一、玻璃化温度的基本概念
二、玻璃化温度检测的核心项目
1. 基础热性能参数检测
- 检测项目:
- 玻璃化温度值(��Tg):通过热分析方法(如DSC、DMA等)测定材料的热力学转变点。
- 转变区间宽度:��Tg由多个参数(如起始温度、中点温度、终止温度)表征,需明确区分。
- 检测方法:
- 差示扫描量热法(DSC):通过吸热/放热峰的拐点确定��Tg。
- 动态力学分析(DMA):依据储能模量(�′E′)下降或损耗因子(tan�tanδ)峰值确定��Tg。
- 热机械分析(TMA):通过材料膨胀系数突变定位��Tg。
2. 热力学性能相关检测
- 热膨胀系数(CTE):
- 检测玻璃态与高弹态下的体积膨胀差异,评估材料在温度变化中的尺寸稳定性(尤其在电子封装领域)。
- 比热容变化:
- 通过DSC测量��Tg前后的比热容跃升幅度,分析分子链段运动的能量变化。
3. 力学性能关联检测
- 动态模量衰减:
- 利用DMA测试储能模量(�′E′)和损耗模量(�′′E′′),量化材料在��Tg附近的刚度变化。
- 低温脆性:
- 评估材料在��Tg以下的抗冲击性能(如塑料、橡胶制品的低温适用性)。
4. 微观结构与组分影响检测
- 交联度与分子量分布:
- 高交联度材料的��Tg通常较高,需结合凝胶渗透色谱(GPC)分析分子量对��Tg的影响。
- 增塑剂含量:
- 增塑剂会显著降低��Tg,需通过组分分析(如FTIR、GC-MS)验证其对��Tg的调控效果。
5. 环境因素影响检测
- 湿热老化后��Tg变化:
- 模拟潮湿高温环境下材料的��Tg漂移,评估吸湿性对材料稳定性的影响(如环氧树脂封装材料)。
- 紫外老化后动态性能:
- 检测光照后材料的��Tg变化,分析光降解对材料耐候性的影响。
6. 应用性能匹配性检测
- 加工温度窗口:
- 确定材料的加工温度范围(需高于��Tg但低于分解温度)。
- 服役温度极限:
- 结合��Tg与材料实际使用温度,评估其在高温或低温环境中的可靠性。
三、检测方法的选择与对比
方法 | 原理 | 适用材料 | 检测灵敏度 |
---|---|---|---|
DSC | 热流变化监测相变 | 高分子、非晶合金 | 高(微克级) |
DMA | 动态力学响应分析 | 弹性体、复合材料 | 极高(纳米级) |
TMA | 热膨胀系数突变定位 | 薄膜、涂层材料 | 中等 |
介电分析 | 介电常数随温度变化 | 绝缘材料、功能高分子 | 高 |
四、检测难点与注意事项
- 样品制备:
- 需确保样品无残留应力或结晶(可通过退火处理消除热历史)。
- 升温速率影响:
- 升温速率过快可能导致��Tg测定值偏高,需根据标准(如ISO 11357)设定合理参数。
- 多组分材料干扰:
- 共混材料可能出现多个��Tg峰,需结合组分分析明确归属。
五、应用案例
- 电子封装材料:
- 测定环氧树脂的��Tg(通常需>150℃),确保芯片封装在高温下的尺寸稳定性。
- 橡胶轮胎:
- 通过DMA分析橡胶的��Tg与损耗因子,优化低温抓地力与高温抗疲劳性。
六、总结
上一篇:刚性印制板的针焰试验检测下一篇:最大允许电流/电压检测
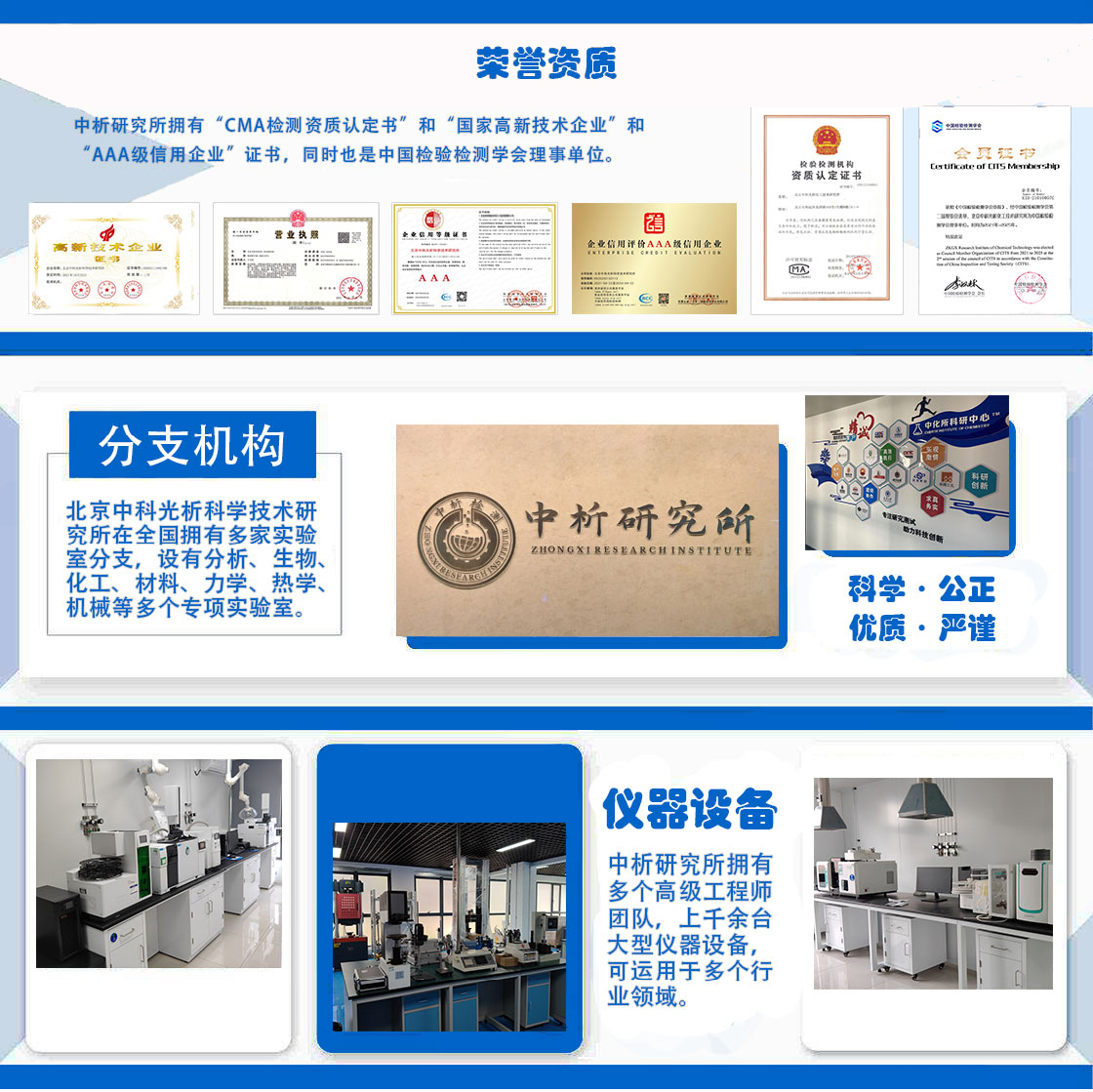
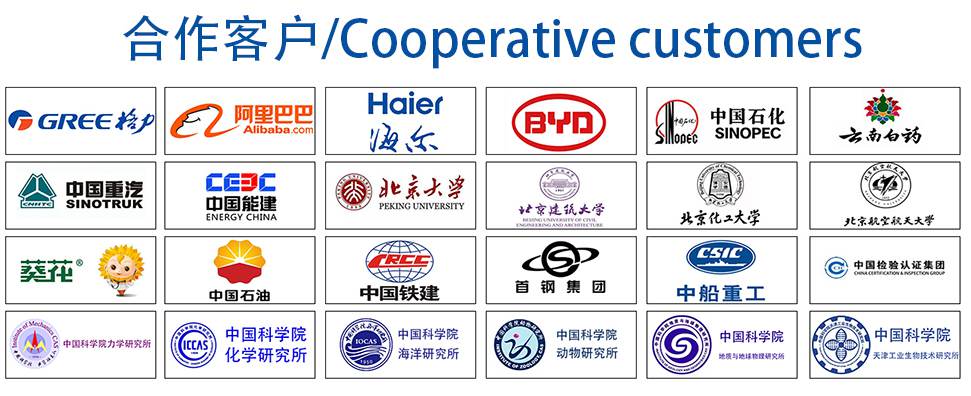
材料实验室
热门检测
254
214
189
203
196
204
209
201
207
217
203
199
197
203
195
193
207
198
209
201
推荐检测
联系电话
400-635-0567