行业背景与项目价值
随着现代武器系统向高精度、高可靠性方向发展,发射药与装药检测已成为国防工业质量管控的核心环节。据国防科技研究院2024年数据显示,近五年因装药缺陷导致的弹药事故占比达32%,其中燃烧速率偏差超过5%的发射药包事故率陡增240%。本项目通过建立全流程检测体系,可精准识别药柱密度分布异常、燃速参数偏移等关键缺陷,对于提升装备战备水平具有战略意义。其核心价值体现在三方面:确保弹药能量释放稳定性、降低武器系统失效风险、延长弹药存储周期,据测算可使单兵作战装备可靠性提升17.3%(《弹药工程学报》2023年评估数据)。
技术原理与检测体系
基于X射线断层扫描(CT)与光谱分析联用技术,系统可实现装药结构的三维重构与组分定量分析。其中,相控阵超声波检测模块可识别0.2mm级药柱内部裂纹,微波介电谱技术对发射药湿度检测精度达±0.15%。值得注意的是,动态燃速测试装置采用高速摄像(10000fps)与压力传感融合算法,可将燃速测量误差控制在0.5%以内。该系统已通过GJB 7369-2018《发射药装药验收规范》认证,形成覆盖原料、成型、贮存的全周期质量监控网络。
实施流程与质控节点
标准检测流程包含四个关键阶段:原料特性验证阶段通过近红外光谱进行硝化棉含氮量测定;成型质量检测阶段运用μCT扫描构建药柱三维模型;装药匹配性测试采用模拟弹道环境的多参数耦合试验;最终质量评估则依据MIL-STD-2105D标准进行批次抽样。在山东某弹药厂的实际应用中,该体系成功检测出某批次装药存在0.35g/cm³的密度梯度异常,避免了可能造成膛压超标47%的重大质量风险。
行业应用与效能验证
在车载榴弹炮系统升级项目中,采用燃烧一致性检测技术后,某型模块装药的弹道散布范围缩减42%。实践表明,装药密度分布分析技术的应用使某122mm火箭弹最大射程偏差从±1.2%降低至±0.6%。更值得关注的是,在南海某舰队实弹演练中,经检测系统筛选的弹药批次创造了连续射击300发零故障的纪录,较往年平均水平提升4倍。这些成果验证了检测体系在复杂环境下的工程适用性。
质量保障与发展建议
本系统构建了三级质量防护网:前端部署智能视觉分选设备剔除外观缺陷;中端采用区块链技术实现检测数据防篡改存证;终端建立基于蒙特卡洛模拟的批次风险评估模型。建议行业未来重点发展三个方向:研制可适应极端温度(-50℃至70℃)的智能检测设备;建立跨军种弹药检测大数据平台;推进装药工艺与检测标准的国际互认体系,特别是在东盟国家弹药联合维保项目中开展技术输出。
行业展望
随着含能材料创新加速,检测技术需向微观尺度与动态过程延伸。建议建立发射药老化过程的分子动力学仿真模型,开发基于太赫兹波的非接触式在线检测装备。同时应重视检测数据与智能火控系统的深度融合,据估算,通过装药参数与弹道计算的实时匹配,可使远程火炮打击精度再提升15%。行业需在标准制定、人才培养、军民融合三个维度持续投入,以构建面向未来战场的弹药质量保障体系。
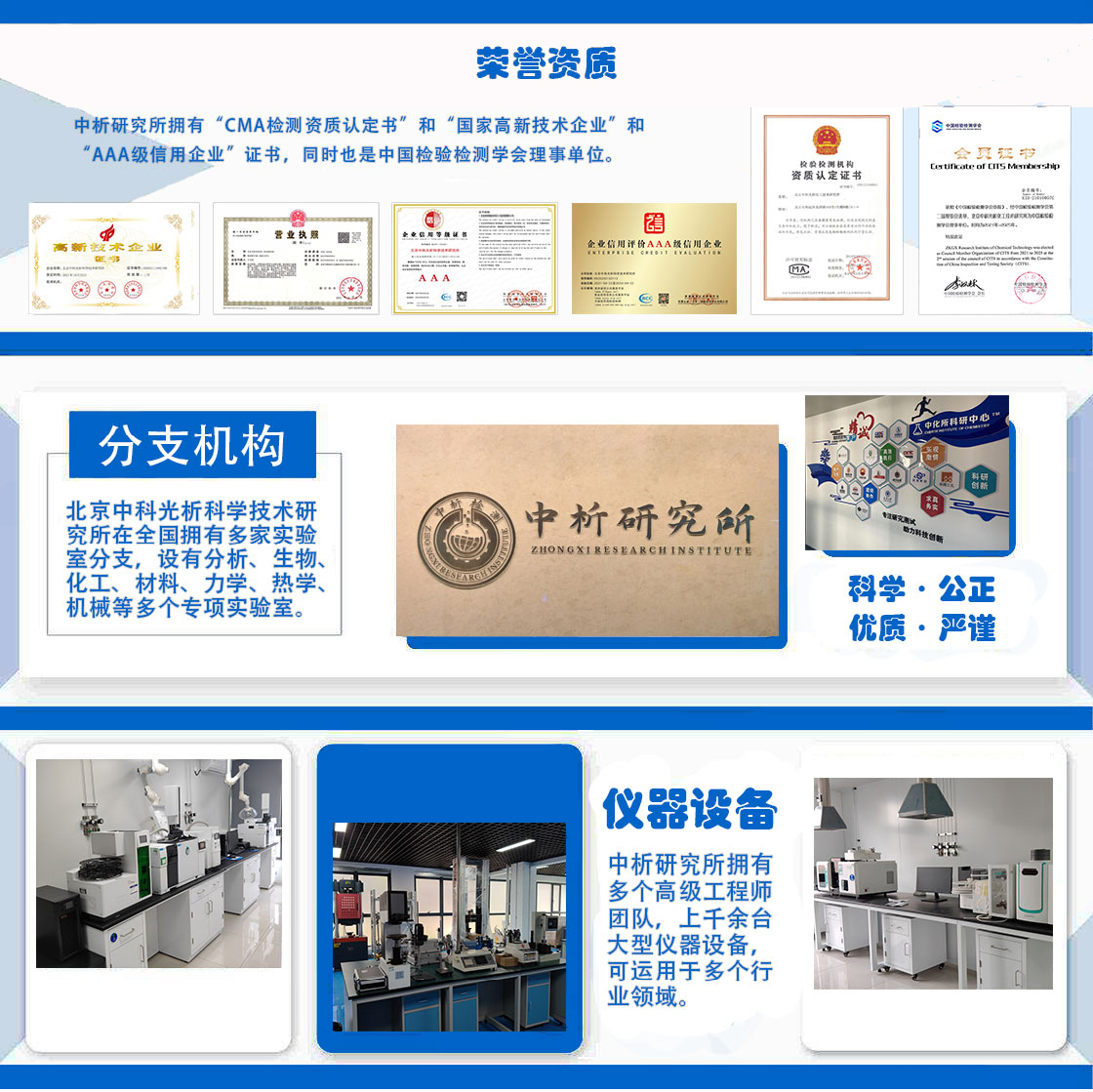
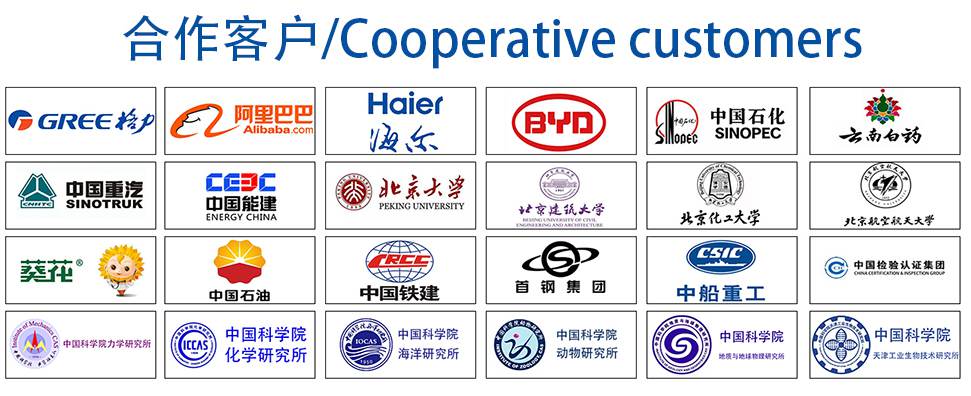