一、核心检测项目
1. 目视检查(基础检测)
- 检测目标:发现肉眼可见的物理缺陷。
- 重点检查项:
- 焊接点:虚焊、冷焊、焊锡桥接(可能导致短路)。
- PCB走线:断裂、铜箔剥落(开路)、相邻走线接触(短路)。
- 元件状态:烧焦、鼓包、引脚弯曲或脱落。
- 工具:放大镜、显微镜。
- 优点:成本低、速度快;缺点:依赖经验,无法检测内部缺陷。
2. 万用表检测(通断与电阻测试)
- 开路检测:
- 切换到“蜂鸣档”或“电阻档”,测量两点间电阻。若电阻无限大(无蜂鸣声),则存在开路。
- 短路检测:
- 测量非导通点间的电阻,若电阻接近零,则存在短路。
- 关键技巧:
- 断电检测,避免误判。
- 对比正常电路参数,定位异常区域。
3. 飞针测试(高精度点对点检测)
- 原理:通过移动探针接触测试点,验证电路连通性。
- 适用场景:小批量PCB原型验证或维修。
- 优势:无需专用治具,灵活性强;局限性:速度慢,不适合量产。
4. 自动光学检测(AOI)
- 功能:通过高清摄像头扫描PCB,比对设计文件识别缺陷。
- 检测项目:
- 元件错位、极性反接。
- 焊锡不足或过量(潜在短路风险)。
- 表面走线断裂。
- 适用阶段:SMT贴片后或焊接工序后。
5. X射线检测(内部缺陷分析)
- 核心应用:
- BGA封装:焊球虚焊、空洞。
- 多层PCB:内层走线短路或开路。
- 优势:非破坏性检测,穿透性强。
6. 在线测试(ICT)
- 原理:通过定制治具连接测试点,全面验证电路功能。
- 测试内容:
- 所有节点的电压、电阻、电容。
- 模拟信号完整性(如阻抗匹配)。
- 适用场景:量产阶段的全检或抽检。
7. 功能测试(系统级验证)
- 方法:在通电状态下验证设备整体功能。
- 检测项:
- 电源模块输出是否正常。
- 信号传输路径是否畅通(如通信接口)。
- 负载状态下是否异常发热。
8. 热成像检测(异常发热定位)
- 应用场景:
- 短路点因电流过大导致局部高温。
- 开路引发的元件过热(如保险丝熔断后负载异常)。
- 工具:红外热像仪。
- 注意:需在安全电流下进行,避免二次损坏。
二、检测流程优化建议
-
- 生产前:检查PCB设计合理性(如测试点布局)。
- 生产中:AOI + 飞针测试结合,实时拦截缺陷。
- 出货前:ICT + 功能测试确保可靠性。
-
- 避免静电、湿度对检测结果的影响。
- 高精度检测需在恒温环境下进行。
-
- 建立标准参数库,自动比对异常值(如ICT测试数据)。
三、常见问题与对策
- 误报问题:
- AOI可能因反光误判焊点质量,需人工复检。
- 万用表探针接触不良导致误判开路,需清洁测试点。
- 隐蔽性故障:
- 间歇性开路(如应力断裂):通过振动测试模拟验证。
- 多层板内层短路:依赖X射线或分层扫描。
四、总结
- 研发阶段:万用表 + 飞针测试 + 热成像。
- 量产阶段:AOI + ICT + X射线组合。
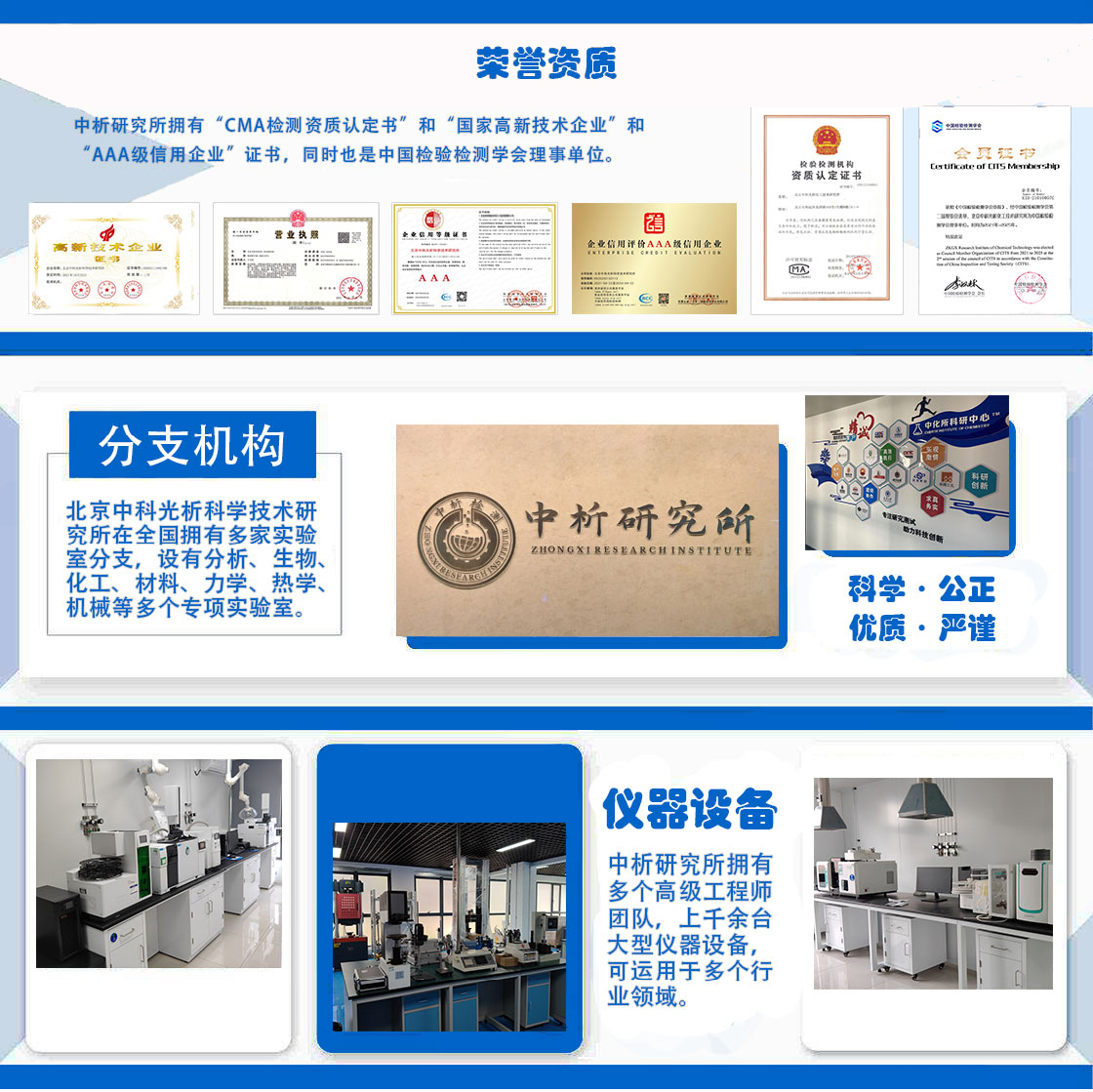
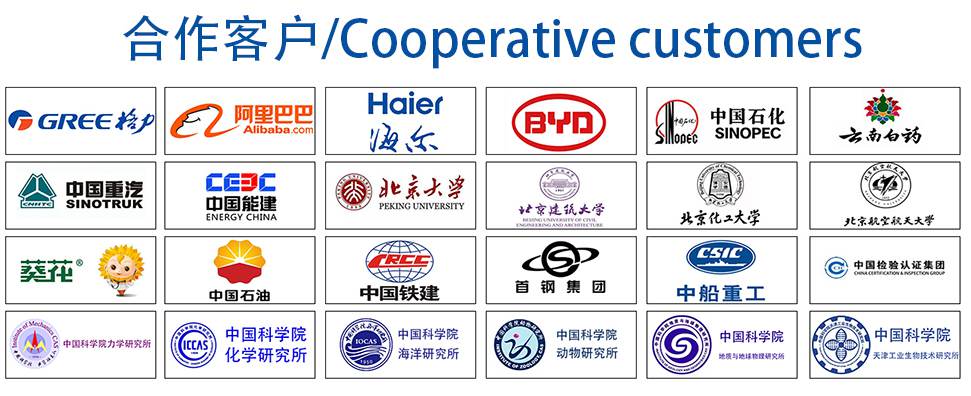
材料实验室
热门检测
269
227
202
211
208
211
223
217
228
229
212
213
216
214
207
204
221
207
220
213
推荐检测
联系电话
400-635-0567