高温容量检测
发布时间:2025-07-12 20:04:37- 点击数: - 关键词:
实验室拥有众多大型仪器及各类分析检测设备,研究所长期与各大企业、高校和科研院所保持合作伙伴关系,始终以科学研究为首任,以客户为中心,不断提高自身综合检测能力和水平,致力于成为全国科学材料研发领域服务平台。
立即咨询高温容量检测:核心检测项目与关键技术解析
一、高温容量检测的核心项目
-
- 检测目的:评估材料在高温下的结构稳定性,防止分解、相变或氧化。
- 方法:热重分析(TGA)、差示扫描量热法(DSC)。
- 关键参数:失重速率、热分解温度(如TGA测定)、相变焓值(DSC)。
- 标准依据:ASTM E1131、ISO 11358。
-
- 检测意义:反映材料储热能力,影响散热系统设计。
- 技术手段:激光闪射法(LFA)、绝热量热法。
- 适用场景:储能材料(如相变材料)、发动机隔热层。
-
- 检测目标:测量热量在材料中的传递效率。
- 主流方法:稳态热板法(ASTM C177)、瞬态热线法(ISO 22007)。
- 高温难点:需控制环境温度梯度,避免热辐射干扰。
-
- 工程价值:预测材料受热形变量,避免结构失配。
- 设备要求:高温膨胀仪(最高可达1600℃)。
- 典型案例:涡轮叶片涂层与基体的CTE匹配性检测。
-
- 检测重点:评估材料在高温+长期应力下的塑性变形。
- 试验标准:ISO 204(金属材料)、ASTM D2990(塑料)。
- 数据输出:蠕变曲线(应变-时间关系)、断裂寿命预测。
-
- 特殊工况:高温氧化、硫化、熔盐腐蚀环境。
- 加速试验:采用管式炉模拟腐蚀气氛(如SO₂、Cl₂)。
- 量化指标:腐蚀速率(g/(m²·h))、氧化膜厚度(SEM观测)。
-
- 高压高温场景:如燃料电池堆、航空液压系统。
- 检测技术:氦质谱检漏(灵敏度达10⁻⁹ Pa·m³/s)、压力衰减法。
- 失效阈值:根据工况设定允许泄漏率(如核电阀门<1×10⁻⁶ mbar·L/s)。
二、检测流程与技术手段
-
- 预处理阶段:样品切割→表面抛光→真空除气(减少氧化干扰)。
- 升温策略:梯度升温(5℃/min~20℃/min)或恒温保持。
- 数据采集:热电偶(K型/N型)+红外测温双重校准,确保±1℃精度。
-
- 同步热分析(STA):同步获取TGA与DSC数据,分析材料分解与吸放热关联性。
- 高温原位表征:结合XRD、SEM观察材料微观结构动态变化。
- 多场耦合测试:实现温度-应力-腐蚀多因素协同加载(如热机械分析仪TMA)。
三、行业应用案例
-
- 检测组合:CTE(基体/涂层匹配)+ 蠕变测试(10³小时寿命模拟)+ 热障涂层氧化试验。
- 失效规避:通过检测优化涂层孔隙率,降低剥落风险。
-
- 关键项目:180℃热收缩率(SEMI标准≤5%)、闭孔温度(DSC测定)。
- 安全提升:筛选耐高温陶瓷涂层隔膜,防止热失控。
-
- 长周期监控:定期进行高温拉伸(350℃~500℃)+ 中子辐照脆化评估。
- 寿命预测:基于断裂韧性(J积分法)推算剩余服役年限。
四、总结
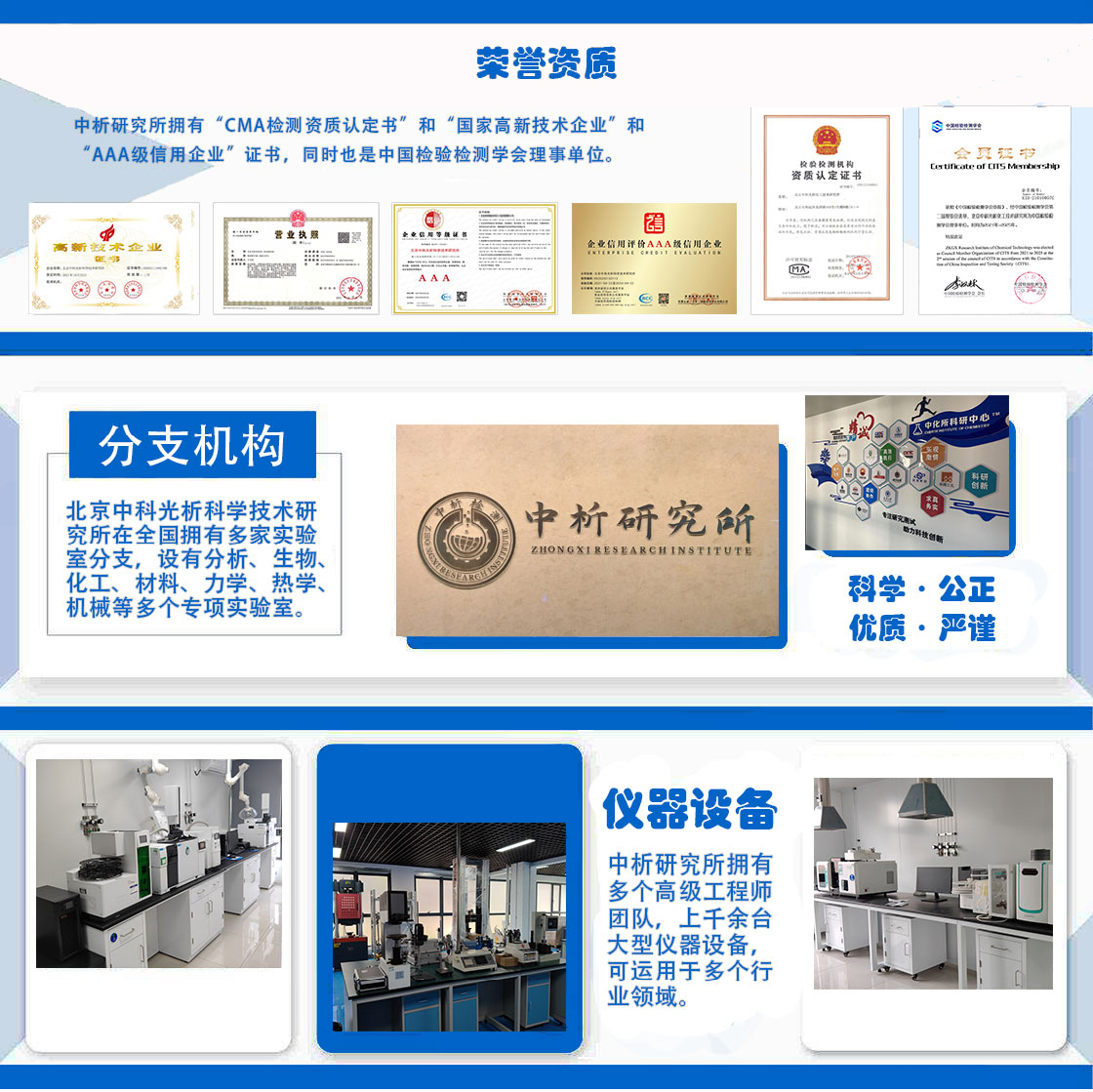
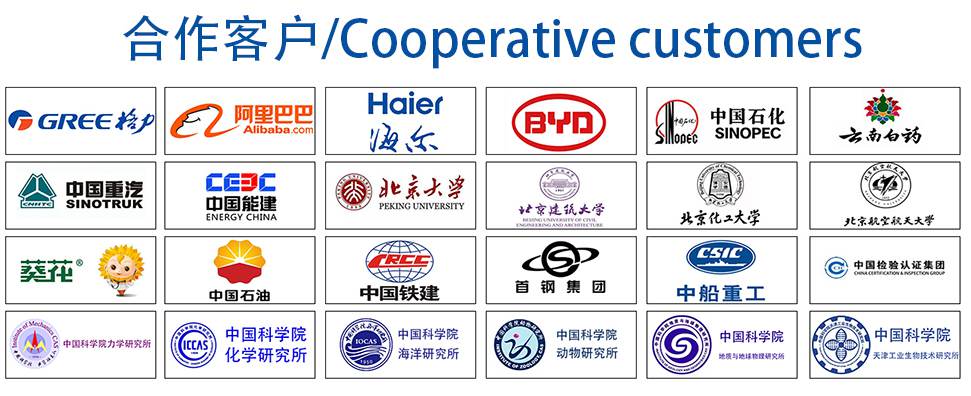
材料实验室
热门检测
297
250
225
236
231
232
246
239
245
253
234
237
237
238
230
228
242
227
241
236
推荐检测
联系电话
400-635-0567