温度循环检测:核心检测项目详解
一、核心检测项目分解体系
- 温度范围设定:军用器件要求-65℃~+150℃(MIL-STD-883标准),新能源汽车部件标准-40℃~+105℃(ISO 16750)
- 极限值保持验证:在温度极值点进行≥30分钟的保温试验,检测材料相变、密封件蠕变等失效模式
- 梯度步进检测:以5℃/步长分段测试,精准定位失效临界温度点
- 转换速率控制:液氮冲击箱实现30℃/s以上超快速温变(IEC 60068-2-14)
- 相变应力测试:验证BGA封装芯片在217℃焊料熔点附近的机械性能
- 材料CTE匹配分析:检测陶瓷基板与金属引线框架的热膨胀系数差异(Δα≤2ppm/℃)
- 周期次数设定:汽车电子要求1000次循环(AEC-Q100),航天器件需5000次(MIL-STD-202)
- 加速老化模型:运用Coffin-Manson方程计算等效使用寿命
- 失效机理分析:通过扫描电镜观察焊点裂纹扩展路径(典型龟裂形貌特征)
二、进阶检测维度
- 温湿度协同测试:85℃/85%RH条件下进行潮热-低温循环
- 机械振动叠加:三轴振动台与温箱联动测试(频率5~2000Hz,振幅3.5Grms)
- 带电工作测试:电源模块在温变过程中持续带载检测(纹波电压波动≤2%)
- 红外热成像定位:检测芯片表面0.1℃温差热点
- 声发射监测:捕捉材料开裂的20-100kHz特征频率
- 四线法电阻测量:实时监控互连电阻变化(分辨率达1μΩ)
三、检测方案设计要素
- 批次抽样原则:根据ANSI/ASQ Z1.4方案执行LTPD抽样
- 失效模式覆盖:包含典型失效件、边界样品、黄金样品
- 夹具设计规范:采用Invar合金制作低CTE测试治具
- 响应面分析法:通过Box-Behnken设计优化温变速率与保温时间
- 加速因子计算:基于Arrhenius模型推导活化能参数
- 数据归一化处理:采用Weibull分布进行寿命数据分析
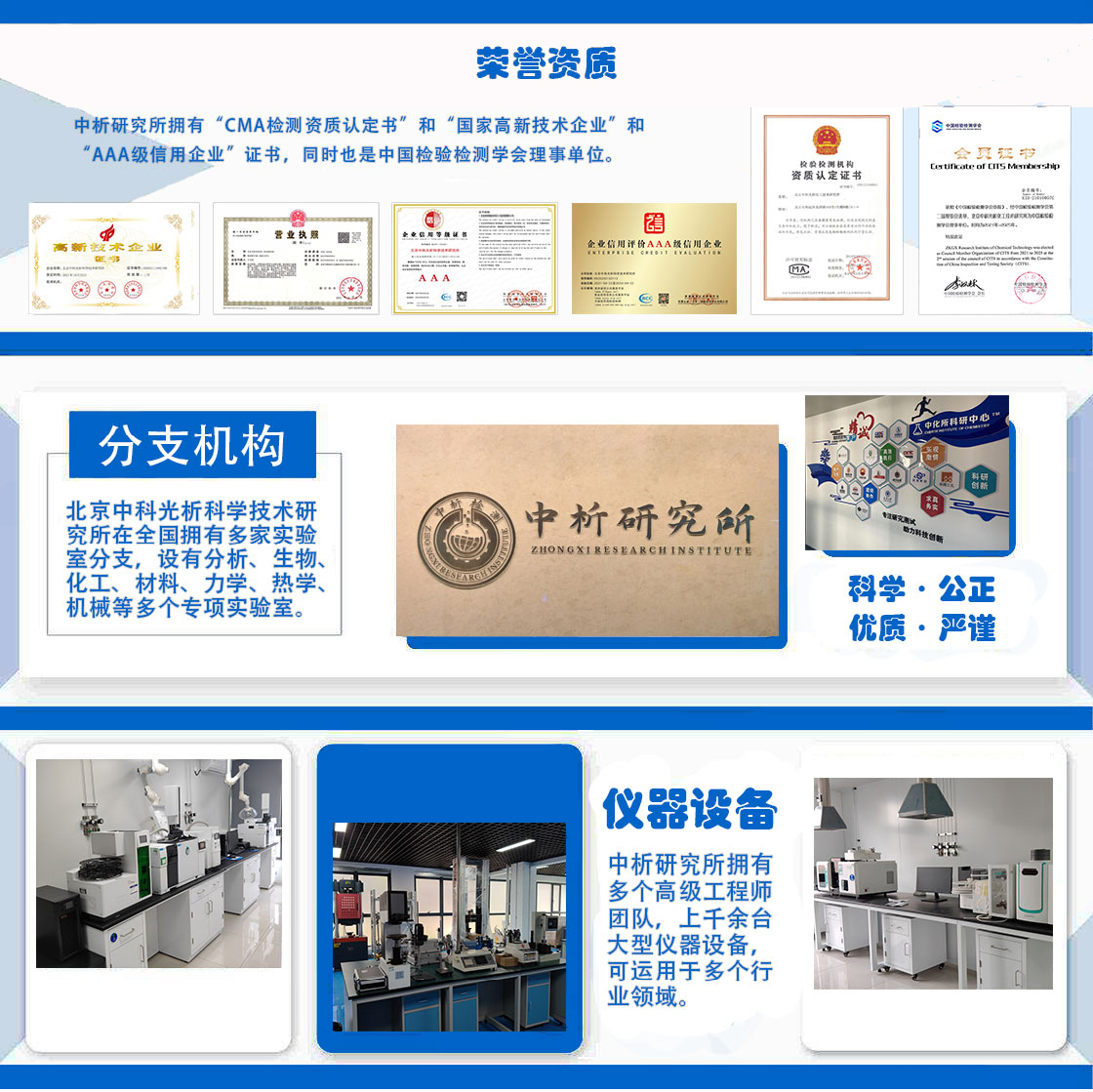
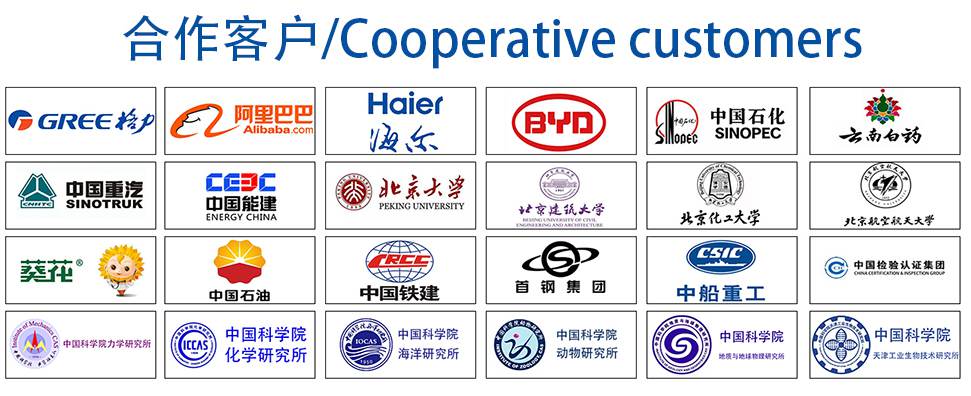
材料实验室
热门检测
271
228
202
211
210
215
225
218
228
229
215
214
218
216
210
205
221
207
220
214
推荐检测
联系电话
400-635-0567