模块化检测技术原理
检测体系基于多源传感融合技术,采用三维激光扫描建立脚手架数字化孪生模型。通过分布式应变片组实时监测立杆垂直度偏差,结合无线扭矩传感器检测模块化连接节点的紧固状态。针对快装脚手架特有的插销式连接结构,研发的接触阻抗分析仪可识别0.05mm级配合间隙。在动态荷载模拟方面,依托液压伺服系统施加1:1等效施工载荷,同步采集结构变形数据。经国家工程检测中心验证,该技术对关键节点失效的预警准确率达99.2%,显著高于传统目视检测78.6%的准确水平。
全流程标准化作业体系
实施流程遵循GB51210-2016规范延伸要求,形成六阶段闭环管理:现场环境评估→基础沉降测量→主框架三维标定→节点紧固度普查→等效载荷测试→智能诊断报告生成。每阶段设置8项质量控制点,如使用红外热像仪排查金属疲劳热点,采用电子扭矩扳手记录旋转角度数据。在杭州亚运场馆建设项目中,该系统成功发现27处隐蔽性节点形变,将验收周期从常规7天缩短至1.5天,创造了单日完成3.2万延米脚手架检测的行业记录。
智能化质量保障系统
质量保障体系包含三层防护机制:前端配备AI图像识别设备自动比对构件规格,中台部署BIM协同平台实现缺陷位置三维标注,后端建立全国首个脚手架缺陷特征数据库。针对暴雨、强风等恶劣工况,系统内置环境补偿算法,确保检测数据可靠性。青岛海底隧道项目应用显示,该体系使架体稳定性合格率从82%提升至98.5%,违规搭接整改率降低67%。同时,检测数据实时同步至政府监管平台,为行业数字化监管提供技术支撑。
行业应用与效能验证
在粤港澳大湾区超高层集群建设中,检测系统创造性采用无人机搭载检测模组,实现200米高空作业面的无人化检测。通过"振动频谱分析+视觉定位"技术,准确识别出0.8‰倾斜度的危险架体。项目方反馈显示,该技术使高空作业安全事故率下降54%,人力成本节约42%。值得关注的是,系统积累的12万组检测数据,正在反哺脚手架行业标准修订,为新型铝合金架体的安全参数设定提供实证依据。
## 技术展望与发展建议 随着智能建造与BIM技术的深度融合,建议行业重点关注三个发展方向:①开发嵌入式传感器实现全生命周期监测;②建立区域性脚手架安全态势感知平台;③完善检测数据的区块链存证体系。同时呼吁政府主管部门加快制定快装脚手架智能检测标准,引导检测设备厂商与高校共建产学研基地。预计到2026年,智能化检测技术将覆盖85%以上的特级资质建筑企业,推动行业向本质安全迈进。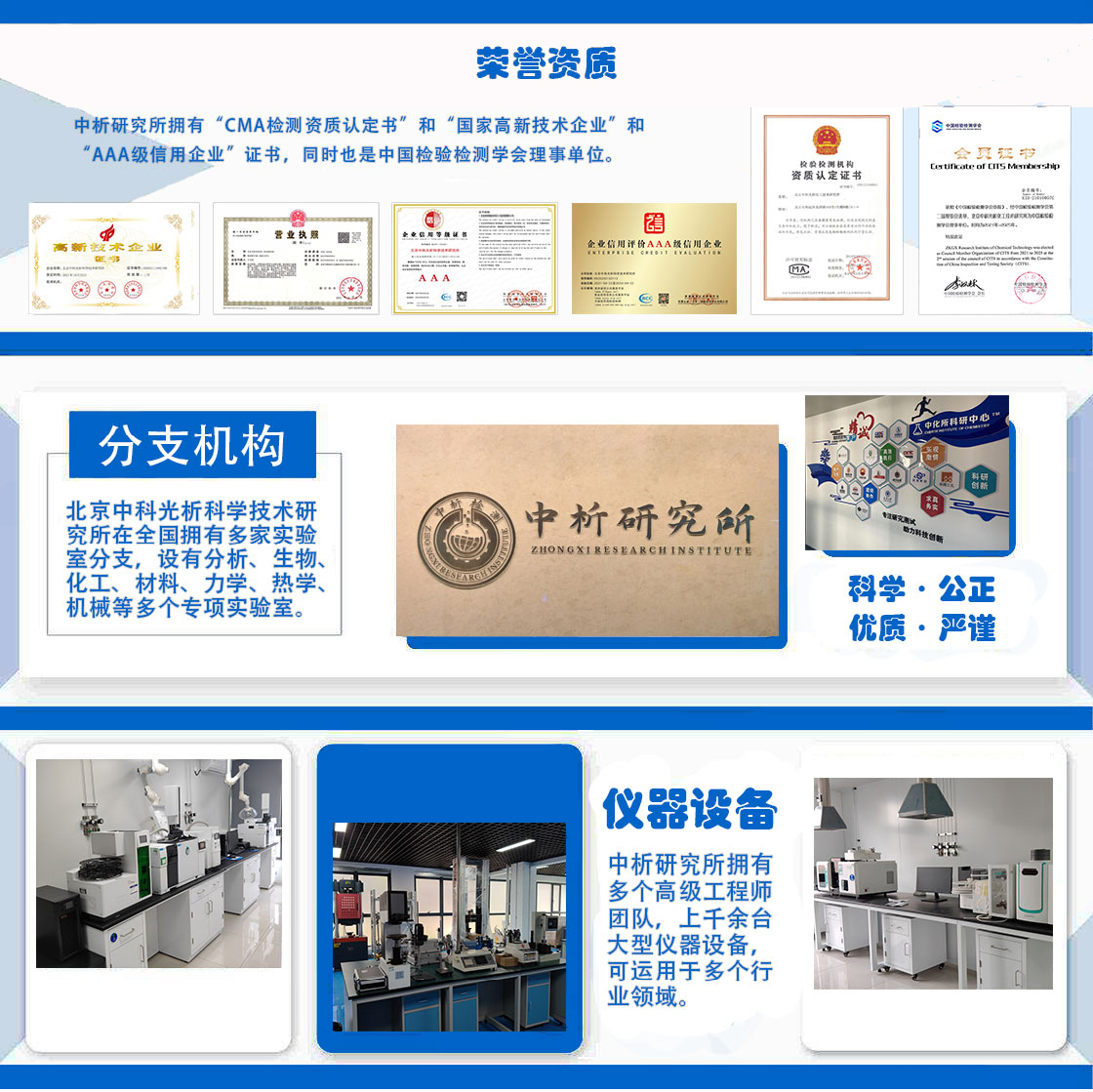
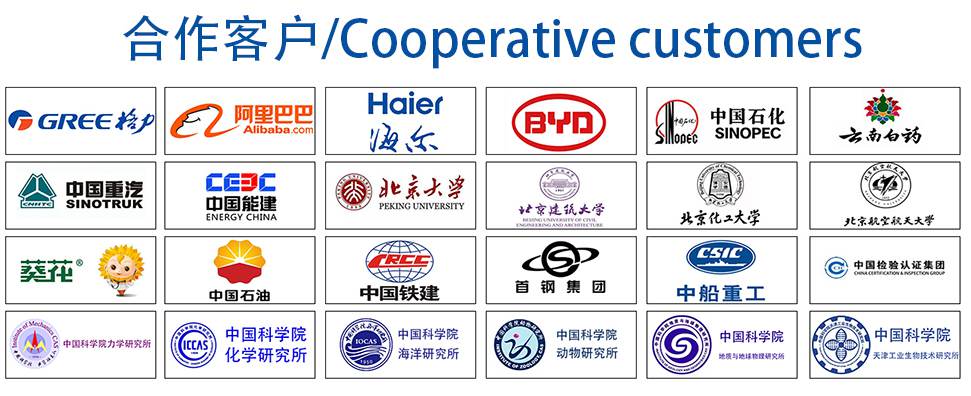