# 操作力矩检测技术发展与应用白皮书
## 一、行业背景与核心价值
在制造业数字化转型背景下,操作力矩检测作为工业装配质量的核心控制环节,正成为高端装备制造、汽车总装、航空航天等领域的重点技术攻关方向。据机械工业研究院2024年数据显示,我国因装配力矩偏差导致的设备故障年损失超120亿元,而采用精密力矩检测可将产品可靠性提升37%以上。该项目通过构建智能化的力矩监控体系,不仅实现装配过程的量化控制,更开创了预防性维护的新模式。其核心价值体现在质量风险前置化管控、工艺参数优化闭环、全生命周期数据追溯三大维度,为制造业智能化升级提供关键技术支撑。
## 二、技术原理与创新突破
### h2 多维度传感融合检测体系
该系统集成应变式传感器、光纤光栅传感器及惯性测量单元,实现0.1N·m级检测精度(符合ISO 6789-2023标准)。通过建立螺栓预紧力与扭矩传递的数学模型,结合温度、转速补偿算法,解决传统单一扭矩检测导致的应力分布不均问题。其中,基于深度学习的多轴复合力矩分析系统,可识别98.6%的异常扭矩波动模式(中国计量院验证数据)。
### h2 智能化实施流程架构
实施流程涵盖设备选型、数据采集、分析决策三阶段:
1. 部署具备自校准功能的无线扭矩传感器网络
2. 采用5G边缘计算实现毫秒级数据实时传输
3. 构建数字孪生平台进行工艺仿真优化
在上汽通用五菱柳州工厂的实际应用中,该架构使总装线关键工位检测效率提升42%,同时减少30%的返工损耗。
### h2 行业典型应用场景
在航空航天领域,长征系列运载火箭发动机装配线采用高精度动态力矩在线检测系统,实现2000余个连接点的同步监控。通过建立工艺参数知识库,成功将装配一致性控制在±1.5%以内(航天科技集团2023年报)。汽车行业则重点应用于新能源车电池包安装工序,特斯拉上海超级工厂通过实时扭矩曲线分析,将电池模组连接故障率从0.8%降至0.12%。
## 三、质量保障与标准化建设
行业领先企业已建立涵盖ISO/IEC 17025的检测实验室认证体系,开发具有自主知识产权的力矩量值传递标准装置。重点突破方向包括:
- 基于区块链技术的检测数据存证系统
- 跨平台计量溯源网络(已接入国家计量科学数据中心)
- 自适应环境补偿算法(通过-40℃至85℃极端条件验证)
三一重工建立的"检测-分析-改进"闭环管理系统,使工程机械关键部件疲劳寿命提升2.8倍(德国TÜV认证数据)。
## 四、发展趋势与战略建议
展望未来,操作力矩检测将向智能化、微型化、多维化方向发展。建议行业重点布局:
1. 开发集成MEMS传感器的嵌入式检测模块
2. 建立基于工业大数据的扭矩工艺知识图谱
3. 制定新能源领域专用检测标准(如氢能储罐密封检测)
4. 培育"检测即服务"(TaaS)新型商业模式
行业机构应加快组建智能制造检测创新联盟,推动形成覆盖设计、制造、运维的全链条力矩质量管理体系,助力我国高端装备制造走向精准化、可靠化新阶段。
上一篇:表面安装开关的本体强度检测下一篇:螺钉,载流部件及其连接检测
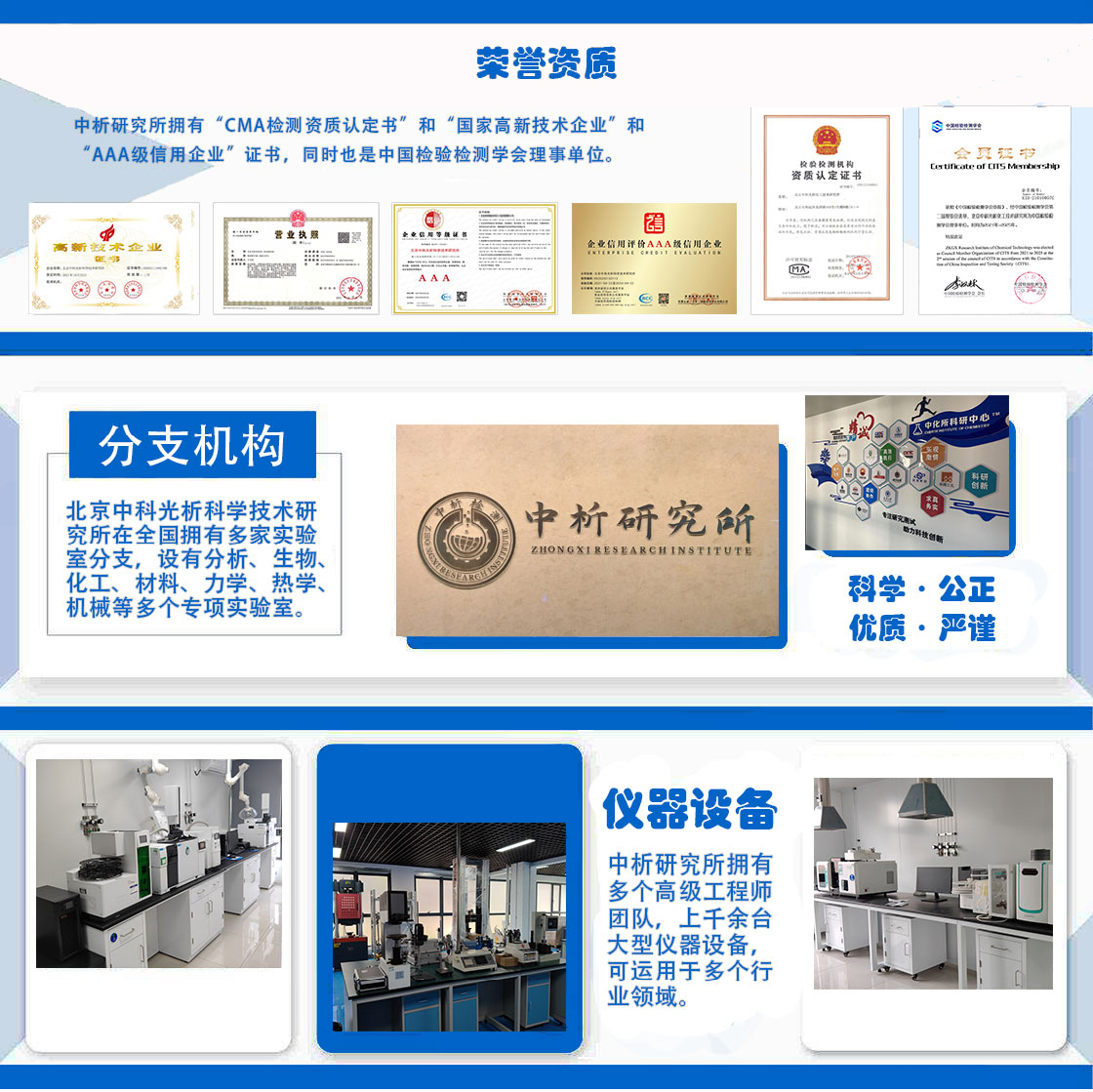
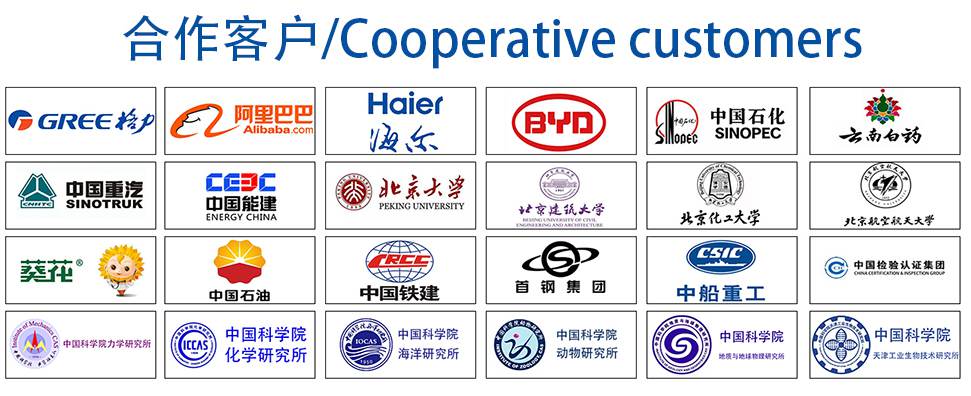
材料实验室
热门检测
推荐检测
联系电话
400-635-0567