基材检测的核心项目与关键技术解析
一、物理性能检测:基础质量的保障
-
- 项目内容:几何尺寸精度、表面平整度、裂纹、气孔、划痕等缺陷。
- 技术手段:三坐标测量仪、光学投影仪、工业内窥镜。
- 意义:直接影响基材的装配适用性和外观质量。
-
- 方法:阿基米德排水法、气体置换法。
- 应用:评估烧结材料(如陶瓷、粉末冶金件)的致密性。
-
- 关键参数:热膨胀系数、导热系数、玻璃化转变温度(高分子材料)。
- 设备:热机械分析仪(TMA)、差示扫描量热仪(DSC)。
二、化学成分检测:确保材料本质合规
-
- 技术:X射线荧光光谱(XRF)、电感耦合等离子体发射光谱(ICP-OES)。
- 目的:验证金属合金成分或塑料添加剂是否符合标准。
-
- 重点对象:RoHS受限物质(铅、镉等)、REACH高关注物质(SVHC)。
- 方法:气相色谱-质谱联用(GC-MS)、原子吸收光谱(AAS)。
三、机械性能检测:力学行为的核心评估
-
- 拉伸试验:测定抗拉强度、屈服强度、断后伸长率(ASTM E8/E21)。
- 弯曲试验:评估脆性材料的抗弯性能(如陶瓷、玻璃)。
-
- 方法选择:金属常用洛氏(HRC)、布氏(HB);橡胶用邵氏硬度(ASTM D2240)。
-
- 设备:摆锤冲击试验机(夏比冲击试验,ISO 148)。
四、环境与耐久性测试:模拟极端服役条件
-
- 盐雾试验:模拟海洋或工业环境(ASTM B117)。
- 电化学测试:极化曲线法评估金属腐蚀速率。
-
- 紫外老化:评估塑料、涂料的光稳定性(ISO 4892)。
- 湿热循环:检测材料在高湿度下的性能衰减。
五、微观结构分析:揭示性能的本质原因
-
- 步骤:切割→镶嵌→抛光→蚀刻→显微镜观察。
- 应用:检测金属晶粒度、夹杂物分布。
-
- 功能:观察微观形貌、分析局部成分(如断口分析)。
六、无损检测(NDT):高效与安全的平衡
-
- 适用场景:检测内部裂纹、分层(复合材料)。
-
- 优势:直观显示铸件、焊缝的内部缺陷。
-
- 应用:导电材料的表面及近表面缺陷检测。
七、检测标准与设备选择原则
- 国际标准:ISO、ASTM、DIN、JIS等根据不同行业选用。
- 设备匹配:根据检测精度、效率、成本综合考量(如实验室级vs在线检测系统)。
八、检测流程优化建议
- 分阶段检测:原材料入场→加工过程→成品出厂。
- 数据化管理:采用LIMS系统整合检测数据,实现可追溯性。
结语
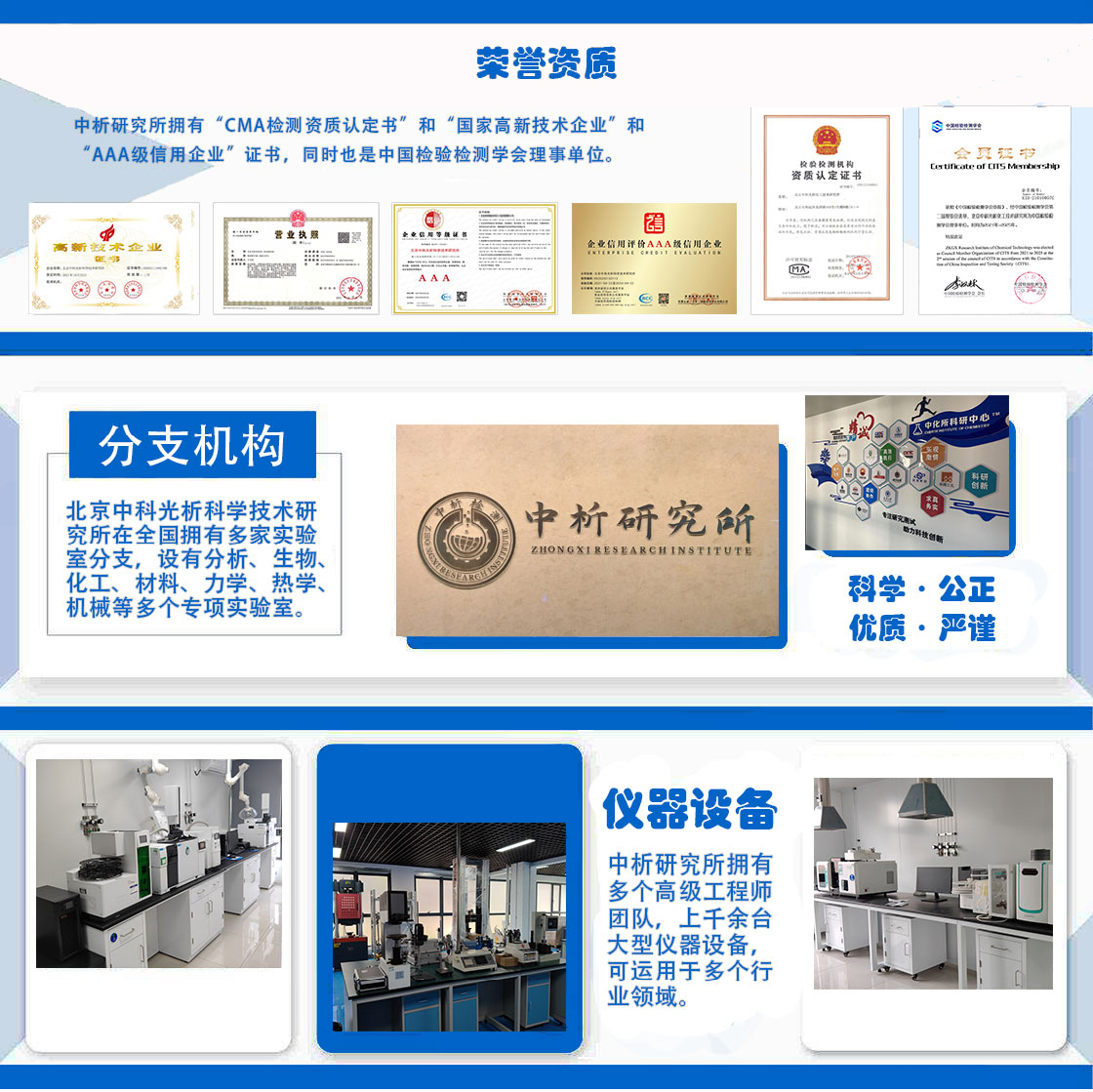
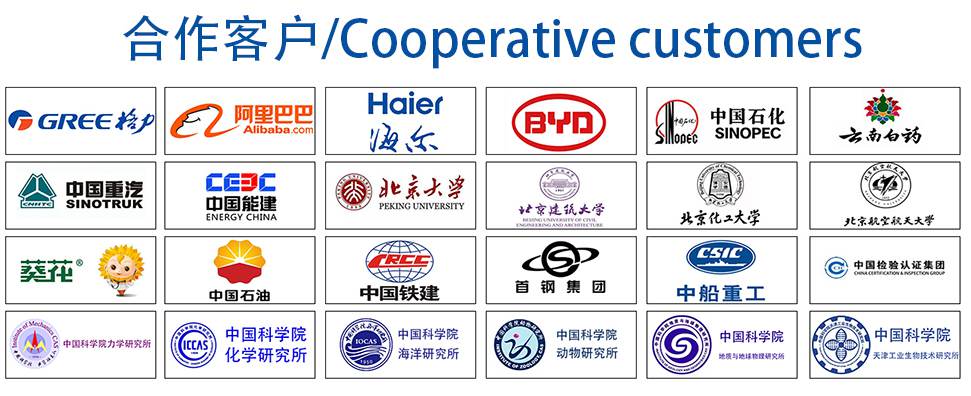
材料实验室
热门检测
254
214
189
203
196
204
209
201
207
217
203
199
197
203
195
193
207
198
209
201
推荐检测
联系电话
400-635-0567