导线和引出端可焊性检测:检测项目与方法详解
一、可焊性检测的核心目标
- 润湿能力:焊料是否能在规定时间内均匀覆盖表面;
- 结合强度:焊点是否满足机械强度要求;
- 表面状态:是否存在氧化、污染或镀层缺陷等影响焊接的因素。
二、可焊性检测的主要项目
1. 润湿性测试(Wettability Test)
- 原理:通过观察焊料与待测表面接触后的润湿速度和扩展范围,判断可焊性。
- 方法:
- 边缘浸渍法(Dip Test):将试样垂直浸入熔融焊料中一定时间(通常3-5秒),取出后观察润湿角度和覆盖率。
- 焊球法(Solder Ball Test):将焊料球置于待测表面,加热后观察焊球的铺展情况。
- 评价标准:
- 润湿角≤90°为合格(角度越小润湿性越好);
- 焊料覆盖率≥95%视为良好。
2. 焊料扩展率测试
- 操作:在标准条件下(如温度、助焊剂类型)将焊料置于待测表面,测量熔融焊料的扩展直径。
- 计算公式: 扩展率=焊料扩展直径−初始焊料直径初始焊料直径×100%扩展率=初始焊料直径焊料扩展直径−初始焊料直径×100%
- 标准要求:扩展率≥70%为合格。
3. 焊接强度测试
- 目的:评估焊点的机械强度,确保其能承受装配或使用中的应力。
- 方法:
- 拉力测试:使用拉力机对焊点施加垂直拉力,记录断裂前的最大载荷;
- 剪切测试:施加平行于焊接面的力,测量剪切强度。
- 参考标准:根据IPC-J-STD-001等规范,强度需满足元器件规格要求。
4. 表面氧化与污染检测
- 目视检查:使用显微镜或放大镜观察表面是否有氧化变色、异物残留或镀层剥落。
- 化学分析:
- EDX(能谱分析):检测表面污染物成分(如硫、氯离子);
- X射线荧光光谱(XRF):分析镀层厚度及均匀性。
5. 加速老化测试
- 模拟恶劣环境:将试样置于高温高湿环境(如85℃/85%RH)中48小时,再进行可焊性测试,评估储存后的性能衰减。
- 结果判定:老化后润湿性下降幅度需<20%。
6. 助焊剂残留物检测
- 离子污染测试:通过溶剂萃取法测量残留物的离子浓度(如Na⁺、Cl⁻),确保残留物不影响长期可靠性。
- 标准参考:IPC-TM-650 2.3.28。
三、检测设备与标准
-
- 可焊性测试仪(如Menas可焊性测试系统);
- 焊料槽、恒温加热台;
- 拉力试验机、显微镜/电子显微镜。
-
- IPC J-STD-002:导线和引出端可焊性测试的国际通用标准;
- IEC 60068-2-20:环境试验中的可焊性评估方法;
- GB/T 2423.32(中国国标):电子元器件可焊性试验规范。
四、常见缺陷与原因分析
缺陷类型 | 可能原因 |
---|---|
润湿不良 | 表面氧化、镀层不纯、助焊剂失效 |
焊料覆盖率低 | 污染、储存条件不当 |
焊接强度不足 | 温度不足、焊接时间过短 |
焊点发黑或空洞 | 助焊剂残留、气体逸出不良 |
五、提升可焊性的关键措施
- 严格控制储存环境(湿度≤60%,温度15-30℃);
- 采用抗氧化镀层(如镀锡、镀银);
- 使用活性适中的免清洗助焊剂;
- 定期校准设备,确保检测条件的一致性。
六、总结
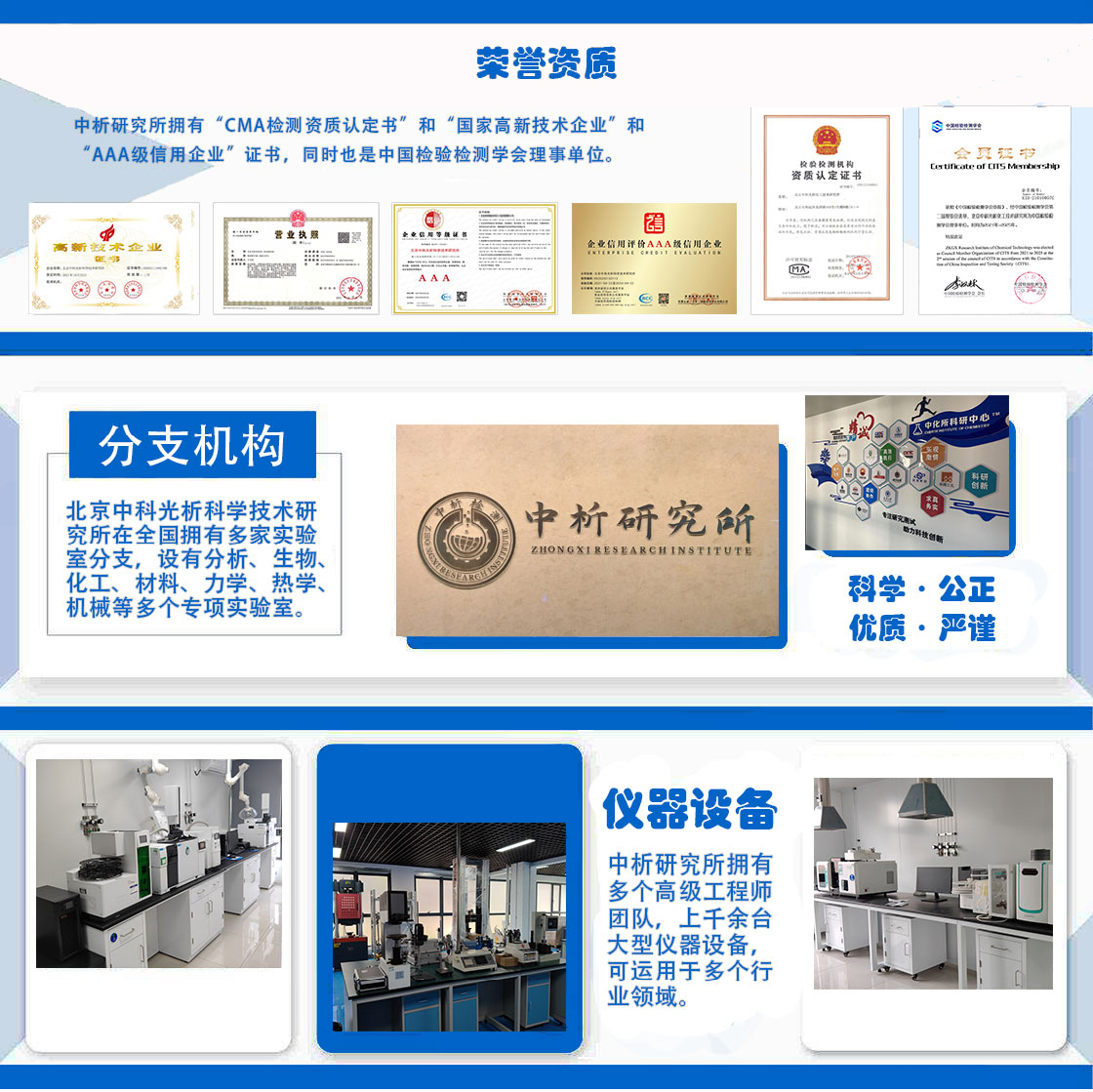
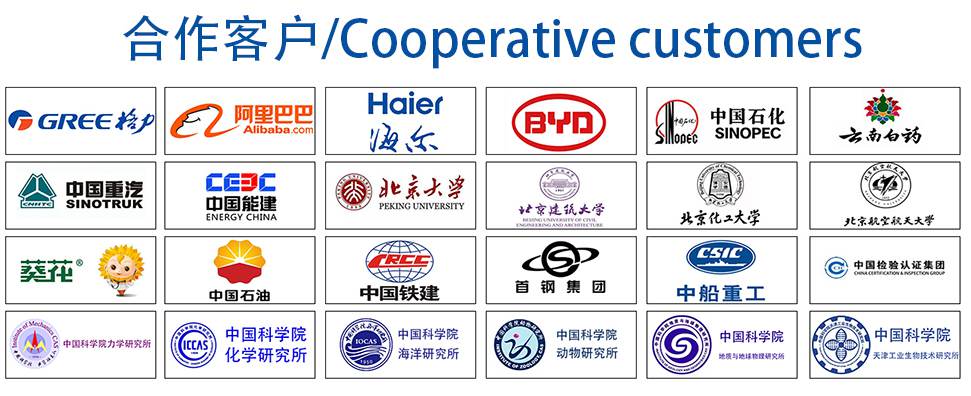
材料实验室
热门检测
264
221
199
207
201
206
216
208
216
221
208
207
211
208
201
199
213
204
211
206
推荐检测
联系电话
400-635-0567