金属材料(微观结构)检测的重要性与核心方向
金属材料的微观结构直接决定了其力学性能、耐腐蚀性、加工性能及使用寿命。通过微观结构检测,可以精准分析材料的晶粒尺寸、相组成、夹杂物分布、缺陷特征等关键参数,为材料研发、生产工艺优化和产品质量控制提供科学依据。在航空航天、汽车制造、能源装备等领域,微观结构检测已成为材料性能评估的核心环节,帮助工程师预测材料在实际工况下的行为,避免因微观缺陷导致的失效风险。
关键检测项目与技术手段
1. 金相组织分析
通过光学显微镜(OM)或扫描电子显微镜(SEM)观察材料的显微组织,包括晶粒形态、第二相分布及晶界特征。典型方法包括: - 试样制备:切割、镶嵌、研磨、抛光、化学/电解腐蚀 - 图像分析:定量统计晶粒尺寸、孔隙率、夹杂物含量
2. 晶粒度测定
依据ASTM E112标准,采用截点法或面积法计算晶粒度等级(G值)。晶粒尺寸直接影响材料的强度、韧性和疲劳性能,例如细晶强化机制可显著提升铝合金的屈服强度。
3. 相组成与相变分析
结合X射线衍射(XRD)和能谱分析(EDS),识别金属中奥氏体、铁素体、碳化物等相的体积分数及其分布。例如,通过原位高温XRD可动态监测合金在热处理过程中的相变行为。
4. 微观缺陷检测
利用电子背散射衍射(EBSD)或透射电子显微镜(TEM)检测位错密度、孪晶界、微裂纹等亚结构特征。例如,钛合金中的位错缠结程度与其抗蠕变性能密切相关。
5. 元素偏析与扩散分析
通过电子探针(EPMA)或激光诱导击穿光谱(LIBS)绘制元素分布图,量化合金成分的均匀性。如不锈钢中Cr/Mo元素的偏析可能导致局部耐蚀性下降。
6. 残余应力评估
采用X射线衍射法或中子衍射法测量材料表面及内部残余应力分布,指导焊接、铸造等工艺的优化,防止应力腐蚀开裂风险。
前沿技术与标准化发展
随着聚焦离子束(FIB)三维重构、原子探针层析技术(APT)等齐全手段的应用,微观结构检测正从二维向三维、从微米级向原子级延伸。国际标准化组织(ISO)和ASTM持续更新检测方法标准(如ISO 643:2020),推动检测结果的跨实验室可比性。
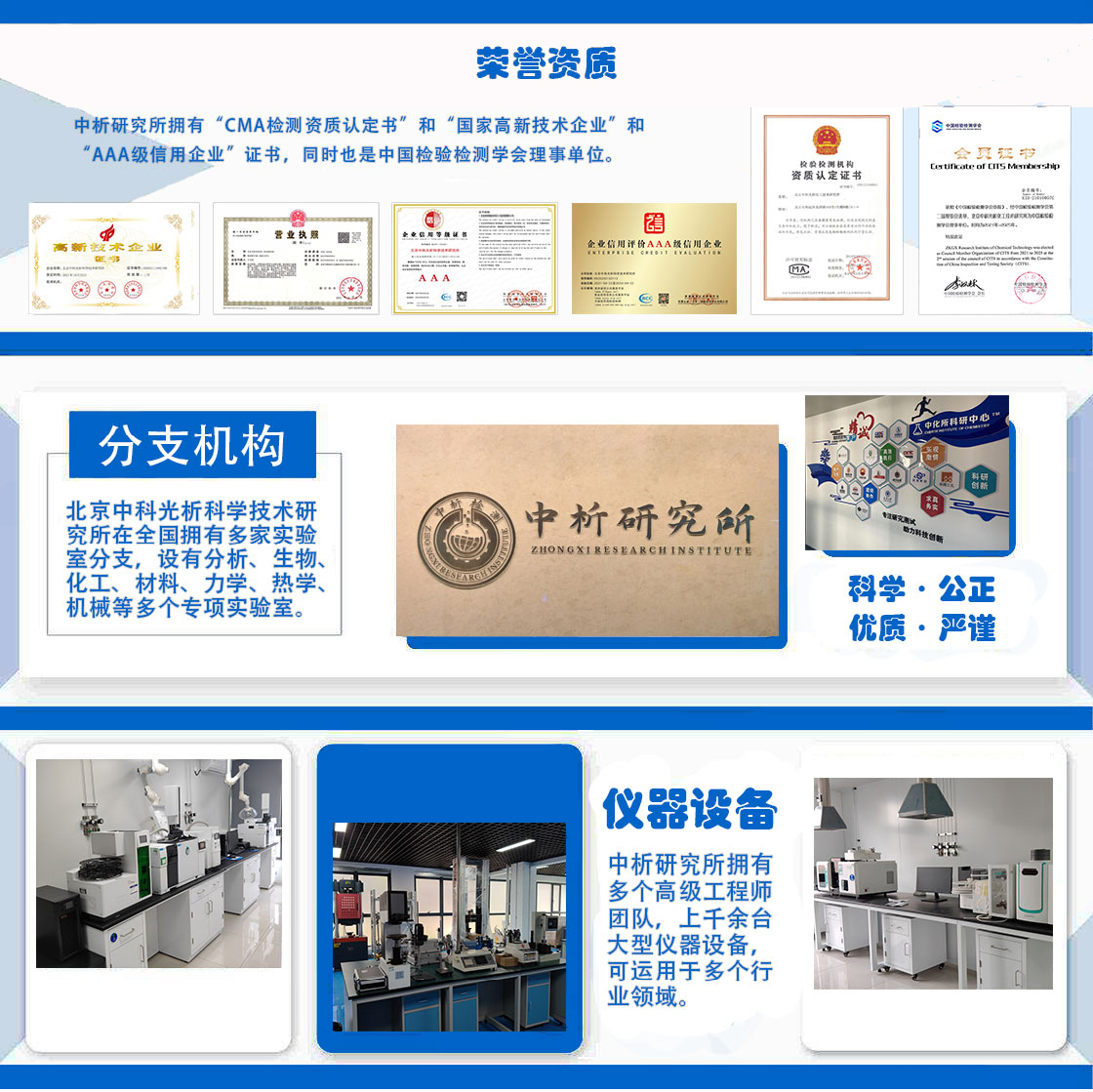
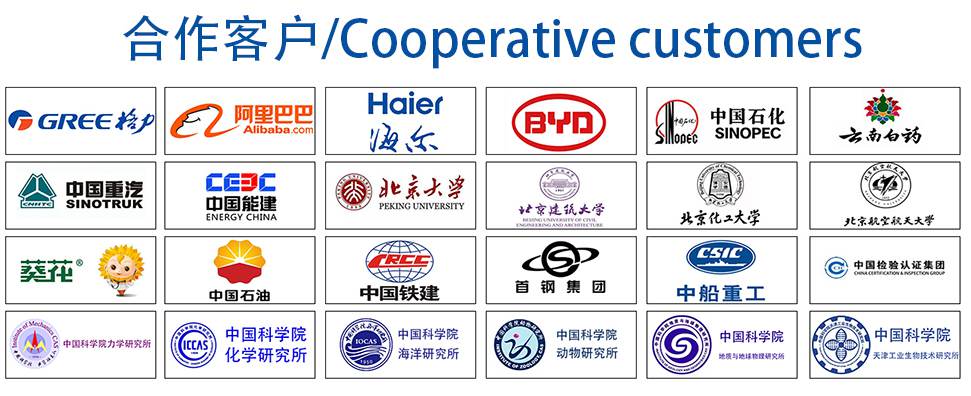