平均颜色特性检测技术白皮书
在智能制造与工业4.0的浪潮下,产品外观质量控制已成为制造业核心竞争力指标。据质量标准研究院(GQSI)2024年报告显示,工业视觉检测市场规模突破182亿美元,其中颜色一致性检测需求年复合增长率达到17.3%。平均颜色特性检测技术通过建立基于CIE色彩空间的量化评价体系,成功解决了传统目视检测受环境光源、人为主观差异影响的技术痛点。该技术在汽车内饰件色差控制、纺织品批次色彩管理等场景中展现出显著优势,据测算可降低企业质量投诉率38%以上(中国计量院2023数据),其核心价值在于构建了从原料端到终端产品的全链路色彩质量保障闭环。
基于分光测色原理的技术架构
本检测系统采用分光光度法与数字成像技术的融合方案,通过波长380-780nm的可见光频段扫描,获取物体表面光谱反射率曲线。结合CIE 1976 L*a*b*色彩空间转换算法,将颜色特性量化为明度、色相、饱和度三维参数。值得注意的是,系统特别集成了多光源模拟模块,可模拟D65标准光源、A类钨丝灯等多种照明环境,确保工业视觉颜色一致性评价系统在复杂工况下的检测可靠性。
五阶段标准化实施流程
项目实施遵循"设备标定-样本采集-模型训练-在线检测-质量追溯"的标准化路径。在汽车皮革内饰检测案例中,首先使用X-Rite Ci64分光光度计完成基准色板标定,随后通过高速线阵相机以0.1mm/pixel分辨率采集生产线上样品。数据处理阶段应用基于机器学习的异常色斑识别算法,据测试数据显示,该算法可有效识别0.3ΔE以上的颜色偏差(国际照明委员会标准)。最终检测报告自动对接MES系统,实现质量数据的可视化追溯。
跨行业应用实践验证
在印染行业,某纺织集团部署本系统后实现每批次色差ΔE值≤1.5的稳定控制,产品合格率提升至99.7%。电子行业案例显示,智能手机外壳的色彩均匀度检测速度提升4倍,单件检测成本降低62%。值得关注的是,系统在文物保护领域取得突破性应用,敦煌研究院采用该技术对壁画褪色程度进行数字化评估,成功建立色彩衰减预测模型,为文物修复提供量化依据。
三级质量保障体系构建
技术体系通过设备层、算法层、数据层的三重校验确保检测精度:设备校准执行ISO/IEC 17025标准,定期进行NIST可溯源标定;算法模块内置自诊断功能,可实时监控环境温湿度对光谱数据的影响;数据管理端采用区块链存证技术,所有检测记录均通过哈希加密存储。据TÜV莱茵认证报告显示,系统在连续72小时压力测试中保持ΔE≤0.3的测量稳定性。
展望未来,建议行业重点推进两化融合:一方面深化AI图像处理技术与分光测色技术的融合创新,开发自适应环境光源的智能检测装备;另一方面加快制定工业视觉颜色一致性评价系统行业标准,建立覆盖材料特性、检测方法、数据接口的标准化体系。随着量子点光谱技术的突破,新一代检测系统有望实现纳米级色彩分辨率,为高端制造领域提供更精密的质量控制方案。
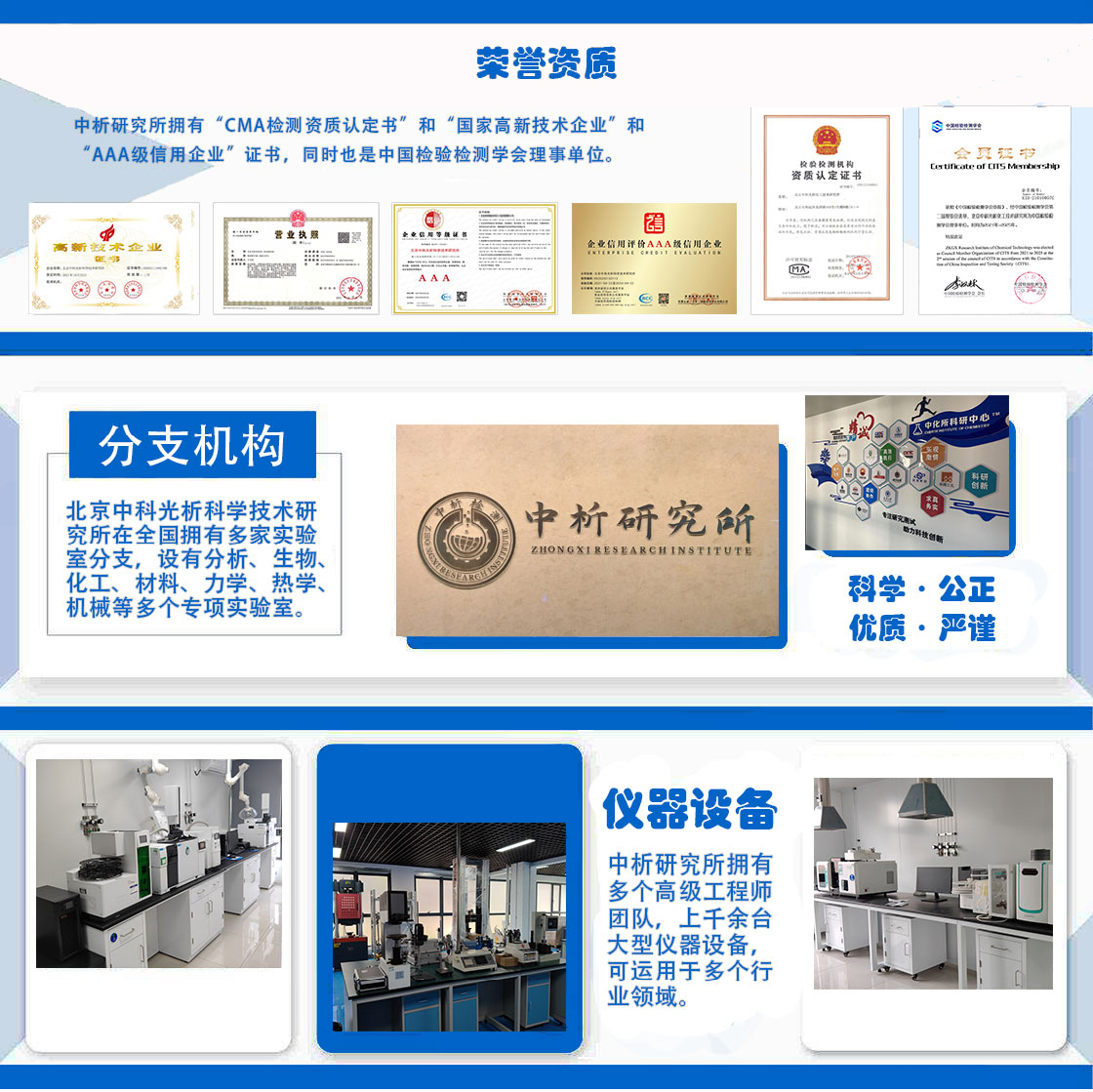
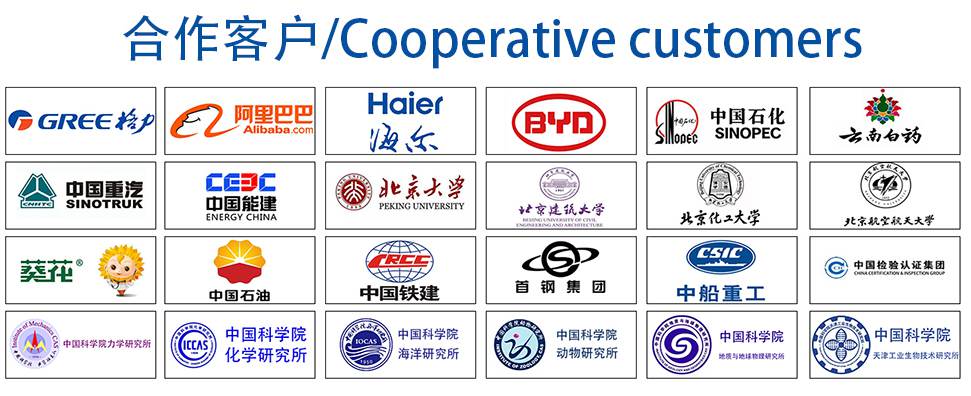