一、高温性能试验检测的核心项目
1. 高温稳定性测试
- 目的:评估材料在高温长期暴露下的结构稳定性。
- 检测方法:
- 高温拉伸试验:测量材料在高温下的抗拉强度、屈服强度和延伸率(标准:ASTM E21/ISO 6892-2)。
- 高温压缩与弯曲试验:测试材料抗压、抗弯能力。
- 典型应用:航空发动机叶片、燃气轮机部件等高温承力件。
2. 高温抗氧化与耐腐蚀性测试
- 目的:分析材料在高温氧化或腐蚀环境中的抗退化能力。
- 检测方法:
- 静态氧化试验:将样品置于高温氧化环境中(如空气、CO₂、H₂S),通过质量变化计算氧化速率(标准:ASTM G54)。
- 热腐蚀试验:模拟熔盐或燃气环境,评估材料抗硫化、氧化腐蚀性能(标准:ASTM G111)。
- 典型应用:火力发电锅炉管、化工反应器内衬材料。
3. 高温蠕变与持久强度测试
- 目的:测定材料在高温恒定应力下的缓慢塑性变形(蠕变)和断裂时间。
- 检测方法:
- 单轴蠕变试验:施加恒定载荷,记录应变-时间曲线,计算蠕变速率及断裂寿命(标准:ASTM E139/GB/T 2039)。
- 持久强度试验:测定材料在高温下承受应力直至断裂的极限值。
- 典型应用:核电站高温管道、航空发动机涡轮盘。
4. 热疲劳性能测试
- 目的:评估材料在反复热循环(急冷急热)下的抗裂纹扩展能力。
- 检测方法:
- 热震试验:将样品快速加热后骤冷,观察表面裂纹数量及长度(标准:ASTM C1525)。
- 高低周热机械疲劳试验:结合温度循环与机械载荷,模拟实际工况。
- 典型应用:刹车盘、火箭喷嘴等承受热冲击的部件。
5. 高温热物理性能测试
- 关键参数:
- 热膨胀系数(CTE):测量材料受热后的尺寸变化(标准:ASTM E228)。
- 热导率:评估材料导热能力(标准:ASTM E1461)。
- 比热容:测定材料储热特性(标准:ISO 11357)。
- 典型应用:电子封装材料、热障涂层设计。
6. 高温环境下的动态力学性能
- 检测内容:
- 高温硬度测试:维氏/布氏硬度随温度的变化(标准:ASTM E384)。
- 动态力学分析(DMA):测量材料储能模量、损耗因子随温度的变化。
- 意义:优化高温阻尼材料、高分子密封件的性能设计。
二、检测流程与设备要求
- 样品制备:根据标准加工试样,确保尺寸精度与表面光洁度。
- 设备选择:
- 高温试验机:配备电阻炉或感应加热系统,温度范围通常为300°C~1600°C。
- 环境模拟装置:如真空/气氛控制箱、腐蚀介质注入系统。
- 数据采集:高温引伸计、红外测温仪、应变传感器实时监测。
- 结果分析:通过蠕变曲线、疲劳寿命图、氧化动力学模型等量化性能指标。
三、行业应用案例
- 航空航天:镍基高温合金的1100°C蠕变性能测试,确保发动机涡轮叶片寿命。
- 新能源电池:锂电正极材料在高温(60°C)下的循环稳定性评估。
- 汽车工业:刹车片材料在800°C热衰退测试中的摩擦系数衰减分析。
四、挑战与发展趋势
- 智能化测试:结合AI算法预测材料高温性能,减少试验周期。
- 多场耦合测试:同步施加温度、应力、腐蚀介质等多因素影响。
- 微观表征结合:SEM、XRD分析高温暴露后的微观结构演变。
五、
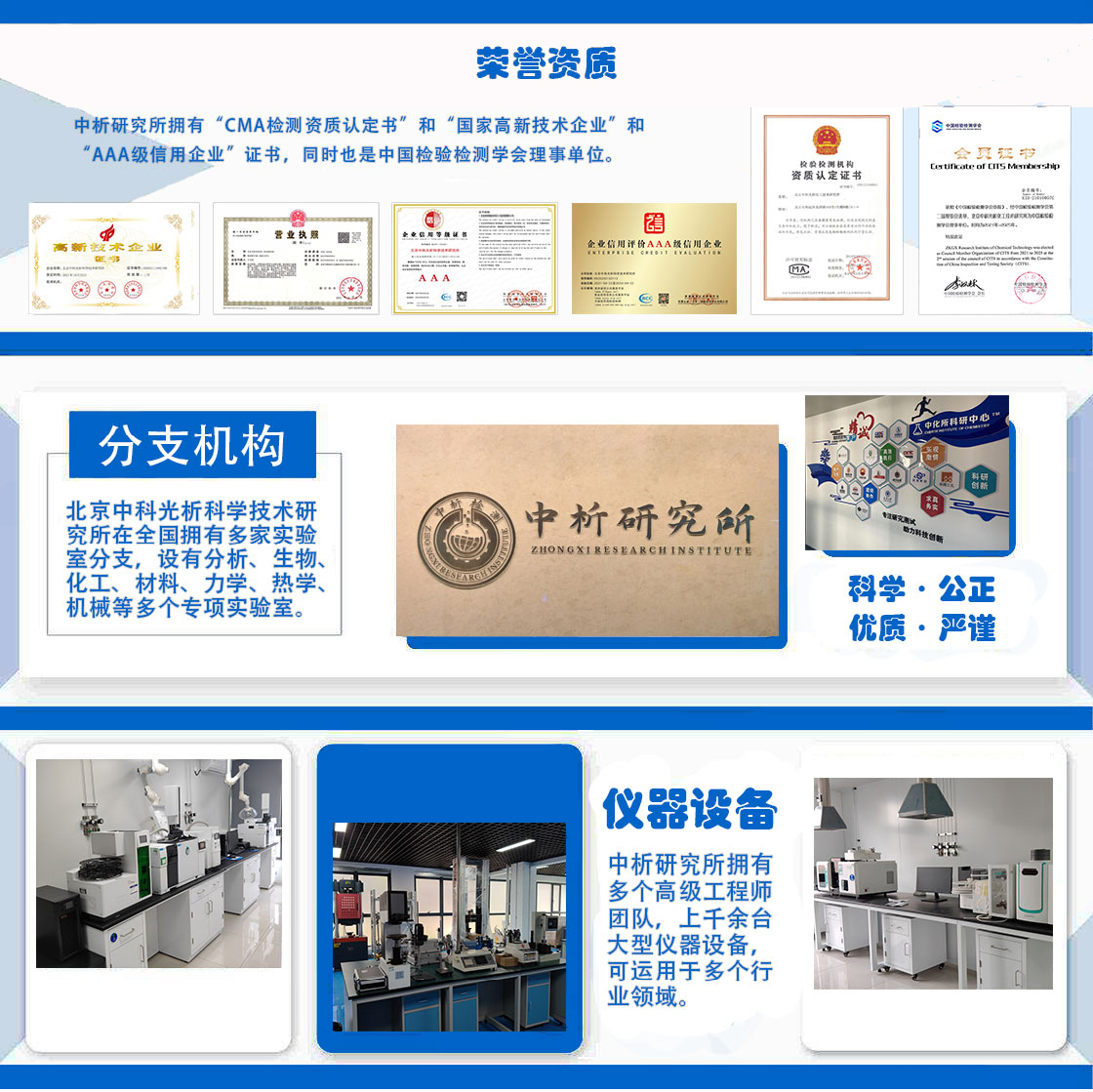
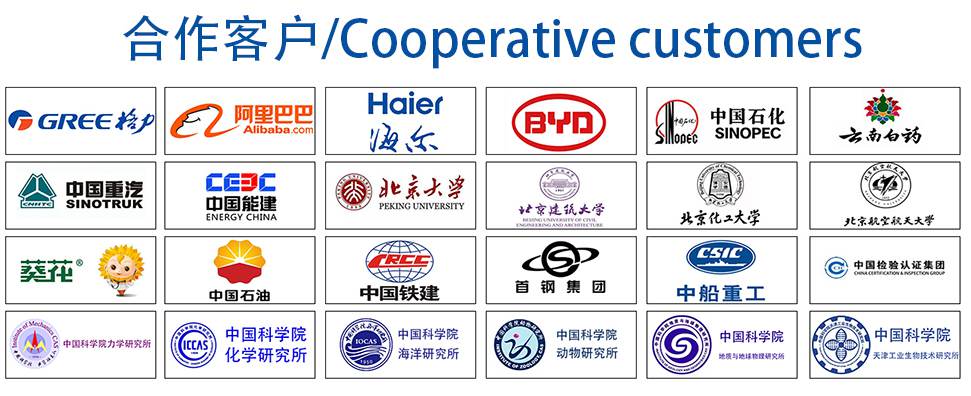
材料实验室
热门检测
276
233
208
216
215
220
228
223
231
231
220
219
222
219
213
209
226
212
224
218
推荐检测
联系电话
400-635-0567