机车车辆车体检测的重要性
机车车辆车体作为承载人员与设备的核心结构,其安全性、可靠性和耐久性直接关系到铁路运输效率与乘客生命安全。随着列车运行速度提升和运营环境复杂化,车体检测已成为轨道交通运维体系中不可或缺的环节。据统计数据显示,车体结构缺陷导致的事故占比超过30%,而定期检测可使故障发生率降低65%以上。现代车体检测不仅包含传统目视检查,更融合了智能传感、无损探伤、三维建模等齐全技术,形成了覆盖静强度、动态响应、材料损伤的全生命周期检测体系。
主要检测项目分类
1. 外观完整性检测
包括车体表面锈蚀检查、覆盖件变形量测量、漆膜附着力测试等。采用激光测距仪和红外热成像技术,可精确识别0.2mm级凹陷变形,发现潜在的结构开裂风险。重点区域如车顶导流罩、端部防爬装置需进行200%放大倍率显微检测。
2. 结构强度检测
通过有限元仿真与实物测试相结合,评估车架焊缝强度、底架横梁载荷能力等关键参数。采用分布式光纤传感器网络监测应力分布,要求纵向压缩载荷不低于2.5MN,扭转刚度需满足±5°范围内无塑性变形。
3. 功能部件检测
包含车门气密性试验(保压3kPa/10min泄漏率<5%)、车窗抗冲击测试(1kg钢球9m/s冲击无贯穿)、贯通道波纹板疲劳试验(50万次伸缩循环后无裂纹)等项目。动车组车头鼻锥部位需额外进行风洞气动性能验证。
4. 无损检测(NDT)应用
采用相控阵超声波检测轮毂座区域、磁粉探伤检查转向架焊缝、工业CT扫描评估铸件内部缺陷。对于铝合金车体,需实施涡流检测以发现0.5mm以上深度裂纹,检测覆盖率要求达到100%。
5. 动态性能监测
在环形试验线进行运行状态检测,包括车体振动频率分析(需避开4-8Hz人体敏感区间)、噪声源定位检测(客室噪声限值68dB(A))、气密性动态保持测试(隧道通过时压力变化≤800Pa/3s)。
6. 专项检测项目
针对特殊运营环境增设检测模块:高寒地区车辆需进行-40℃低温冷脆性试验;沿海线路增加盐雾腐蚀检测;高原动车组需验证车体气密保持能力(海拔4000m保持2000Pa/10min)。新型碳纤维复合材料车体还需进行雷击防护性能验证。
智能化检测发展趋势
当前行业正推进基于数字孪生的预测性检测系统,通过车载监测终端实时采集300+项运行参数,结合大数据分析实现缺陷早期预警。机器人检测系统已可完成85%车底部件自动巡检,检测效率提升40%的同时,将漏检率控制在0.3%以下。
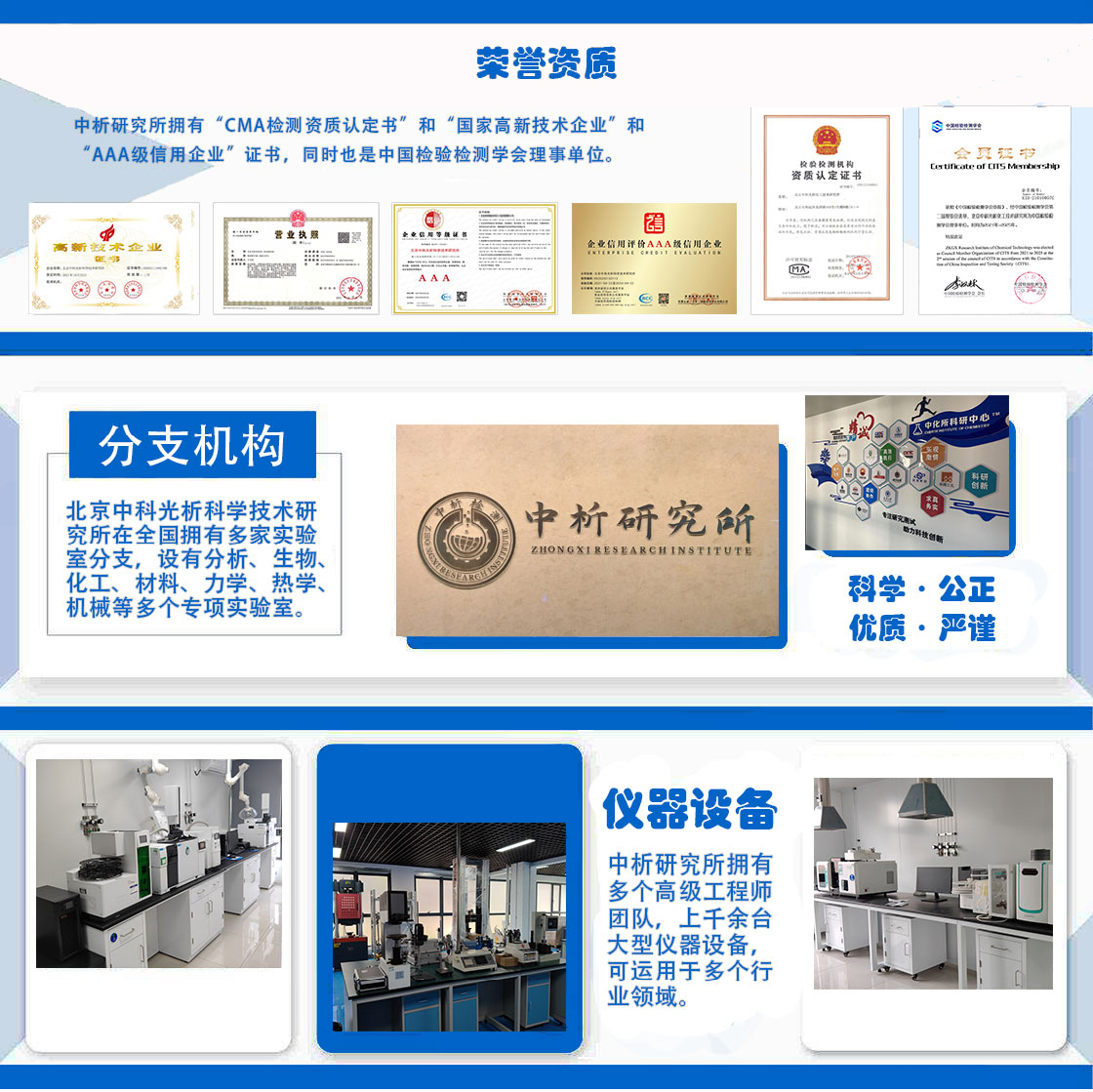
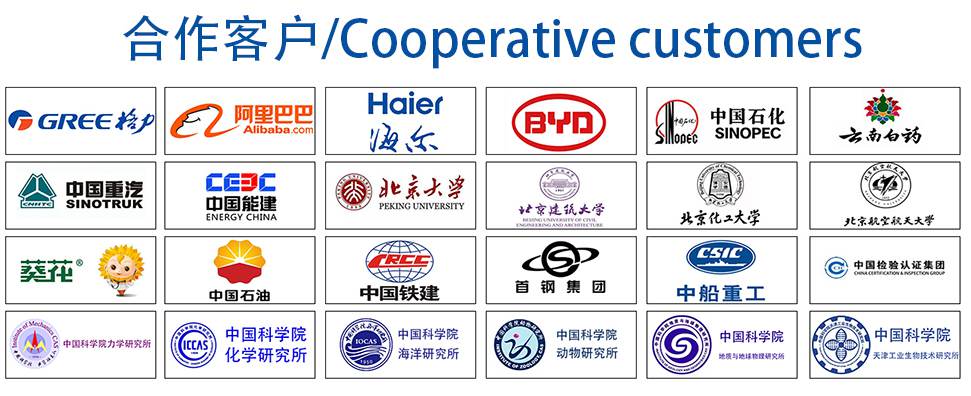