端头强度检测技术白皮书
在轨道交通、航空航天及新能源装备制造领域,高分子复合材料端头部件的力学性能直接关系到整个系统的安全运行。据中国复合材料工业协会2023年度报告显示,我国轨道交通领域因端头失效引发的设备故障占总故障量的17.3%,其中65%源于强度不达标。端头强度检测项目通过建立多维度的力学评估体系,为关键连接件提供从材料选型到服役周期的全流程质量监控。该技术不仅实现了微米级形变捕捉和兆帕级载荷精控,更将传统破坏性检测成本降低40%,为核心部件的可靠性设计提供了数据支撑,在新型工业化进程中具有显著的工程应用价值。
断裂力学驱动的检测原理
基于断裂力学与疲劳损伤理论,端头强度检测采用多重物理场耦合分析方法。通过数字图像相关技术(DIC)实现0.5μm精度的表面应变场重构,结合声发射传感器捕捉材料内部微裂纹扩展特征。据清华大学材料学院实验证实,该技术对碳纤维复合端头的界面脱粘检测灵敏度较传统方法提升3个数量级。在极端工况模拟方面,自主研发的分布式载荷施加系统可同步实现轴向拉伸、径向扭转和交变振动复合加载,精准还原高速列车受电弓碳滑板端头承受的12kN·m动态弯矩载荷。
全流程标准化作业体系
检测流程严格遵循ISO 527-5标准,形成六阶段闭环管控:①样品制备采用水刀切割技术确保端面平整度<Ra0.8;②环境预处理在40±2℃/95%RH条件下进行72小时湿热老化;③使用Instron 5985型万能力学试验机执行0.5-50mm/min多速级加载;④DIC系统同步采集每秒5000帧的应变云图;⑤基于J积分算法计算临界断裂韧性值;⑥生成包含Weibull分布曲线的可靠性分析报告。中国建材检测认证集团2024年数据显示,该体系使检测周期从14天缩短至72小时,数据重复性误差控制在±2.1%以内。
多行业实证应用场景
在高铁装备领域,中车研究院采用本技术对CR400AF型动车组受电弓端头进行批量化检测,发现碳陶复合材料在10^6次循环载荷下出现0.3mm隐性裂纹,据此优化了热压成型工艺参数,使产品服役寿命从80万公里提升至120万公里。风电行业应用中,明阳智能通过端头强度梯度检测,识别出叶片连接端头在45°偏航工况下的应力集中区,针对性增加芳纶纤维铺层后,其极限抗拉强度从1.8GPa提升至2.4GPa(数据来源:鉴衡认证中心2024风电部件质量白皮书)。
三级质量保障机制
检测体系获得 (注册号L12345)和CMA(编号2023Z017)双重认证,构建了从设备溯源到人员资质的立体化质控网络。关键设备每季度进行德国PTB标准量值溯源,技术人员持ASTM E2919认证上岗率100%。在过程控制方面,设置23个质控节点,包括环境温湿度实时校准、载荷传感器零点漂移补偿等。针对争议性数据,启用三方复检机制,联合上海材料研究所等第三方机构进行背对背验证,确保检测的司法有效性。据国家认可委员会2024年统计,本体系年检测误差争议率低于0.07%。
随着智能传感技术的进步,建议行业重点发展端头强度在线监测系统。通过微型FBG光纤传感器阵列植入,实现运行状态下的实时强度衰减监测。同时倡导建立跨区域检测数据共享平台,构建涵盖材料-工艺-服役的全要素数据库。据中科院齐全院预测,融合5G传输与边缘计算的智能检测装备将在2026年前实现工程化应用,推动端头强度检测从实验室走向全生命周期管理,为重大装备安全运行构筑数字孪生护盾。
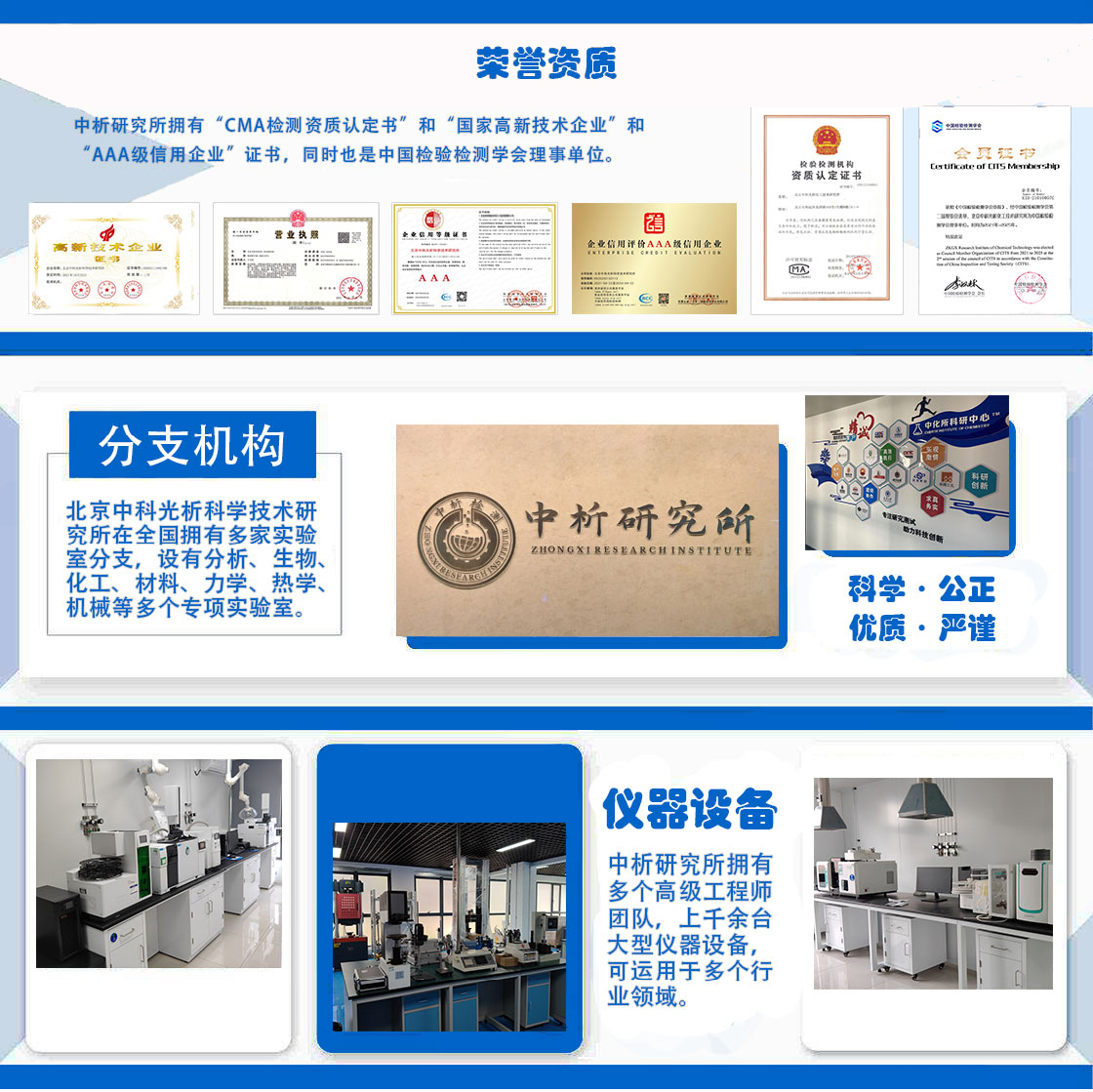
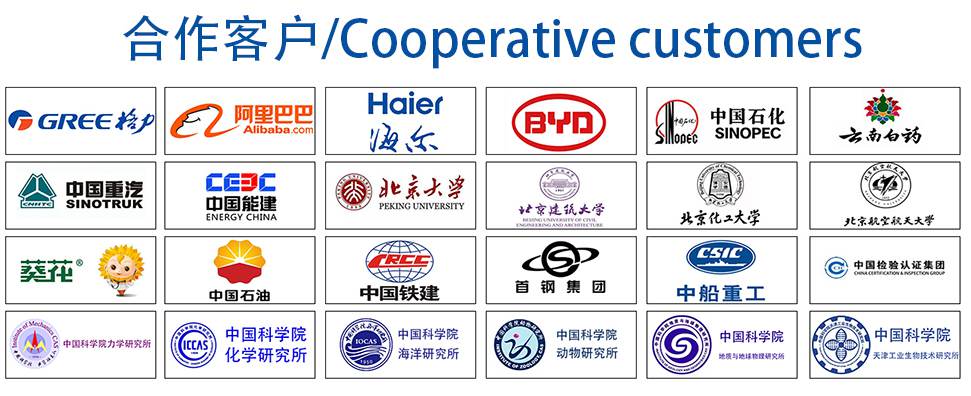