技术原理与创新突破
耐久性试验采用多轴振动耦合加载技术,通过有限元分析建立材料疲劳损伤模型,结合ISO 16750-3标准进行加速寿命测试。热试验体系则包含温度循环(-40℃~150℃)、热冲击(ΔT≥100℃/min)及太阳辐射模拟(1120W/m²)三类核心测试模式。值得关注的是,最新研发的"电池模组热失控防护验证系统"创新性融合了红外热成像与气体成分在线监测技术,可实时捕捉热扩散过程中温度场演变及析气特征,测试精度达到±0.5℃。据国家新能源汽车技术创新中心验证,该技术使热失控预警准确率提升至98.6%。
标准化实施流程构建
项目实施遵循PDCA管理循环,建立包含需求分析、工况模拟、数据采集、失效分析的四阶段流程。在新能源汽车电机测试中,首先依据GB/T 29307标准构建负载谱,通过六自由度振动台模拟10万公里等效路谱载荷。热试验环节则采用JASO D001规范,执行1000次-30℃~85℃温度循环。某储能系统制造商应用该流程后,电池包连接件断裂故障率从3.2‰降至0.5‰,同时开发出满足IP67防护等级的"高低温交变密封检测工艺"。
行业应用与价值延伸
在轨道交通领域,复兴号动车组转向架通过200万次循环耐久测试,成功将检修周期从120万公里延长至240万公里。航空航天领域,C919机载电子设备采用三级阶梯式热试验方案,使元器件失效率降低70%。值得关注的是,在光伏行业新兴的"组件微裂纹智能检测系统"中,创新性融合了热斑试验(IEC 61215)与EL成像技术,使0.1mm级隐裂检出率提升至95%,据中国光伏行业协会统计,该技术每年可减少电站运维损失超12亿元。
质量保障体系创新
建立包含设备管理、人员资质、数据追溯的三维质量矩阵。采用NIST可追溯的校准体系,确保振动台控制精度≤±1dB。开发基于区块链的检测数据存证系统,实现试验过程100%可追溯。某检测机构通过 认可的热试验实验室,其温控均匀性达到±0.8℃(国家标准为±2℃),成为国内首家具备IEC 62660-3动力电池全项检测能力的第三方机构。
## 未来展望与建议 面向2030智能制造发展需求,建议从三方面深化技术应用:首先推动5G+AI技术在试验数据实时分析中的应用,建立"数字孪生测试平台";其次开发适应氢能装备、钠离子电池等新材料的专用测试标准;最后构建跨行业的"产品可靠性大数据中心",通过数据共享提升全产业链质量协同水平。据赛迪研究院预测,实施上述措施可使重点领域产品研发周期压缩30%,质量成本降低25%,为我国高端装备"走出去"战略提供坚实技术支撑。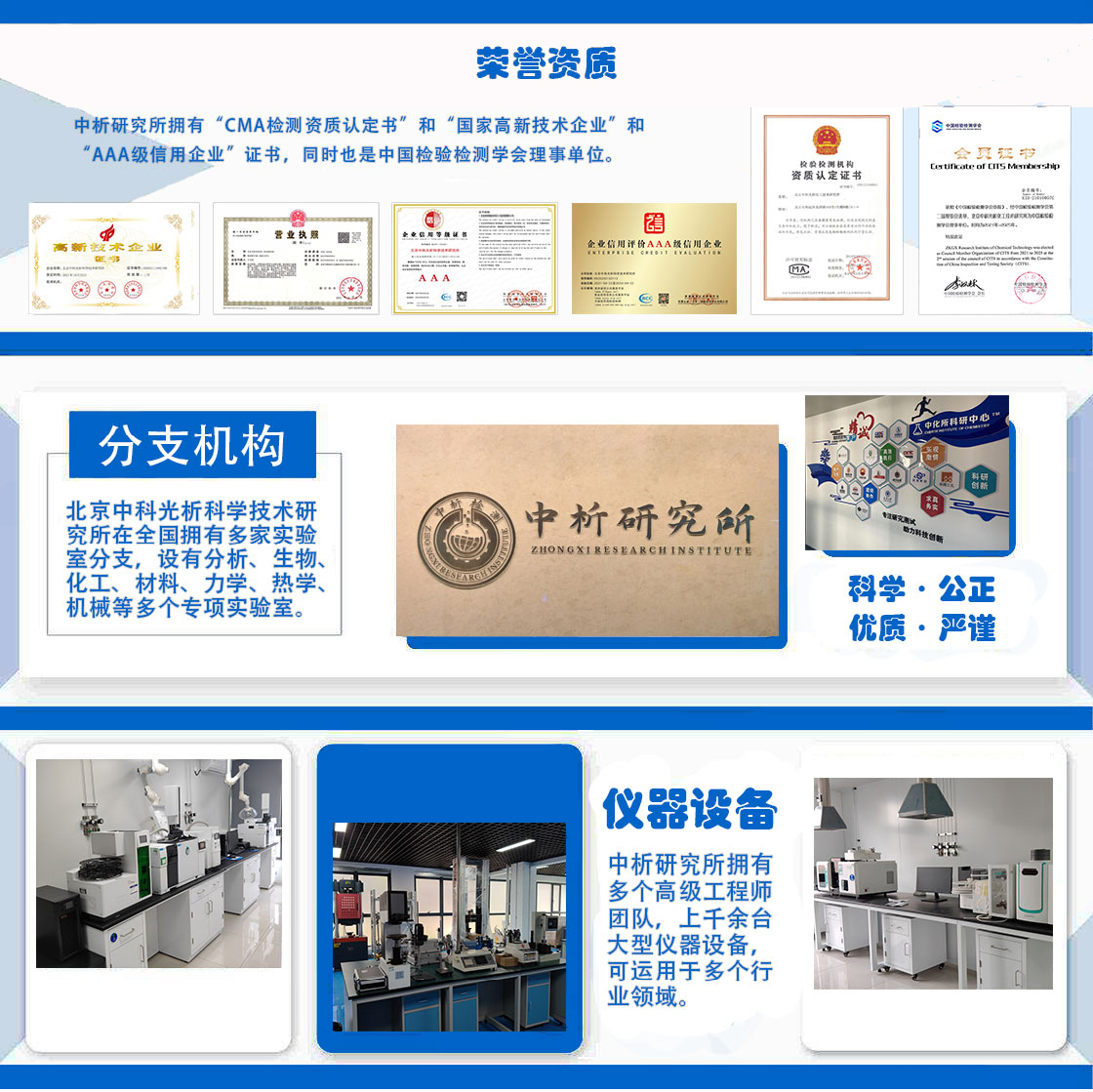
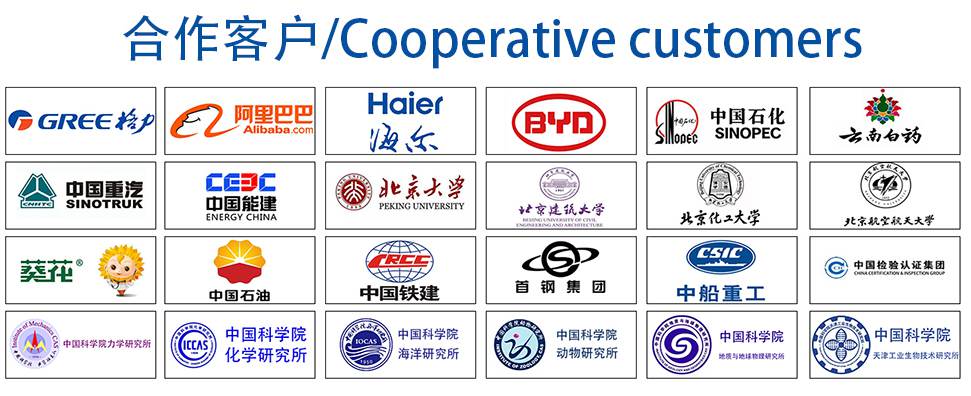