包装机械检测的重要性与行业需求
在食品、医药、日化、电子等现代制造领域,包装机械作为生产线核心设备,其性能直接影响产品质量、生产效率及企业运营成本。随着自动化与智能化技术的快速发展,包装机械检测已成为确保设备合规性、安全性和稳定性的关键环节。通过系统的检测流程,企业不仅能规避因机械故障导致的生产事故,还能优化设备参数以提升包装精度,减少材料浪费。根据ISO 9001质量管理体系及GB/T 19001国家标准规范,第三方检测机构需对包装机械实施全维度技术评估,为设备出厂、验收及日常维护提供科学依据。
包装机械核心检测项目解析
1. 机械性能测试
包括运行速度检测(如每分钟包装次数)、传动系统稳定性分析、密封压力测试(针对真空包装机)以及送料机构精准度验证。通过高精度传感器记录设备在满载、空载及极端工况下的振动、噪音数据,评估机械结构的耐久性与可靠性。
2. 电气安全检测
依据IEC 60204-1标准,重点检测电机绝缘电阻(需≥1MΩ)、接地连续性(接地电阻≤0.1Ω)、应急制动响应时间(≤2秒)及控制系统抗干扰能力。对伺服驱动系统进行过载保护测试,确保电路设计符合防爆、防尘、防水等级要求。
3. 材料兼容性测试
模拟实际生产环境,验证机械与包装材料(如PE膜、铝箔、玻璃容器)的适配性。通过300小时连续运行试验,检测热封刀头耐腐蚀性、传送带抗磨损系数,防止材料残留导致的产品污染风险。
4. 智能化功能验证
针对配备PLC、机器视觉系统的设备,需测试自动纠偏功能的定位精度(误差≤±0.5mm)、重量检测模块的重复性(RSD<0.3%),以及MES系统数据交互的实时性与准确性。通过注入模拟故障信号,检验设备自诊断系统的报警响应机制。
5. 环境适应性试验
在温湿度试验箱中模拟-10℃至50℃极端环境,检测机械润滑系统效能、热收缩炉温控精度(波动≤±1.5℃)及电子元件的工作稳定性。盐雾测试(48小时)可评估金属部件在潮湿环境的防锈能力。
检测流程标准化建设
专业检测机构采用三级检测体系:出厂前完成72小时空载跑合试验,现场安装后进行负载性能校准,每季度执行预防性维护检测。运用激光干涉仪、扭矩测试仪等齐全设备,结合大数据分析平台,生成包含设备OEE(整体设备效率)、MTBF(平均无故障时间)等关键指标的检测报告,为企业设备管理决策提供数据支撑。
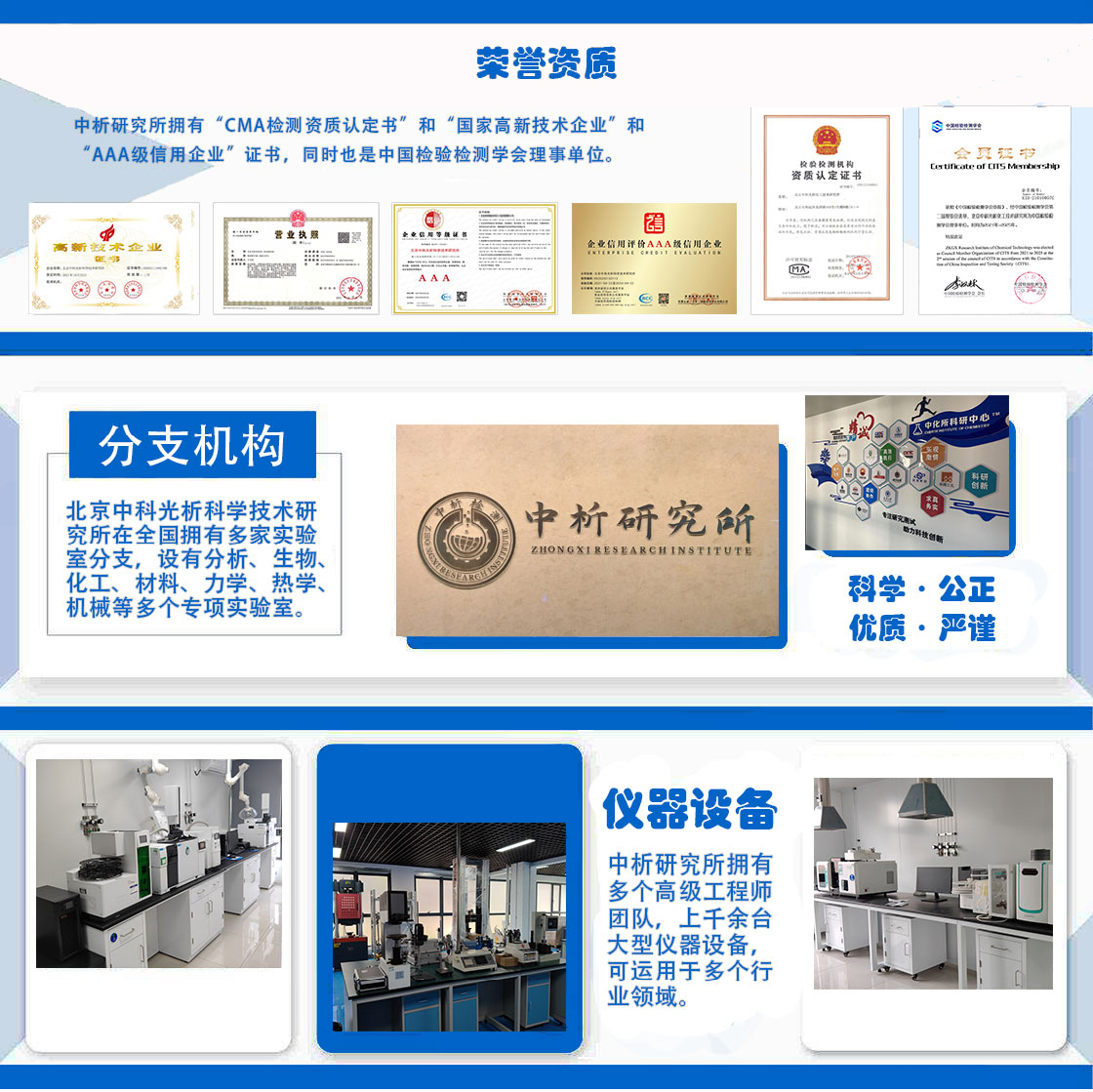
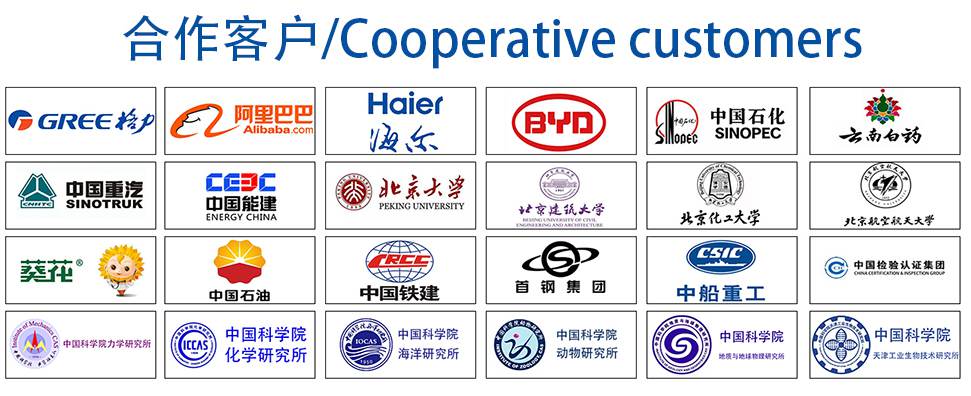