氯乙烷检测技术及检测项目详解
一、氯乙烷检测的核心项目
- 环境空气中的氯乙烷浓度 检测指标:空气中氯乙烷的ppm或μg/m³级残留量。 场景:化工园区周边、垃圾填埋场等挥发性有机物(VOCs)重点区域。
- 水质检测 检测指标:水体中氯乙烷的溶解量(μg/L级),重点监控工业废水排放口或地下水污染。
- 土壤残留检测 检测指标:污染土壤中氯乙烷的迁移与降解情况(mg/kg级)。
- 工作场所空气浓度 限值参考:中国《工作场所有害因素职业接触限值》(GBZ 2.1-2019)规定,氯乙烷时间加权平均容许浓度(PC-TWA)为50 mg/m³。
- 生产设备泄漏检测 方法:使用便携式PID检测仪(光离子化检测器)进行实时监测,灵敏度可达ppb级。
- 药品溶剂残留 标准:根据《中国药典》,药品生产中使用氯乙烷作为溶剂时,残留量需低于50 ppm。
- 食品包装材料迁移量 检测指标:塑料包装中氯乙烷向食品模拟液(如乙醇溶液)的迁移量(μg/dm²)。
- 纯度检测 指标:工业级氯乙烷的纯度(≥99%)、杂质(如1,2-二氯乙烷)含量。
- 稳定性测试 内容:高温/光照条件下氯乙烷的分解产物分析(如HCl、乙烯)。
二、主流检测方法及适用场景
方法 | 原理 | 灵敏度 | 适用场景 |
---|---|---|---|
气相色谱法(GC) | 基于氯乙烷在色谱柱中的分离与FID/ECD检测 | 0.01 ppm | 实验室高精度定量(环境、食品) |
GC-MS联用 | GC分离后通过质谱定性定量 | 0.001 ppm | 复杂基质中的痕量检测(如血液) |
红外光谱法(IR) | 特征吸收峰(如C-Cl键振动)分析 | 1 ppm | 工业现场快速筛查 |
电化学传感器 | 氯乙烷与传感器发生氧化还原反应 | 0.1 ppm | 便携式实时监测(工厂巡检) |
三、检测标准与法规
- 中国标准
- HJ 734-2014(固定污染源废气 氯乙烷的测定 气相色谱法)。
- GB 31604.8-2021(食品接触材料 氯乙烯和氯乙烷迁移量测定)。
- 国际标准
- EPA Method 8015B(气相色谱法测定卤代挥发性有机物)。
- ISO 15337:2009(工作场所空气 氯代烃测定指南)。
四、注意事项
- 采样代表性:氯乙烷易挥发,需使用密封性好的采样管(如Tenax吸附管),避免运输损失。
- 干扰物排除:若样本中含其他卤代烃(如氯甲烷),需优化色谱条件(如DB-624色谱柱)。
- 安全防护:检测人员需佩戴防毒面具(如3M 6006滤毒盒),避免吸入高浓度蒸气。
五、应用实例
- 制药厂清洁验证:使用GC-MS检测反应釜清洗后氯乙烷残留,确保下一批次药品安全。
- 污染事故应急:某化工厂泄漏后,采用PID传感器快速定位泄漏点,结合GC分析周边土壤污染程度。
结语
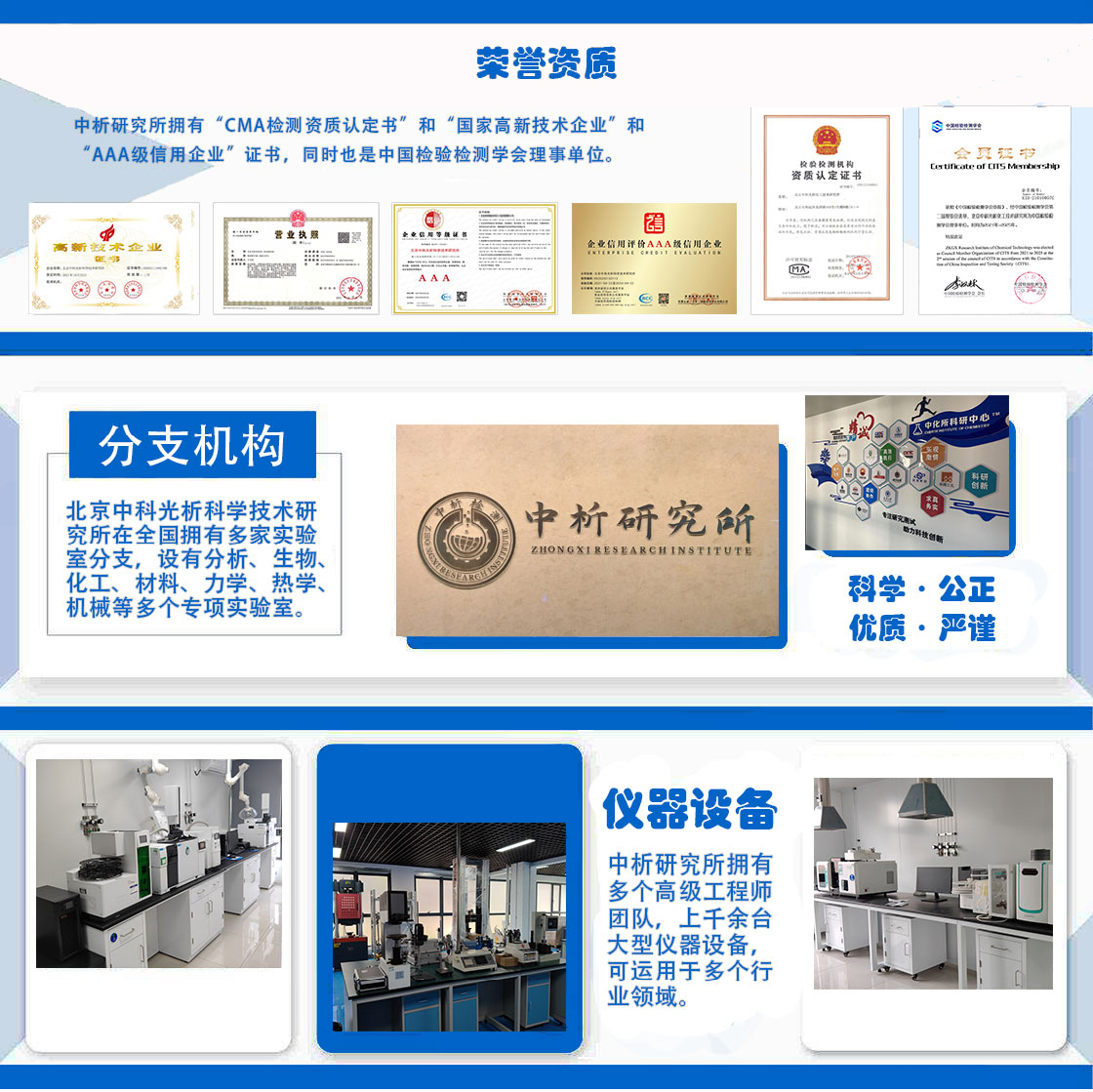
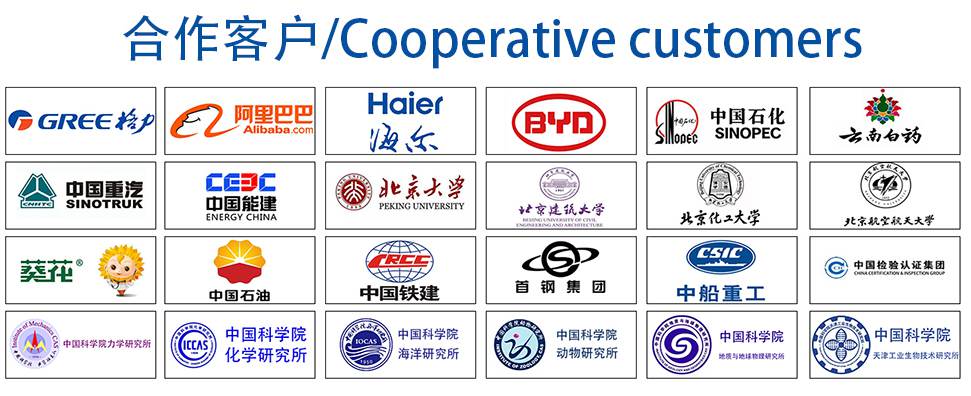
材料实验室
热门检测
41
42
42
41
57
52
60
55
60
62
61
62
57
59
51
57
51
57
50
56
推荐检测
联系电话
400-635-0567