一、反向耗散功率的定义与意义
- 热稳定性:过高的反向功率会导致局部温升,引发热失控。
- 可靠性:长期反向损耗可能加速器件老化,缩短寿命。
- 电路安全:极端情况下可能造成短路或烧毁。
二、核心检测项目清单
1. 反向击穿电压(V_BR)测试
- 目的:确定器件在反向击穿时的临界电压。
- 方法:施加反向电压并逐步升高,直至漏电流达到预设阈值(如1 mA)。
- 标准依据:JEDEC JESD24、MIL-STD-750。
- 关键设备:高精度源表(SourceMeter)、示波器。
2. 反向漏电流(I_R)测量
- 测试条件:在额定反向电压(如80% V_BR)下测量稳态漏电流。
- 关注点:
- 温度依赖性(25°C至最高结温)。
- 时间稳定性(漏电流随时间的变化)。
- 数据记录:需记录漏电流-电压(I-V)曲线及温度补偿值。
3. 动态反向恢复特性
- 适用对象:快恢复二极管、整流器等。
- 检测参数:
- 反向恢复时间(t_rr)
- 反向恢复电荷(Q_rr)
- 测试电路:采用电感负载开关电路,利用双脉冲测试法。
4. 热特性分析
- 热阻(R_th)测试:通过功率循环法测量结到环境的热阻。
- 结温(T_j)监控:使用红外热成像或电学法(如V_f法)实时监测温升。
- 失效判据:结温超过器件规格书限值或出现热击穿。
5. 反向功率耐受能力(Repetitive Avalanche Energy)
- 测试场景:模拟器件在雪崩击穿状态下的能量吸收能力。
- 关键指标:
- 单脉冲雪崩能量(E_AS)
- 重复雪崩能量(E_AR)
- 设备要求:雪崩测试仪、能量回收电路。
三、检测流程与注意事项
1. 标准检测流程
- 预处理:器件恒温老化(如85°C/85%RH,48小时)。
- 静态参数测试:V_BR、I_R、热阻。
- 动态特性测试:反向恢复时间、雪崩能量。
- 极限条件验证:高温(125°C)、低温(-40°C)下的反向特性。
- 失效分析:对异常样本进行SEM/EDS微观结构分析。
2. 常见问题与解决方案
问题现象 | 潜在原因 | 改进措施 |
---|---|---|
反向漏电流超标 | 表面污染、晶格缺陷 | 优化封装工艺、退火处理 |
击穿电压离散性大 | 材料掺杂不均匀 | 加强晶圆级参数筛选 |
雪崩能量耐受性不足 | 芯片散热设计缺陷 | 改进金属化层或添加散热结构 |
四、应用案例:汽车级IGBT模块检测
- 高温反偏(HTRB)测试:150°C下施加1200V反向电压1000小时,监测漏电流漂移。
- 雪崩能量循环测试:模拟电机堵转时的能量冲击,验证E_AR ≥ 500mJ。
- 有限元热仿真:结合实测数据优化封装结构,降低热阻20%。
五、前沿技术趋势
- 在线监测系统:集成温度-电流-电压多参数同步采集,实现实时预警。
- AI辅助分析:利用机器学习预测器件寿命与失效模式。
- 宽禁带半导体测试:针对SiC/GaN器件的高频、高温特性开发专用检测协议。
结语
上一篇:机械耐久性/寿命检测下一篇:铜上镀金层孔隙率检测
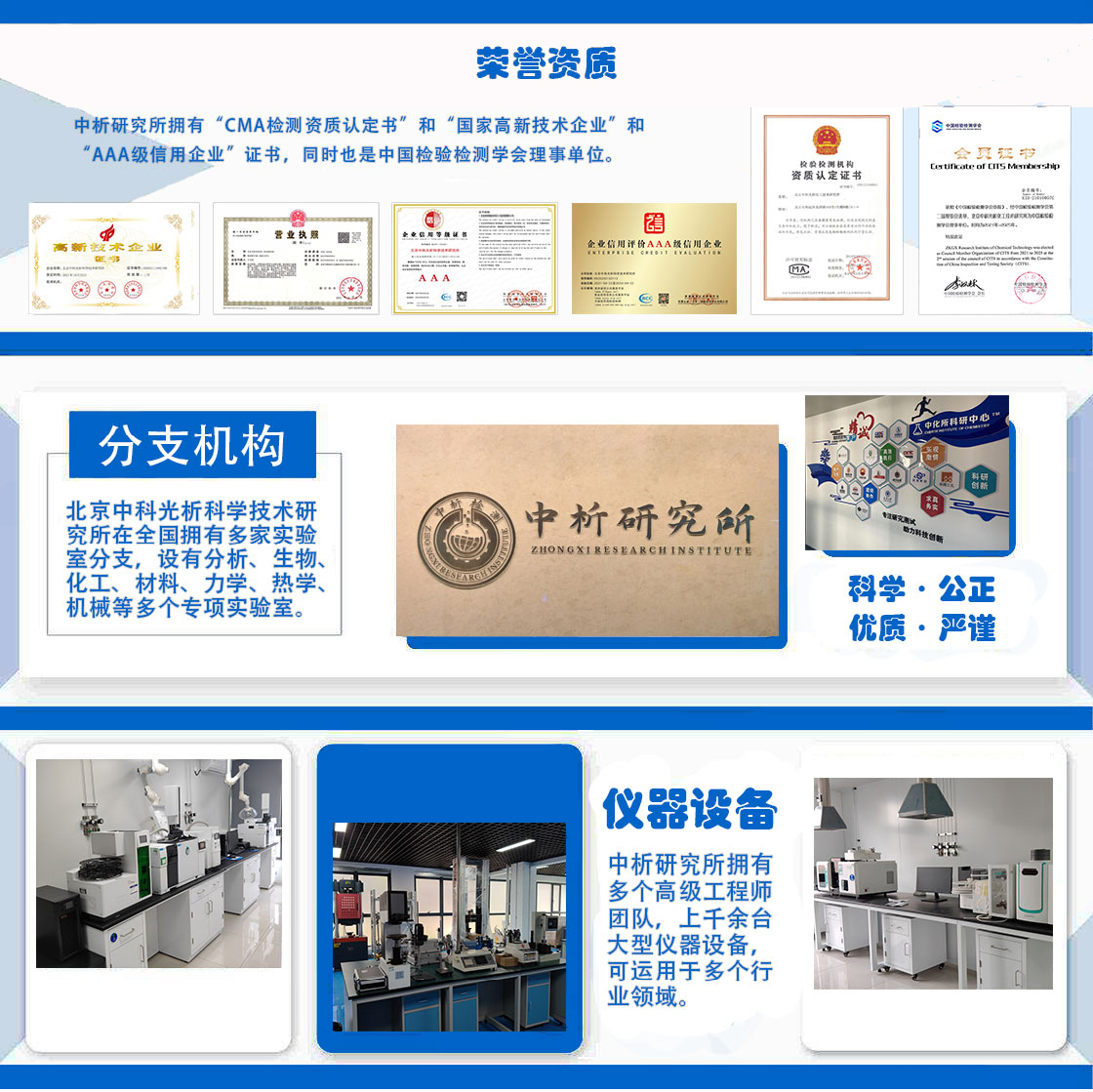
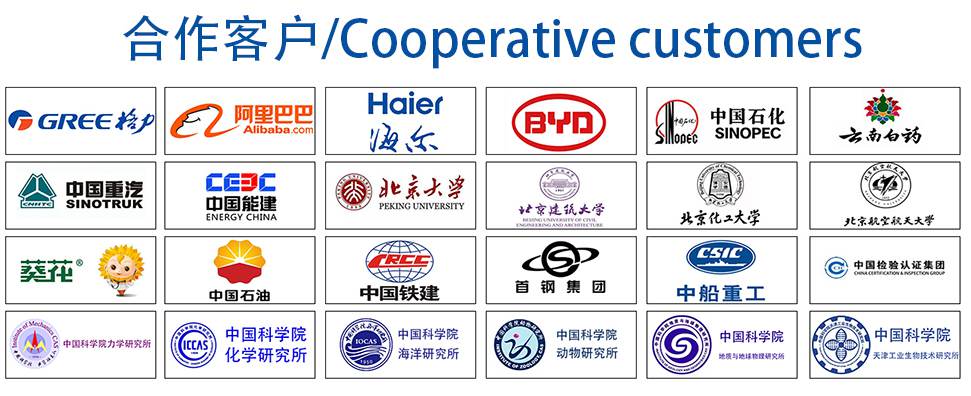
材料实验室
热门检测
259
218
193
204
200
205
213
203
209
219
206
201
205
205
199
197
211
201
210
203
推荐检测
联系电话
400-635-0567