一、疲劳寿命试验目的
- 验证设计合理性:评估球头销在循环载荷下的抗疲劳能力。
- 材料强度分析:检测材料是否满足长期交变应力下的强度要求。
- 寿命预测:模拟实际工况,预测球头销的失效周期。
- 质量控制:确保批量生产的产品符合企业或国家标准(如ISO 26262、GB/T 标准)。
二、核心检测项目
1. 静载荷测试
- 测试内容:施加额定静载荷至球头销总成,检测其变形量、间隙变化及结构完整性。
- 评判标准:载荷移除后,球头销应无塑性变形,密封性完好。
2. 动态疲劳测试
- 测试分类:
- 垂直方向载荷:模拟车辆颠簸路况下的垂直冲击。
- 横向载荷:模拟转向时的侧向受力。
- 复合载荷:垂向+横向联合加载,模拟复杂工况。
- 测试参数:
- 载荷范围:通常为额定载荷的50%~150%。
- 频率:10~15 Hz(接近实际行驶频率)。
- 循环次数:目标寿命≥50万次(乘用车)或≥100万次(商用车)。
3. 轴向和径向载荷测试
- 轴向测试:评估球头销在转向拉杆推力下的抗压疲劳性能。
- 径向测试:模拟车轮跳动对球头销的剪切应力影响。
4. 环境模拟测试
- 温度影响:在-40℃~120℃环境下测试疲劳寿命,验证材料的热稳定性。
- 腐蚀疲劳测试:盐雾试验后加载循环载荷,评估腐蚀环境对寿命的影响。
5. 失效模式分析
- 检测内容:
- 球头销断裂、裂纹扩展路径。
- 球座磨损、润滑脂泄漏情况。
- 防尘罩老化或破损导致的污染失效。
- 分析方法:金相显微镜、扫描电镜(SEM)观察断口形貌。
三、测试设备与方法
-
- 伺服液压疲劳试验机(如MTS、Instron)。
- 环境模拟箱(温湿度、盐雾)。
- 数据采集系统(记录载荷、位移、温度参数)。
-
- 国际:ISO 26262(道路车辆功能安全)。
- 国内:QC/T 29096-2021《汽车转向节用球头销总成技术条件》。
- 企业标准:部分车企要求高于行业标准。
四、检测结果分析
- 疲劳寿命曲线:绘制S-N曲线(应力-寿命曲线),确定疲劳极限。
- 失效判定:
- 临界点:裂纹长度≥1 mm或间隙变化超过设计值(如0.5 mm)。
- 数据统计:采用威布尔分布或三参数幂函数模型预测批量产品的可靠性。
五、注意事项
- 设备校准:确保传感器和作动器精度误差≤1%。
- 样品安装:模拟实车装配状态,避免附加力矩干扰。
- 环境控制:温湿度波动需保持在±2℃、±5% RH以内。
- 安全防护:设置紧急停机程序,防止试验中部件飞溅。
六、
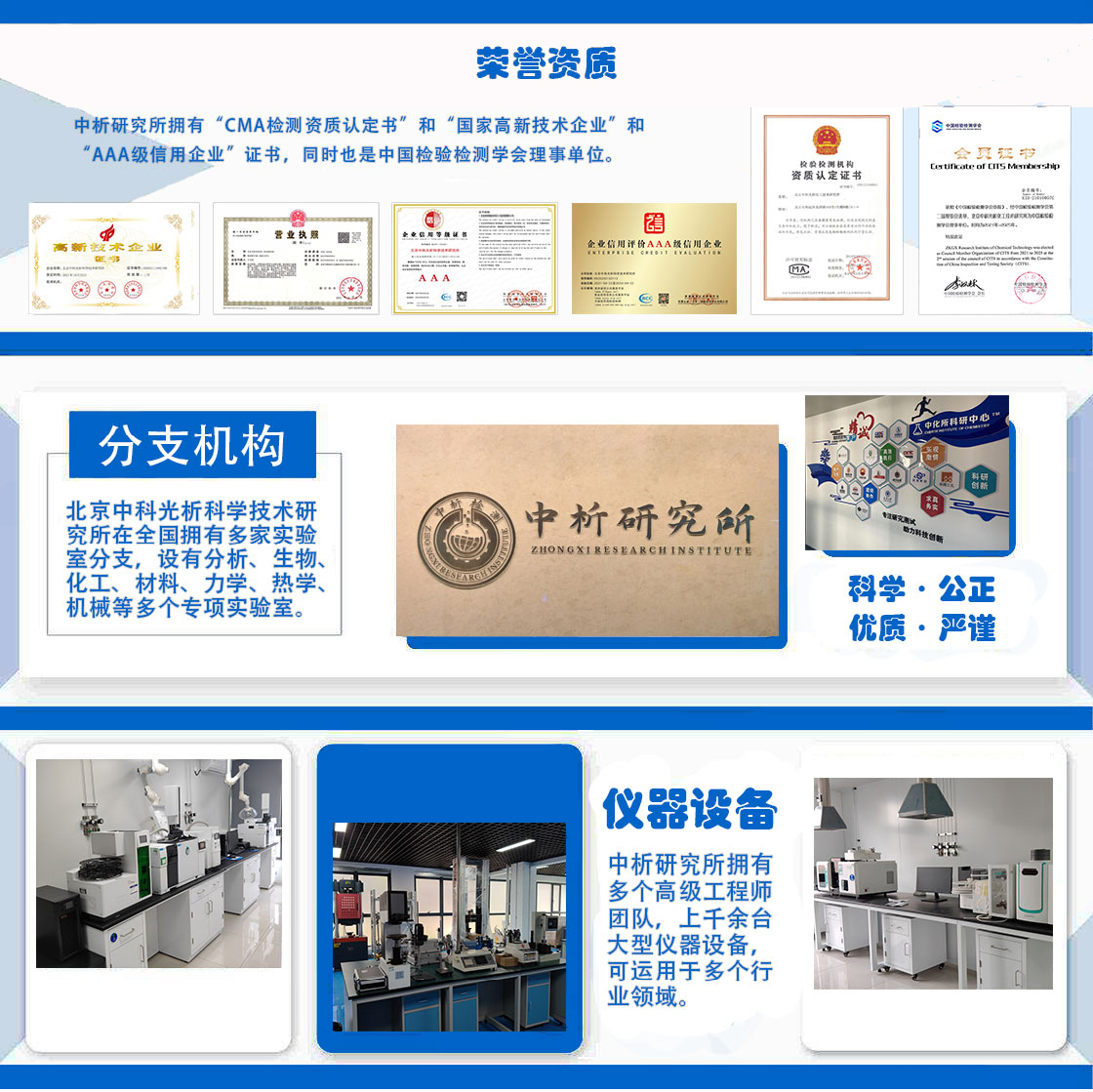
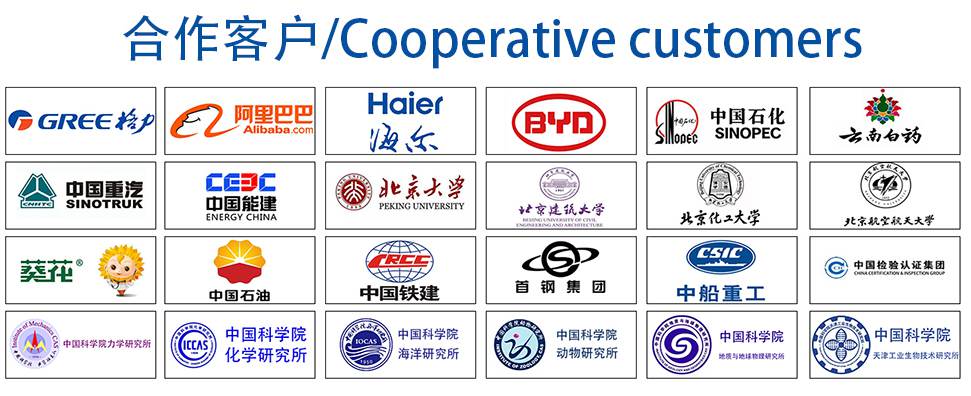
材料实验室
热门检测
276
233
208
217
215
220
230
223
233
233
220
219
222
219
213
210
227
212
224
218
推荐检测
联系电话
400-635-0567