悬挂短节检测项目与技术规范
一、外观及几何尺寸检测
-
- 检查表面是否存在裂纹、腐蚀、磨损、变形或机械损伤。
- 确认标识(如钢级、规格、生产批号)清晰可见且符合标准(API 5CT/ISO 11960)。
-
- 关键参数:外径、内径、长度、壁厚、螺纹参数(锥度、螺距、齿高)。
- 工具:数显卡尺、螺纹规、超声波测厚仪。
- 标准公差:参照API 5B规范,螺纹精度需满足±0.025 mm误差范围。
二、材料性能检测
-
- 使用光谱分析仪检测材质成分(C、Mn、Cr、Mo等元素),确保符合ASTM A182或API标准要求。
-
- 拉伸试验:测定抗拉强度、屈服强度及延伸率。
- 冲击试验(夏比V型缺口):评估低温韧性(-20℃~-40℃工况)。
- 硬度测试(布氏/洛氏):验证热处理均匀性,避免局部硬化或软化。
三、无损检测(NDT)
-
- 检测内部缺陷(夹杂、气孔、分层),探头频率2.5-5 MHz,覆盖全表面。
-
- 针对铁磁性材料表面及近表面裂纹检测,灵敏度需达到ISO 23278标准。
-
- 用于非磁性材料表面开口缺陷检查(灵敏度等级Ⅱ级及以上)。
四、螺纹连接性能检测
-
- 气密封试验(氮气加压至额定工作压力的1.25倍,保压5分钟无泄漏)。
-
- 模拟实际工况进行3次完整上扣/卸扣操作,检查螺纹磨损及粘扣现象。
五、特殊工况适应性检测
-
- 按NACE TM0177标准进行硫化物应力开裂(SSC)试验(载荷≥80% AYS)。
-
- 在模拟井下环境(如150℃、70 MPa)下测试密封性能与结构稳定性。
六、涂层与防腐检测
-
- 测量涂层厚度(如锌镀层≥50μm),划格法测试附着力(ASTM D3359)。
-
- 按ASTM B117进行500小时中性盐雾测试,评估耐腐蚀性能。
检测周期与标准依据
- 新件验收:全项目检测,符合API 5CT/API 5B规范。
- 在役复查:每12个月或作业前重点检测NDT+螺纹密封性。
- 异常工况后:强制进行UT+MT+尺寸复测。
上一篇:支撑剂性能检测下一篇:钻井液用褐煤树脂检测
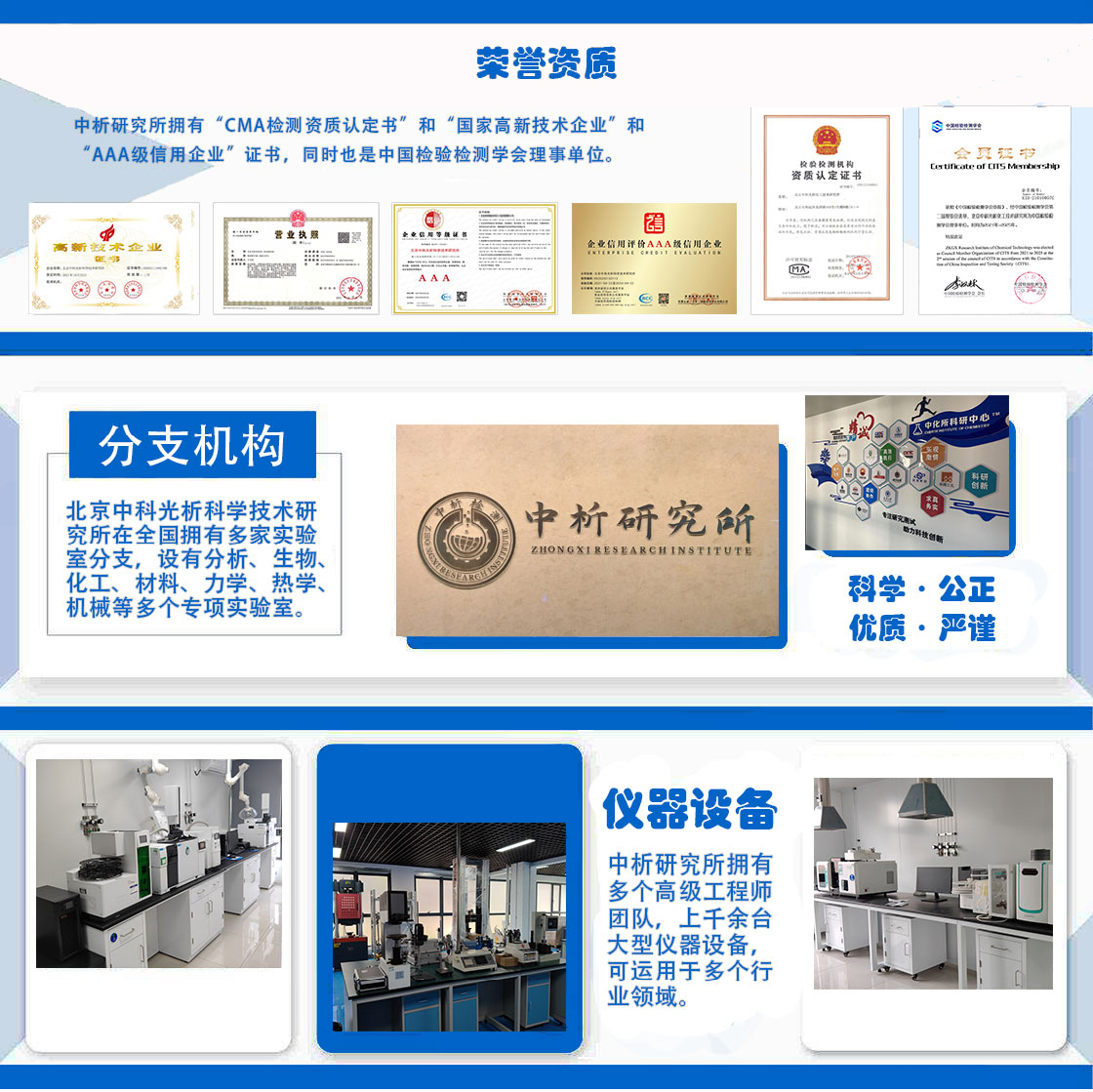
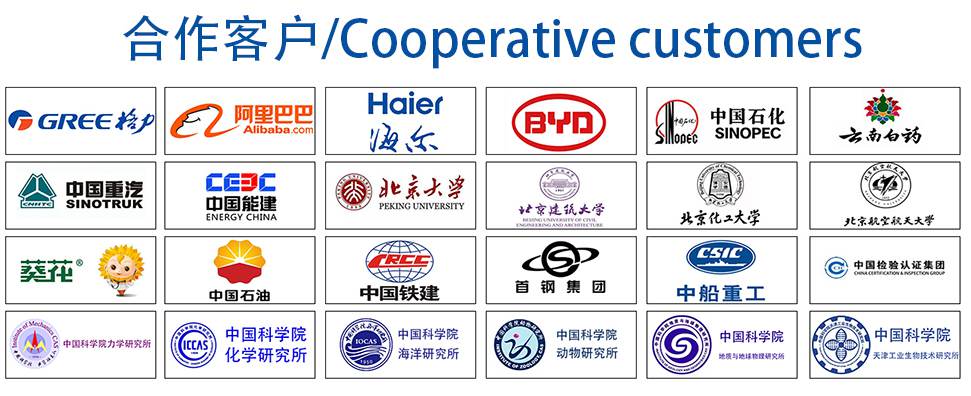
材料实验室
热门检测
156
122
114
123
122
124
137
129
128
140
135
126
130
122
117
125
123
123
127
127
推荐检测
联系电话
400-635-0567