大批量在线检测 |
无损检测 | X射线、超声波探伤仪 | 缺陷识别>50μm | 内部结构缺陷排查 |
五、检测标准依据
- 国家标准:GB/T 1804(一般公差)、GB/T 1184(形状位置公差)。
- 行业标准:汽车行业ISO 9001/IATF 16949、电子行业IPC-A-610。
- 国际规范:ASTM E2544(3D扫描)、ISO 8503(表面粗糙度)。
- 企业内控标准:严于行业标准20%~50%的定制化公差要求。
六、常见问题与解决方案
-
- 原因:设备磨损、夹具定位误差。
- 对策:SPC过程控制,每2小时校准一次测量设备。
-
- 案例:注塑件表面银纹(材料含水率>0.02%导致)。
- 改善:原料预干燥(120℃/4h),模具温度提升10℃。
-
- 优化方案:采用温度补偿系统(20±1℃恒温环境),减少热胀冷缩影响。
七、总结
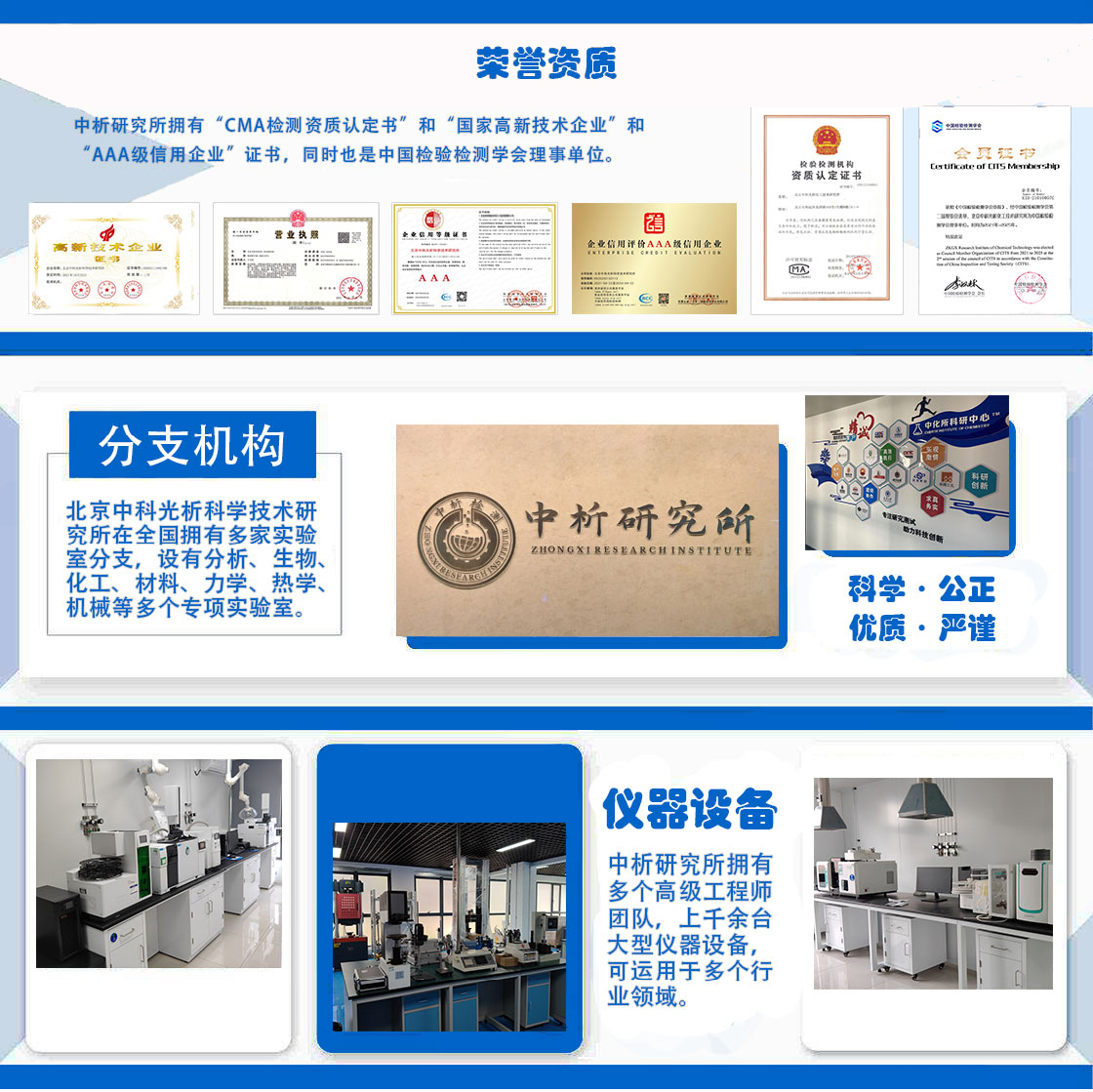
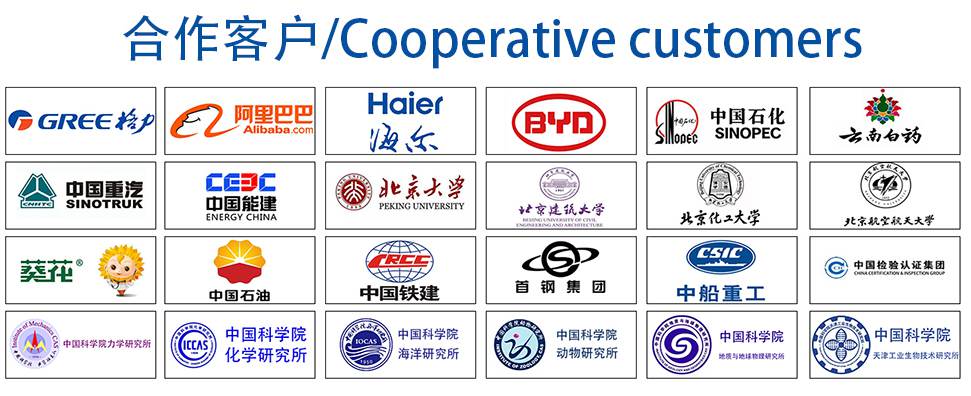
材料实验室
热门检测
253
211
188
202
195
202
207
200
206
214
202
197
195
201
194
192
205
197
206
200
推荐检测
联系电话
400-635-0567