公路车辆用低压电缆检测的重要性
公路车辆用低压电缆作为汽车电气系统的核心组成部分,承担着电力传输、信号控制及设备连接等关键功能,广泛应用于乘用车、商用车及新能源车辆中。随着汽车智能化、电动化趋势的加速,电缆的安全性、可靠性和耐久性要求显著提高。为确保车辆在复杂工况下的稳定运行,针对低压电缆的标准化检测成为行业规范的重要环节。根据国际标准(如ISO 6722、GB/T 25085)及车企技术要求,检测项目需覆盖电气性能、机械强度、环境适应性等多个维度,以全面评估电缆质量。
关键检测项目及技术要求
1. 导体性能测试
导体是电缆传输电流的核心部分,需通过电阻率、截面积均匀性及抗拉强度等测试。例如,依据ISO 6722标准,导体电阻偏差不得超过标称值的±2%,同时需验证导体在反复弯折后的断裂伸长率,以确保其在车辆振动环境下的稳定性。
2. 绝缘与护套材料检测
绝缘层和护套的材质直接影响电缆的耐温、耐油及抗老化能力。检测项目包括: - 热老化测试:在125℃高温下持续暴露168小时,观察材料硬度变化与开裂现象; - 抗撕裂强度测试:模拟安装过程中的机械损伤风险; - 耐油性测试:将试样浸泡于汽油或机油中48小时,验证体积膨胀率是否超标。
3. 耐候性验证
车辆电缆需适应极端温度、湿度及紫外线环境。通过以下测试评估其适应性: - 温度循环测试:-40℃至+120℃间快速交变100次,检查绝缘层龟裂情况; - 湿热老化测试:在85℃、85%湿度下持续1000小时,评估绝缘电阻衰减率; - UV暴露测试:模拟阳光照射2000小时,检测护套材料脆化程度。
4. 电气性能验证
包括绝缘电阻(≥100MΩ/km)、耐电压(2000V/5min无击穿)及屏蔽效能测试(针对CAN总线等高频信号电缆),确保电磁兼容性符合ISO 11452系列标准要求。
5. 机械性能试验
模拟实际使用场景的机械应力,如: - 弯曲试验:以20倍电缆直径的弯折半径进行5000次循环; - 抗压试验:施加1000N压力持续1小时,检测绝缘层变形量; - 耐磨试验:在钢丝刷摩擦装置下测试护套磨损深度。
6. 阻燃性能评估
依据UL 1581或GB/T 18380标准进行垂直燃烧测试,要求自熄时间≤60秒,炭化长度≤50mm。对新能源车辆高压线束还需增加氧指数(OI≥32%)测试。
7. 环保与毒性检测
针对RoHS 2.0指令,检测铅、镉等重金属含量;同时需通过VOC(挥发性有机物)释放量测试,满足车内空气质量要求。
8. 标识耐久性验证
电缆表面印刷的型号、规格等标识需通过酒精擦拭、高温水浸等测试,确保在使用周期内清晰可辨。
检测流程与质量管控
完整的检测流程涵盖原材料入厂检验、生产过程抽检及成品综合测试三个阶段。车企及零部件供应商需建立ISO 17025认证实验室,结合自动化检测设备(如高压测试仪、环境试验箱)与人工目检,实现全生命周期质量追溯。对于新能源车辆,还需增加高压绝缘监测、EMC抗干扰等专项测试。
结语
公路车辆用低压电缆的检测体系是保障行车安全的核心技术屏障。随着新材料、新工艺的应用,检测标准将持续迭代升级。建议企业动态跟踪IEC、SAE等行业规范,通过数字化检测平台优化质量控制流程,为智能网联汽车的快速发展提供可靠保障。
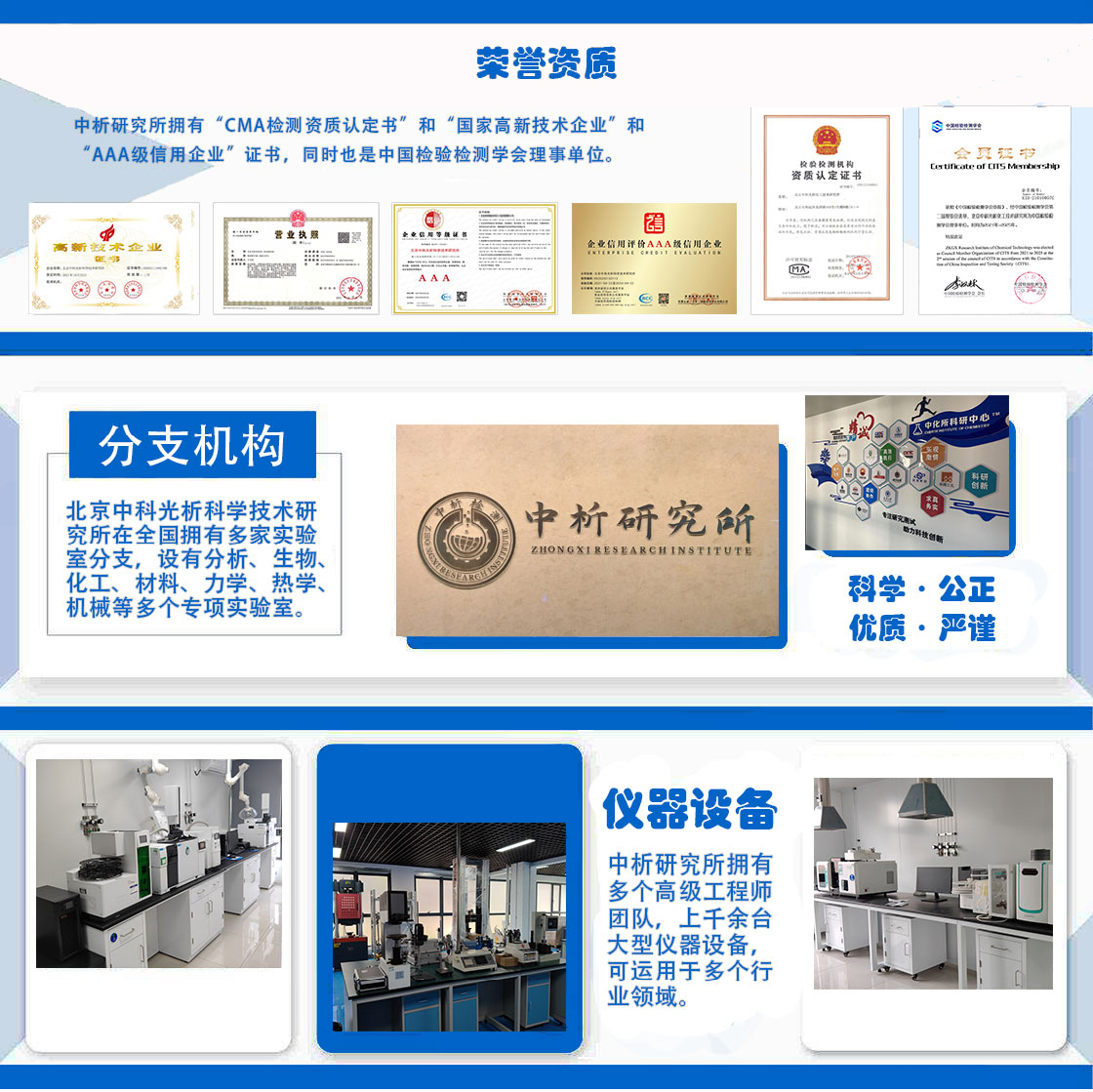
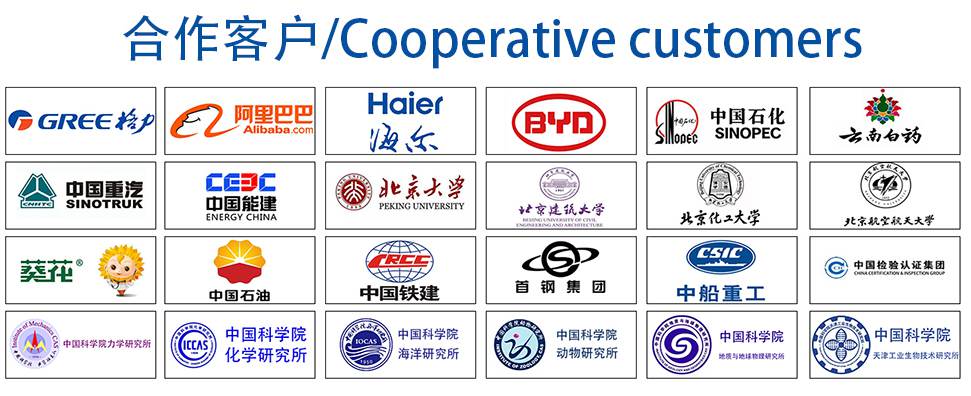