一、机械试验检测项目
-
- 目的:模拟运输、使用过程中的振动环境,测试产品结构的疲劳寿命。
- 测试方法:
- 正弦振动:按固定频率和振幅测试共振点(如IEC 60068-2-6标准)。
- 随机振动:模拟真实环境中的复合振动(如ASTM D3580)。
- 典型应用:汽车零部件、电子设备、航空航天仪器。
-
- 目的:验证产品在突发冲击或跌落时的抗损能力。
- 测试类型:
- 半正弦波冲击:模拟运输碰撞(如ISTA 3A标准)。
- 自由跌落试验:测试产品包装或裸机的跌落耐受性(高度可达1.5米)。
- 关键参数:加速度(g值)、冲击持续时间、跌落角度。
-
- 目的:评估材料或部件在循环载荷下的寿命预测。
- 测试方法:通过高频拉伸/压缩或弯曲载荷(如ISO 12107标准),记录裂纹萌生和扩展数据。
- 应用领域:桥梁构件、发动机零件、医疗器械。
-
- 测试内容:测量材料的屈服强度、抗拉强度及弹性模量。
- 设备要求:万能材料试验机(符合ASTM E8/E9标准)。
二、气候环境试验检测项目
-
- 目的:检验产品在温度骤变(-70℃至+150℃)下的性能。
- 测试标准:GB/T 2423.1(低温)、GB/T 2423.2(高温)。
- 典型失效:元器件开裂、密封圈老化、液晶屏失效。
-
- 测试类型:
- 恒定湿热:85℃/85% RH条件下持续暴露(如IEC 60068-2-78)。
- 交变湿热:温湿度循环变化,加速材料吸湿劣化。
- 失效模式:金属氧化、绝缘性能下降、霉菌滋生(如军用装备GJB 150.9A)。
- 测试类型:
-
- 目的:评估金属部件及涂层的耐腐蚀性。
- 测试分类:
- 中性盐雾(NSS):5% NaCl溶液持续喷雾(ASTM B117)。
- 循环盐雾:结合湿热、干燥阶段(如ISO 14993)。
- 应用领域:汽车底盘、海洋设备、户外电子器件。
-
- 目的:模拟太阳光辐射对材料颜色、强度的影响。
- 测试标准:
- 紫外老化:ASTM G154(UV-A/B波段)。
- 氙灯加速老化:SAE J2527(汽车外饰件)。
-
- 场景模拟:高原或航空运输环境(如12 kPa气压)。
- 主要影响:密封产品膨胀、散热性能下降。
三、复合环境试验(三综合试验)
- 测试示例:振动+高温+湿度同步加载(如MIL-STD-810G方法)。
- 应用场景:卫星部件(太空极端环境)、电动汽车电池包(振动与温变耦合)。
四、行业应用与标准选择
- 汽车行业:侧重振动(ISO 16750)、温度冲击、EMC兼容性。
- 消费电子:跌落测试(1.2米6面跌落)、盐雾(48小时)、USB接口插拔寿命。
- 军工装备:GJB 150系列覆盖爆炸性大气、淋雨等极端条件。
五、如何选择检测服务机构
- 资质认证: 、CMA、ISTA认可实验室。
- 设备能力:是否具备快速温变箱(≥15℃/min)、多轴振动台。
- 报告权威性:符合目标市场法规(如欧盟CE认证需EN标准测试)。
结语
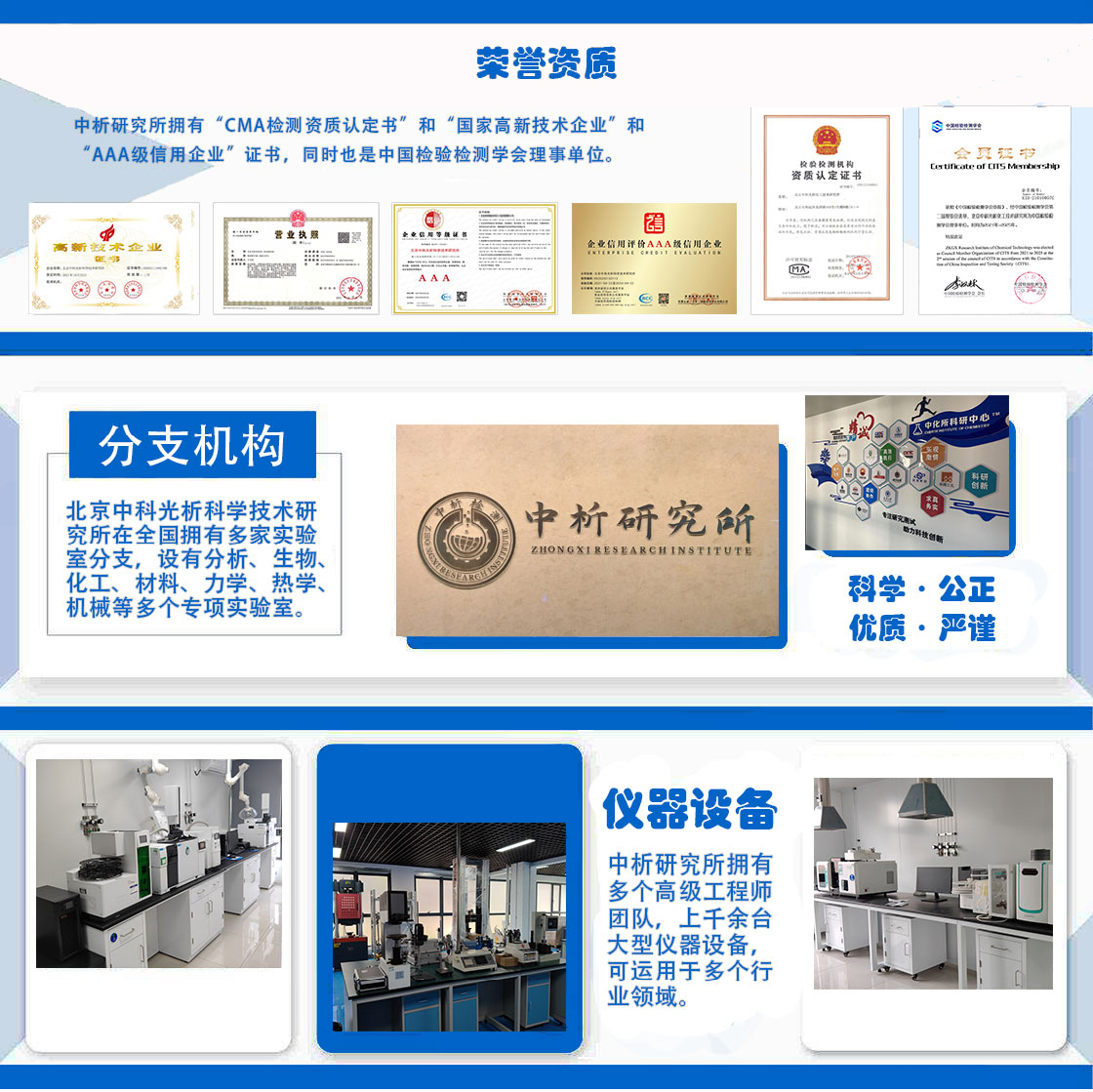
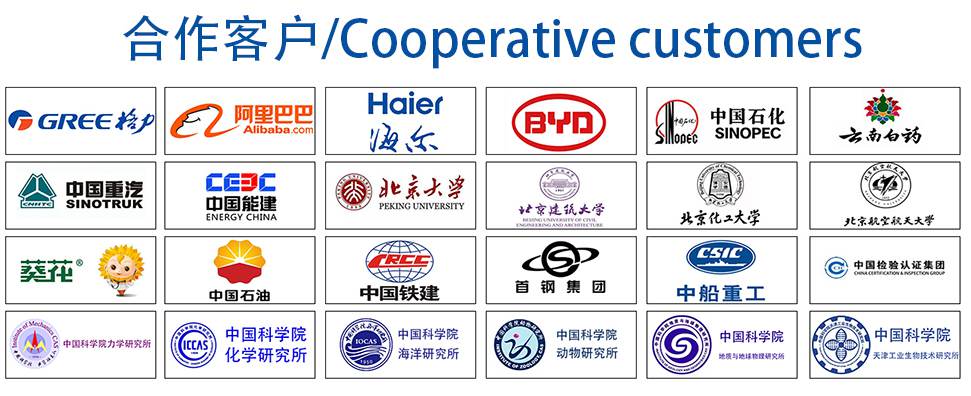
材料实验室
热门检测
253
211
188
202
195
202
207
200
206
214
202
197
195
201
194
192
205
197
206
200
推荐检测
联系电话
400-635-0567