最大直径检测技术详解:核心检测项目与流程
引言
一、检测对象与参数
1. 适用对象
- 机械零件:轴类、轴承、齿轮、活塞等旋转对称部件
- 工业产品:管道、电缆、瓶罐类容器
- 医疗领域:肿瘤/器官的医学影像测量
- 精密元件:光学镜头、半导体晶圆
2. 核心检测参数
参数类型 | 技术指标 |
---|---|
几何尺寸 | 最大外径、最小内径、椭圆度 |
形状精度 | 圆度误差、圆柱度误差 |
位置公差 | 轴线偏移量、同心度偏差 |
二、核心检测项目
1. 静态尺寸检测
-
- 工具:千分尺、游标卡尺、三坐标测量机(CMM)
- 精度:±0.005 mm(高精度CMM可达μm级)
-
- 技术:激光扫描、光学影像测量、工业CT
- 优势:适用于软质材料或表面易损物件
2. 动态直径检测(产线在线监测)
- 技术方案:
- 激光位移传感器阵列
- 高速视觉检测系统(500-1000 fps)
- 检测能力:
- 实时监测旋转工件的最大径向跳动
- 识别直径波动>0.02 mm的异常
3. 复合参数分析
- 圆度-直径相关性分析 通过直径分布曲线推导圆度误差
- 热变形补偿检测 在温控环境下(±1℃)测量热膨胀导致的直径变化
三、检测设备与标准
1. 典型设备选型
设备类型 | 测量范围 | 精度等级 | 适用场景 |
---|---|---|---|
数显千分尺 | 0-500 mm | ±0.002 mm | 车间快速检测 |
影像测量仪 | 0.1-2000 mm | ±(1.5+L/200)μm | 复杂轮廓测量 |
激光扫描系统 | 1-5000 mm | ±0.01 mm | 大型工件在线检测 |
2. 国际/国内标准
- ISO 12180:圆柱度公差规范
- GB/T 1958:形状和位置公差检测规定
- ASME B89.1.5:精密孔径测量标准
四、检测流程规范
1. 标准化操作流程
-
- 清洁表面油污/毛刺
- 恒温处理(23±2℃维持4小时)
-
- 建立三维坐标系
- 确定测量基准轴线
-
- 轴向分段测量(通常≥5个截面)
- 圆周方向等角度采样(建议12点法)
-
- 计算最大直径极值
- 生成直径-角度分布云图
2. 关键控制点(KCP)
- 环境振动控制:≤0.5 m/s²(符合ISO 10816标准)
- 测量力控制:接触式测量施加压力≤2N
- 数据有效性验证:重复测量误差<标称精度的30%
五、典型应用场景
1. 汽车工业案例
- 发动机曲轴检测 要求:直径公差±0.015 mm 解决方案:采用多探头气动量仪实现100%在线全检
2. 医疗检测应用
- CT影像肿瘤测量 技术:三维重建算法+边缘梯度检测 精度:可识别≥0.5 mm的直径变化
六、常见问题与解决方案
问题现象 | 根本原因 | 改进措施 |
---|---|---|
重复测量数据离散度大 | 基准面定位误差 | 采用V型块定位+磁性夹具 |
非接触测量边缘模糊 | 表面反光特性异常 | 喷涂哑光显影剂(可清洗型) |
高温工况测量值漂移 | 材料热膨胀系数影响 | 引入温度补偿算法 |
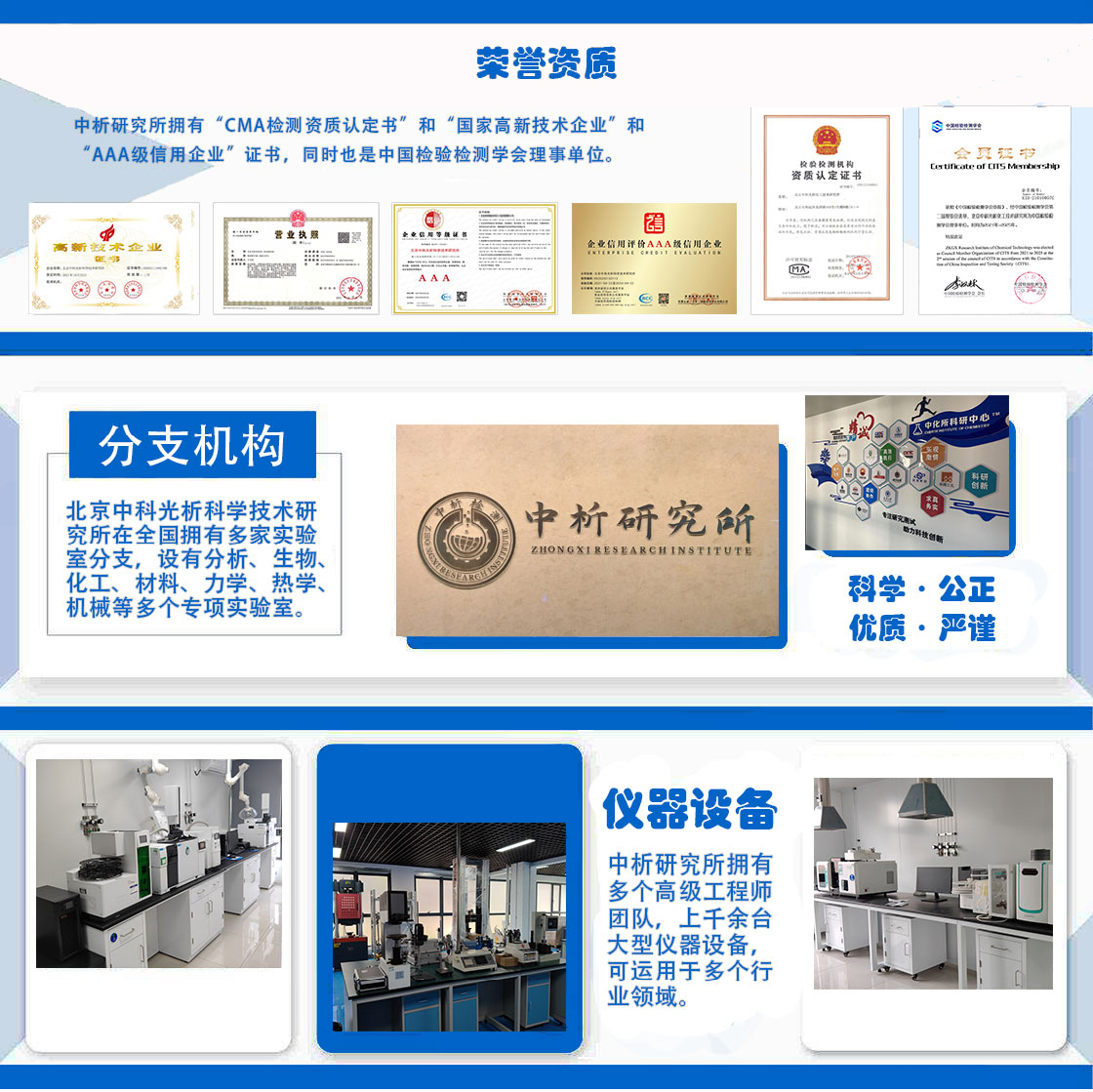
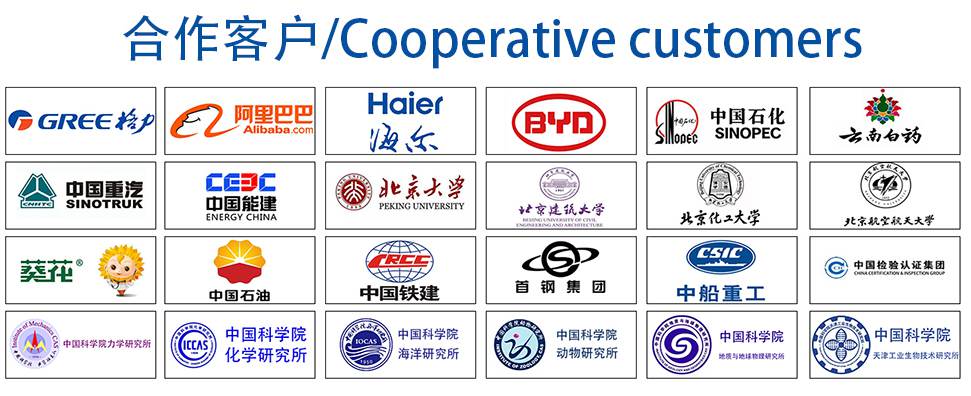
材料实验室
热门检测
17
17
15
14
15
18
14
17
18
15
14
15
20
25
23
18
18
17
23
20
推荐检测
联系电话
400-635-0567