先导式减压阀检测的重要性
先导式减压阀作为工业管道系统中的核心控制元件,广泛应用于石油化工、电力系统、水处理等领域。其主要功能是通过调节导阀与主阀的联动作用,稳定输出压力并保护下游设备安全。由于长期处于高压、高温或腐蚀性介质环境中,阀体易出现密封失效、导阀卡滞、调压偏差等问题。定期开展系统的先导式减压阀检测,能够及时排查隐患、延长使用寿命,同时确保工艺流程的稳定性和安全性。检测过程需结合结构特性、工况条件及行业标准,形成完整的评估方案。
关键检测项目及方法
1. 外观与密封性检测
首先对阀体表面进行目视检查,确认是否存在腐蚀、裂纹或机械损伤;通过着色渗透法检测关键焊缝的完整性。密封性测试需在额定压力下进行,使用氮气或水介质加压至1.5倍工作压力并保压10分钟,观察压力表数值变化,泄漏率需符合GB/T 12246-2006标准要求。
2. 压力调节性能测试
在试验台上模拟实际工况,逐步调整进口压力并记录出口压力变化曲线。通过导阀设定目标压力值,验证主阀响应精度及稳定性。重复3次测试后,偏差应小于±5%,且无振荡现象。流量特性测试需结合不同开度下的压力-流量曲线,分析减压阀的动态调节能力。
3. 导阀动作灵敏性检测
采用压力阶跃法对导阀进行冲击试验,利用高频压力传感器采集导阀启闭时间及复位精度。标准要求导阀全行程动作时间不超过0.5秒,复位滞后误差需小于设定值的2%。同时检查导阀弹簧是否变形、膜片是否破损。
4. 材料耐腐蚀性评估
对阀体、阀座及密封件取样进行金相分析,结合介质成分检测结果,评估材料的耐腐蚀等级。重点检测导阀腔体内部是否因气蚀产生蜂窝状损伤,必要时进行硬度测试和光谱分析以确认材料劣化程度。
5. 综合性能模拟试验
在闭环测试系统中模拟实际工况,连续运行72小时监测全参数变化。包括突发压力冲击试验、交变载荷疲劳试验及高温/低温适应性测试,验证减压阀在极端条件下的可靠性。
检测结果分析与处理
根据检测数据生成三维性能图谱,对比出厂参数和历史记录,判定阀体剩余寿命。对密封面磨损、导阀卡滞等典型问题,可采用激光熔覆修复或更换高精度导阀组件。检测报告需包含改进建议,如调整弹簧预紧力、优化导阀孔径设计等,确保设备达到最佳运行状态。
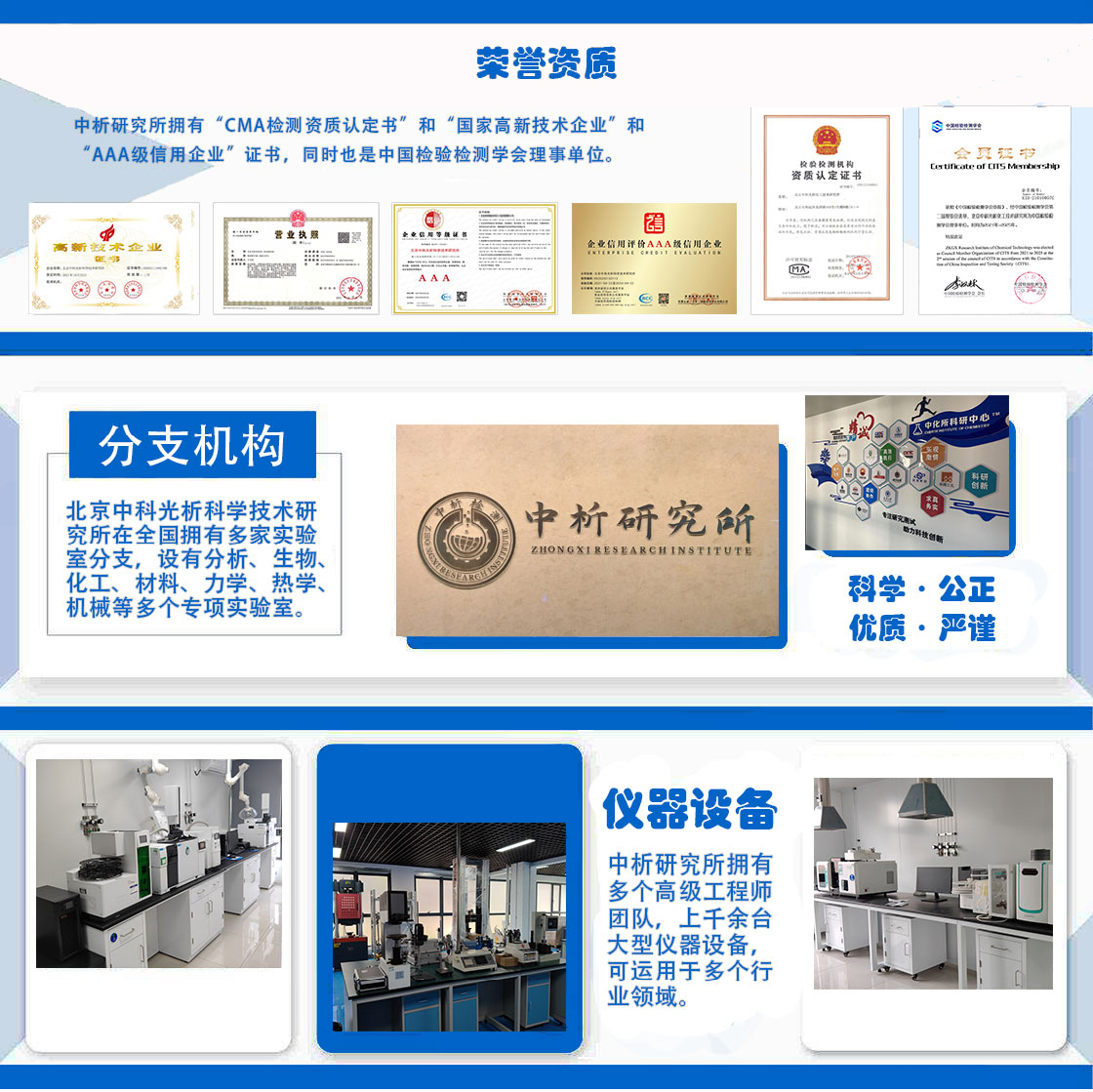
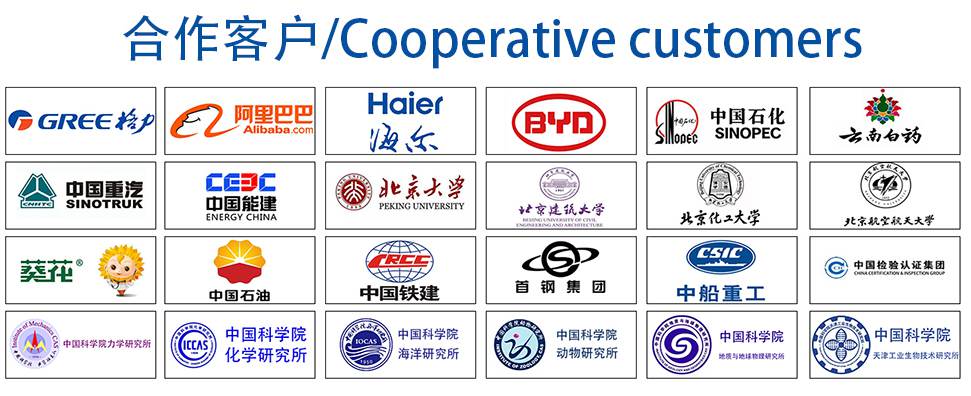