功率因数检测:核心检测项目与关键技术
一、功率因数检测的核心项目
-
- 定义:功率因数=有功功率(kW)/视在功率(kVA)
- 检测意义:数值越接近1,系统效率越高;若低于0.9,需采取补偿措施。
- 检测方法:使用功率分析仪或电能表直接读取实时功率因数值。
-
- 有功功率(P):实际用于做功的能量,直接影响设备运行效率。
- 无功功率(Q):维持电磁场交换但未做功的能量,可能导致线路损耗。
- 检测设备:通过功率分析仪同步测量P与Q,计算功率因数PF=cosφ=P/S(S为视在功率)。
-
- 原理:功率因数低通常源于电压与电流相位不同步(感性或容性负载导致)。
- 检测工具:示波器捕捉电压、电流波形相位差,或直接使用相位分析仪。
-
- 检测内容:总谐波畸变率(THD)、各次谐波分量(如3次、5次、7次谐波)。
- 影响:谐波会导致功率因数降低、设备过热,需专用谐波分析仪测量。
-
- 感性负载(如电动机、变压器):导致无功功率增加,需电容补偿。
- 容性负载(如电容柜、长电缆):可能引发过补偿,需动态调整。
- 检测方法:通过负载特性曲线分析或分段测量各支路功率因数。
-
- 检测参数:三相电压、电流的幅值偏差(偏差率>2%需调整)。
- 影响:不平衡会降低系统整体功率因数,增加中性线电流。
二、功率因数检测的关键技术
-
- 使用便携式功率分析仪或钳形表,实时采集电网数据,适用于工厂、楼宇等场景。
- 典型设备:Fluke 435系列电能质量分析仪、Hioki PW3390功率计。
-
- 安装固定式传感器与监测终端,与SCADA系统集成,实现24小时动态监控。
- 应用场景:变电站、数据中心、大型工业园区。
-
- 通过Matlab/Simulink或ETAP软件建模,模拟负载变化对功率因数的影响。
- 优势:预测补偿方案效果,避免现场试错成本。
三、检测结果的应用与优化
- 静态补偿
- 安装并联电容器组,抵消感性无功功率,适用于负载稳定的场景。
- 动态补偿(SVG/SVC)
- 使用静止无功发生器(SVG)或晶闸管控制电抗器(TCR),实时调节无功功率。
- 谐波治理
- 加装无源滤波器(LC电路)或有源滤波器(APF),降低谐波导致的功率损耗。
四、行业应用案例
- 工业领域:某化工厂通过检测发现功率因数仅0.75,加装电容补偿柜后提升至0.95,年节省电费超12万元。
- 新能源领域:光伏逆变器输出端功率因数需稳定在0.99以上,避免电网罚款。
- 建筑领域:商业综合体通过SVG动态补偿空调系统无功功率,降低变压器容量需求。
五、总结
- 国际标准:IEC 61000-4-30(电能质量测量方法)
- 国家标准:GB/T 14549-93(电能质量公用电网谐波)
- 行业规范:IEEE 1159-2019(电能质量监测指南)
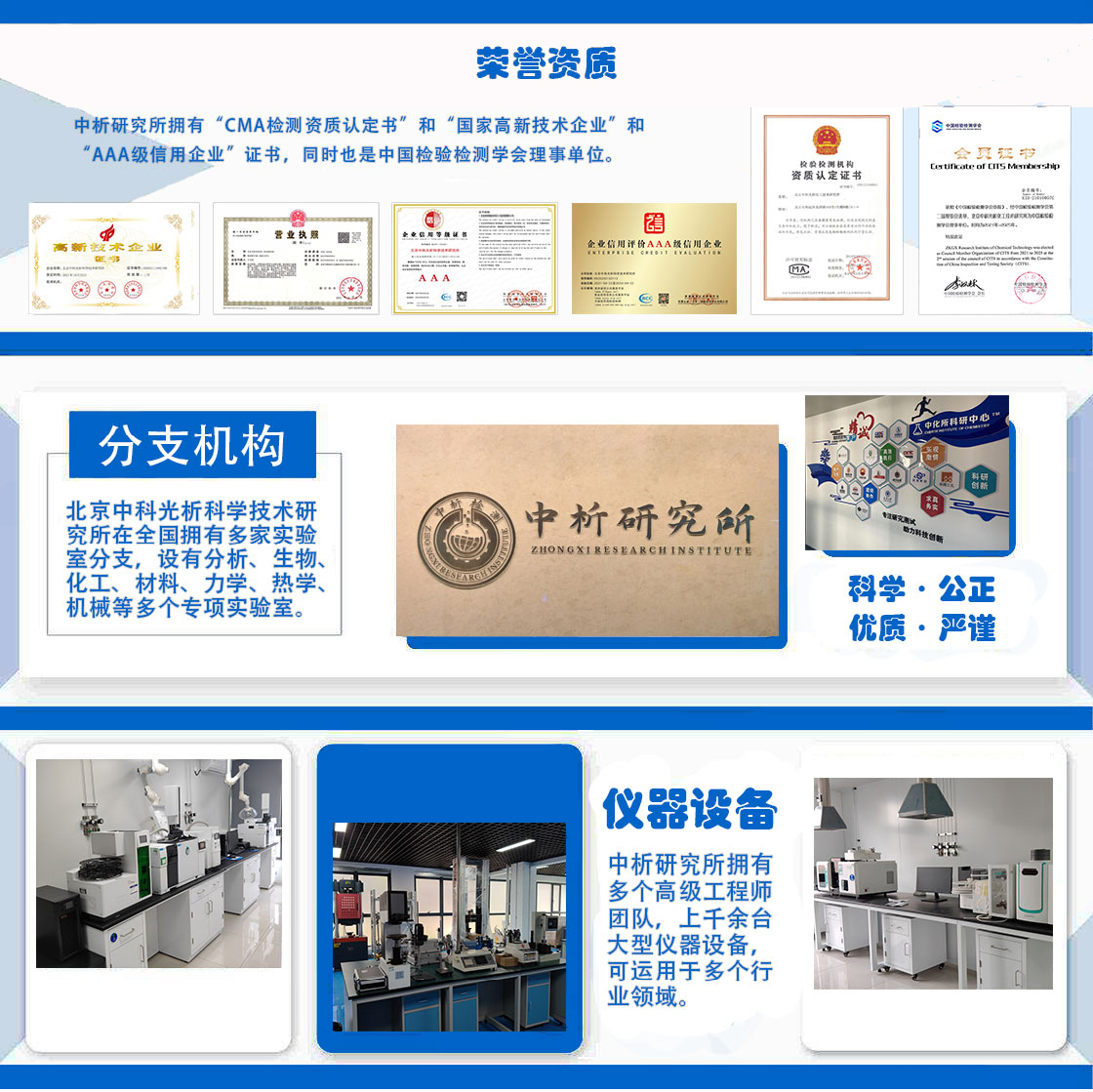
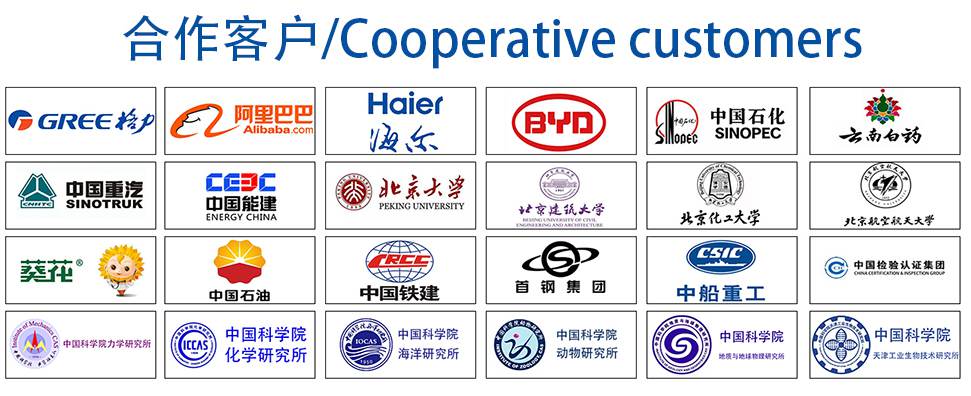
材料实验室
热门检测
22
25
24
24
25
21
20
16
14
17
20
22
19
20
18
15
19
20
24
18
推荐检测
联系电话
400-635-0567