玻璃容器含气饮料瓶检测技术及关键检测项目
一、检测背景
二、核心检测项目及方法
1. 物理性能检测
(1) 抗压强度测试
- 测试目的:验证瓶体承受内部气体压力和外部堆码压力的能力。
- 方法:
- 内压测试:向瓶内注水加压至标准压力(如1.2倍额定压力),保持1分钟,观察是否破裂。
- 垂直载荷测试:模拟堆码运输,施加垂直压力(如≥5000 N),检测瓶体变形量及破裂阈值。
(2) 垂直度偏差检测
- 意义:垂直度不良可能导致灌装线卡瓶或密封不严。
- 工具:垂直度检测仪,测量瓶体轴线与基准面的最大偏离角度(标准通常≤1.5°)。
(3) 瓶口尺寸精度
- 关键参数:瓶口外径、螺纹尺寸、密封面平整度。
- 设备:光学投影仪或三坐标测量仪,符合ISO 9001尺寸公差标准(如±0.2 mm)。
2. 化学稳定性检测
(1) 耐水解性能
- 方法:将玻璃瓶置于高温高压水蒸气环境(如121℃、2小时),观察表面蚀斑或析出物。
- 标准:通过GB 4544《啤酒瓶》中耐水等级≥HC3级要求。
(2) 重金属迁移测试
- 项目:铅(Pb)、镉(Cd)、砷(As)等有害元素溶出量。
- 流程:模拟酸性环境(4%乙酸溶液),70℃浸泡24小时,ICP-MS检测溶出量。
- 限值:符合GB 4806.5《食品接触玻璃制品》标准。
3. 密封性检测
(1) 压力保持测试
- 方法:充填二氧化碳至额定压力后密封,静置24小时,压力下降率应≤5%。
(2) 泄漏检测
- 在线检测:采用真空衰减法或高压放电法,快速识别微米级漏点。
4. 外观缺陷检测
(1) 表面缺陷
- 类型:气泡(直径≤1.5 mm且无集中分布)、裂纹、结石(玻璃杂质)、划痕。
- 设备:机器视觉系统(AOI),结合高分辨率摄像头与AI算法识别缺陷。
(2) 光洁度检测
- 要求:内壁粗糙度Ra≤0.8 μm,避免饮料残留滋生细菌。
5. 其他专项检测
- 耐热冲击性:冷热温差骤变测试(如从0℃骤升至60℃),检测抗爆裂性能。
- 循环疲劳测试:模拟多次开盖过程,验证瓶口螺纹耐久性。
三、检测标准与质量控制
- 国际标准参考:
- ISO 8162(玻璃容器抗内压力试验)
- ASTM C147(玻璃瓶垂直度检测)
- 国内标准:
- GB 4544《啤酒瓶》
- QB/T 3729《玻璃容器抗热震性试验方法》
- 质量控制流程:
- 抽样频率:每批次按GB/T 2828.1执行AQL抽样方案。
- 不合格品处理:隔离、追溯生产批次并分析工艺缺陷。
四、检测设备与技术发展
- 自动化趋势:集成压力测试机、光学检测仪、密封性测试模块的在线检测系统可覆盖80%以上检测项目。
- 智能分析:AI算法辅助缺陷分类,误检率<0.1%。
五、总结
上一篇:动车组用中空玻璃检测下一篇:玻璃容器 白酒瓶检测
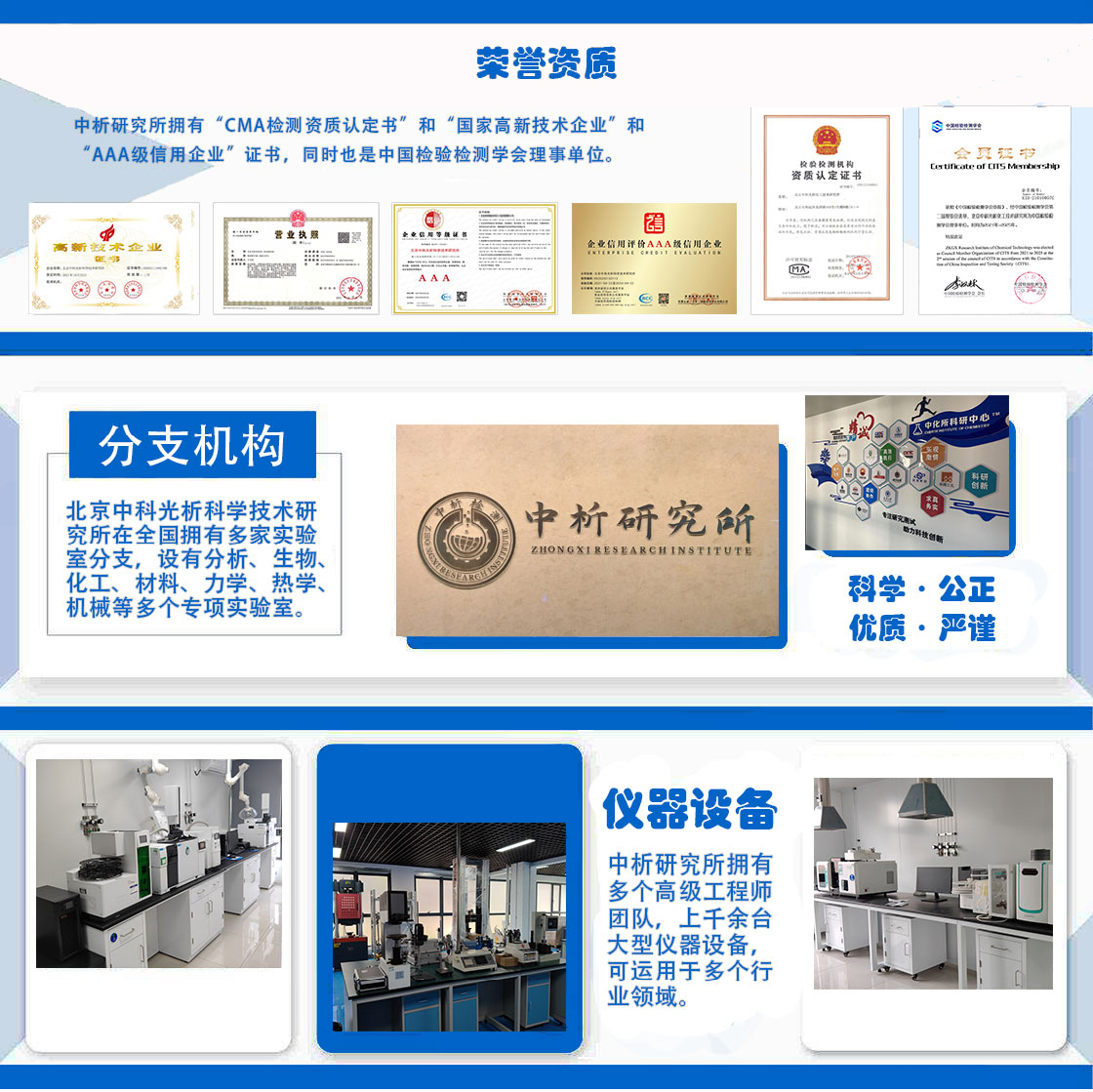
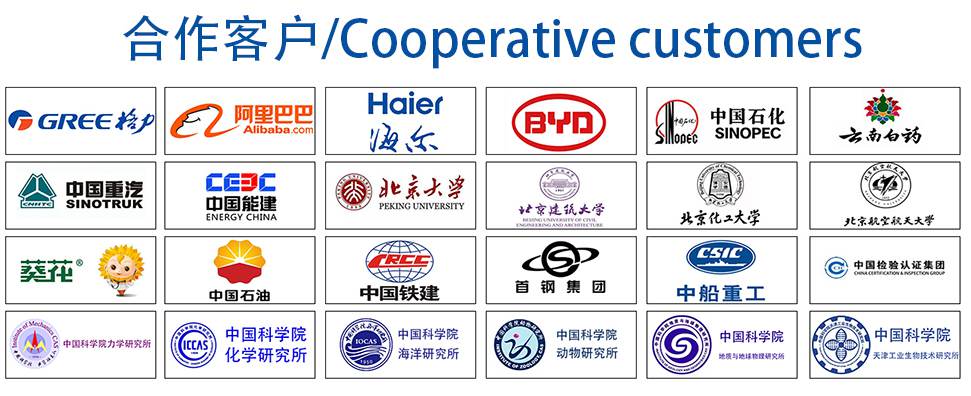
材料实验室
热门检测
268
226
202
211
208
211
222
215
226
228
212
212
215
213
206
204
221
207
219
213
推荐检测
联系电话
400-635-0567