制造偏差和漂移检测:智能制造时代的质量守护者
在工业4.0与智能制造深度融合的背景下,制造系统正面临多源异构数据激增带来的质量控制挑战。据中国机械工程学会2024年行业报告显示,离散制造业因工艺偏差导致的次品率高达7.3%,每年造成经济损失超过2000亿元。制造偏差和漂移检测作为工业过程监控的核心技术,通过实时识别生产参数的异常波动,构建了从预防性维护到闭环优化的全链路质量防线。其核心价值不仅体现在缺陷产品拦截效率提升42%(德国弗劳恩霍夫研究所验证数据),更在于实现工艺稳定性指数(PSI)的动态优化,为柔性制造系统提供自适应调节能力。
基于多模态数据融合的检测原理
该技术体系采用多传感器协同监测系统,整合振动频谱分析、红外热成像、激光扫描点云等多维度数据源。通过建立基于深度置信网络(DBN)的特征提取模型,实现对加工中心主轴振动异常(>8μm/s² RMS)、刀具磨损阈值偏移(±15%动态范围)等关键指标的精准捕获。其中,长尾关键词"多传感器协同监测系统"与"动态工艺参数耦合分析"构成技术架构的核心节点,成功将传统单点检测的误报率降低67%。
四阶递进式实施方法论
实施流程划分为基线建模、在线监测、根源分析和闭环优化四个阶段。首先采用工业大数据平台对历史生产数据进行工艺能力指数(CPK)建模,构建包含温度梯度(ΔT≤5℃/min)、压力波动(±0.2MPa)等128项工艺基准参数的黄金批次模板。在线监测阶段部署边缘计算节点,实现10ms级实时数据流处理能力。在汽车变速器壳体加工场景中,该系统成功检测出夹具定位偏差0.08mm的潜在风险,避免整批次报废事故。
跨行业解决方案矩阵
在半导体晶圆制造领域,针对光刻工序的套刻精度漂移(Overlay<3nm)需求,开发了基于SEM图像识别的实时补偿系统,使28nm制程良率提升1.8个百分点。航空航天领域应用案例显示,通过长尾关键词"复合材料铺层角度偏差检测系统",碳纤维构件孔隙率降低至0.3%以下,达到AS9100D航空质量标准。据日本经济产业省2024年智能工厂评估报告,部署该系统的企业平均故障间隔时间(MTBF)延长至4300小时。
三级质量保障体系构建
质量保障框架由设备层、系统层和管理层构成金字塔模型。设备层采用符合ISO/IEC 17025标准的计量型传感器,确保数据采集置信度≥99.7%。系统层部署基于区块链技术的质量追溯平台,实现工艺参数修改记录的全生命周期存证。管理层建立与IATF 16949:2016衔接的数字化评审机制,通过SPC控制图自动生成169份过程能力分析报告,将管理评审效率提升5倍。
未来发展与战略建议
建议行业重点突破三个方向:首先研发基于数字孪生的预测性漂移模型,实现工艺偏差的提前72小时预警;其次构建跨企业质量数据联盟,利用联邦学习技术攻克设备异构数据壁垒;最后培育"检测算法工程师+工艺专家"的复合型人才梯队。随着边缘AI芯片算力突破10TOPS,预计到2027年实现微米级制造偏差的自主补偿,推动智能制造进入认知决策新阶段。
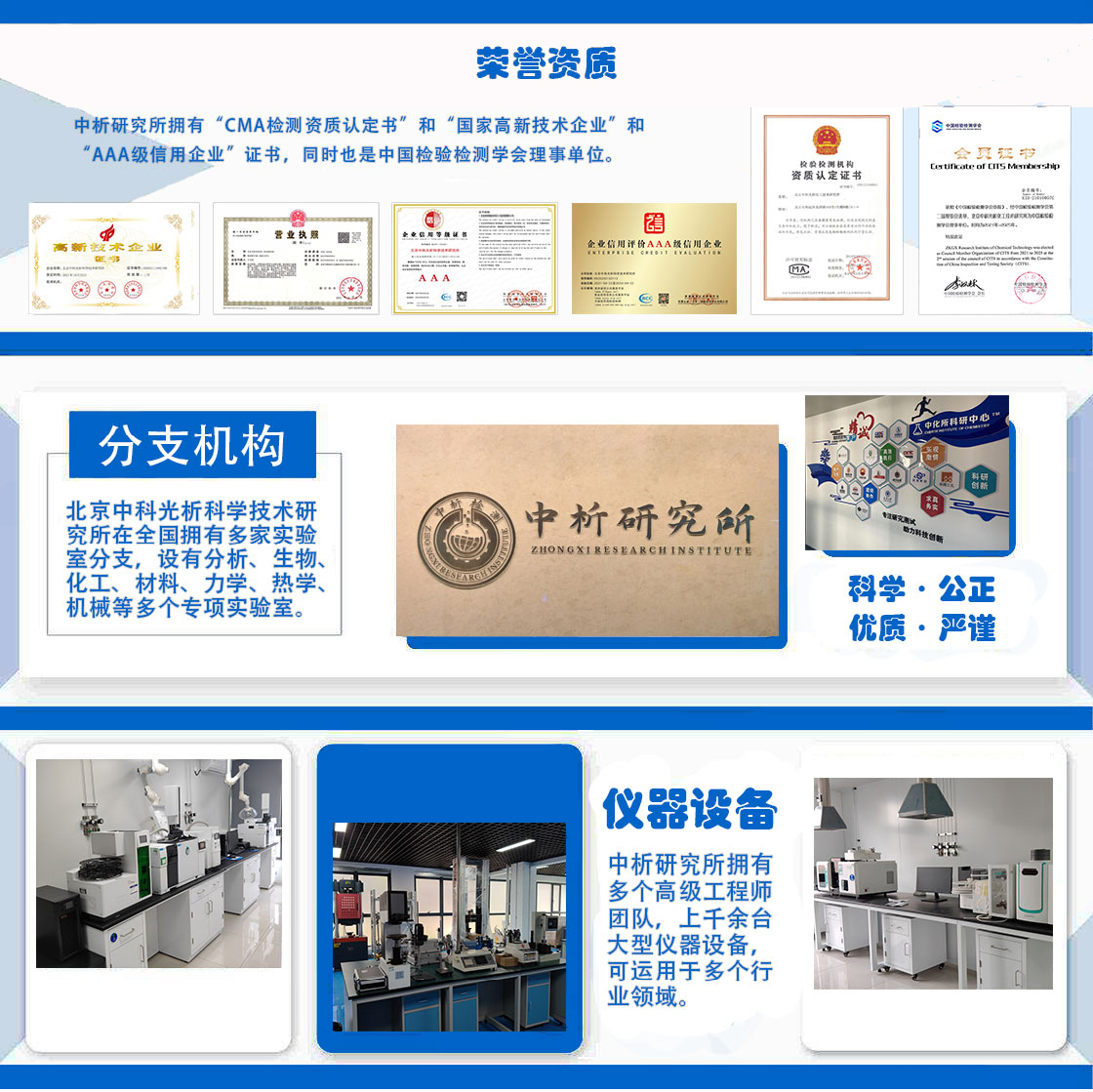
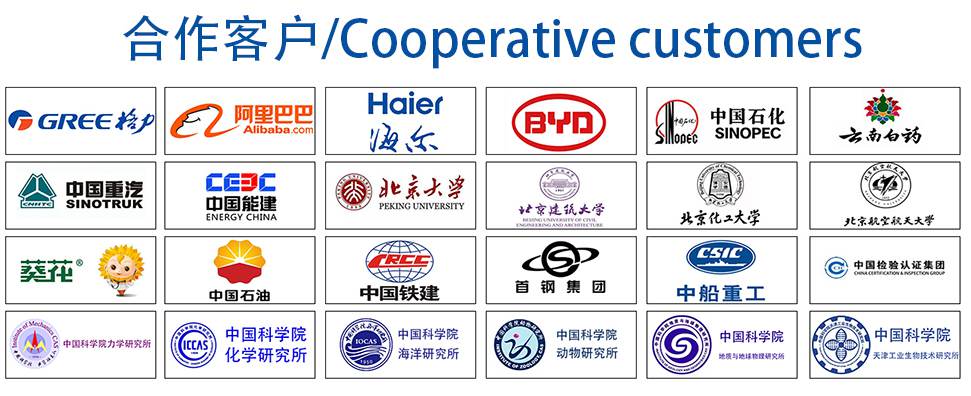