一、热冲击(液体-液体)检测概述
- 评估材料耐温变性能:检测材料在热膨胀系数差异下的抗开裂能力。
- 验证产品可靠性:确保部件在极端温度循环下的功能完整性。
- 优化设计和工艺:通过失效分析改进材料选择或制造工艺。
二、核心检测项目
1. 物理性能检测
2. 力学性能检测
3. 功能性测试
4. 化学稳定性分析
- 介质兼容性: 检测测试液体(如硅油、乙二醇)与样品的化学相容性,避免溶胀、腐蚀等副反应。
- 氧化与腐蚀评估: 通过X射线光电子能谱(XPS)或能谱仪(EDS)分析表面元素变化,确认高温液体环境是否引发氧化层生长。
5. 循环寿命测试
- 失效循环数(Nf)统计: 记录样品在经历多少次热冲击循环后发生功能失效(如断裂、电气参数超标),绘制韦布尔分布曲线评估可靠性。
- 加速寿命模型: 基于Arrhenius方程建立温度-寿命关系,预测实际使用条件下的耐久性。
三、检测条件与标准
- 温度范围:
- 高温槽:通常设定为125°C~300°C(依材料类型调整)。
- 低温槽:-65°C~0°C,需避免介质凝固(如采用液氮冷却的乙醇)。
- 驻留时间:单次循环中高/低温液体浸渍时间(通常5~15分钟),确保样品温度均衡。
- 转换时间:样品转移时间需≤10秒,避免温度回稳影响骤变效果。
- 循环次数:依应用场景而定,电子元件通常需500~1000次循环。 参考标准:
- MIL-STD-883(军工电子)
- JESD22-A104(半导体器件)
- GB/T 2423.22(中国国标)
四、典型应用案例
-
- 检测ECU在-40°C(冷媒)至150°C(热油)循环下的焊点开裂风险。
- 关键指标:X射线检测焊点空洞率变化(需<5%)。
-
- 碳纤维增强树脂基复合材料在液氮(-196°C)与高温油(200°C)交替中的层间剪切强度(ILSS)衰减。
五、测试设备与流程
-
- 双槽式热冲击试验箱(独立高温槽与低温槽)。
- 自动转移机构(机械臂或吊篮),确保快速切换。
- 液体介质需具备高沸点/低冰点、低黏度、化学惰性。
-
- 预处理:样品在常温下稳定24小时。
- 初始检测:记录基线数据(形貌、电性能等)。
- 循环测试:按设定参数执行高低温交替。
- 中间检测:每50~100次循环抽检关键参数。
- 最终分析:失效模式分析(FMEA)与报告生成。
六、
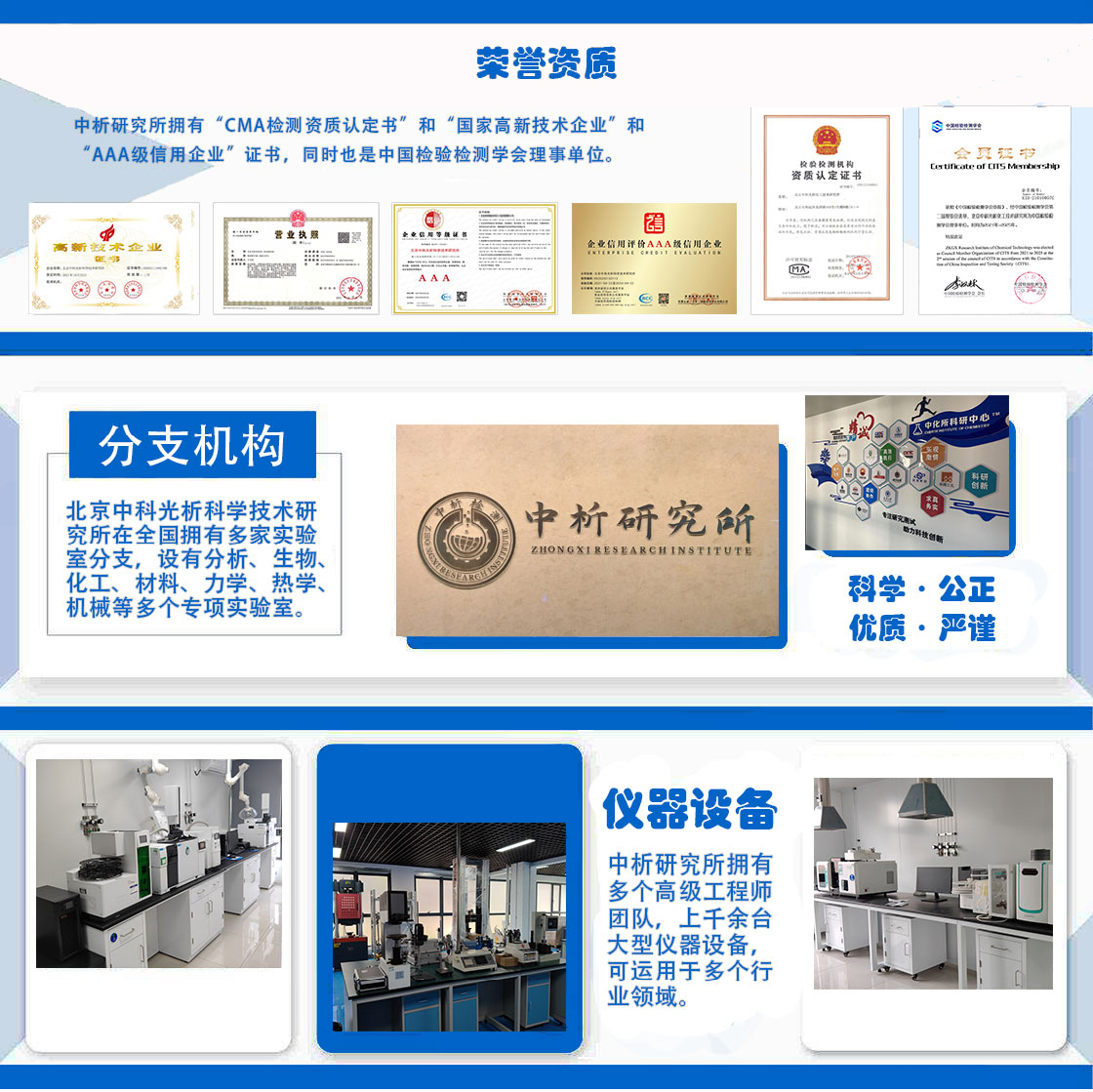
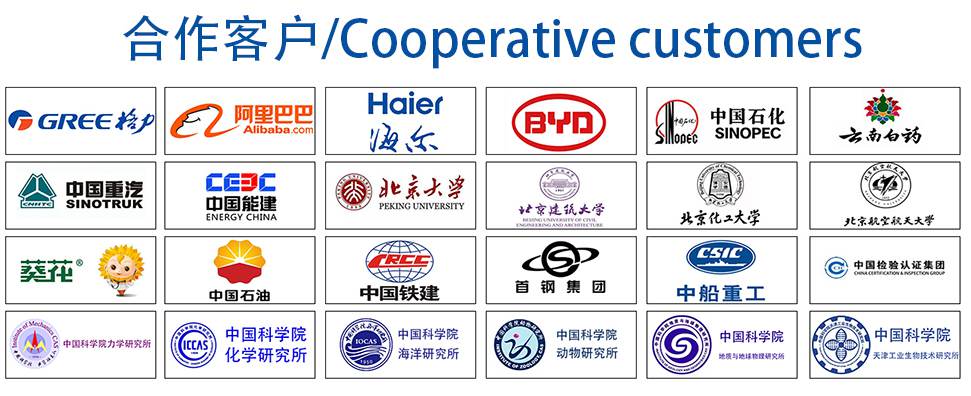
材料实验室
热门检测
271
227
202
211
210
213
225
218
228
229
213
213
218
216
210
205
221
207
220
214
推荐检测
联系电话
400-635-0567