机车车辆转向架部件检测的重要性
机车车辆转向架是承载车体重量、传递牵引力与制动力的核心部件,其性能直接影响列车的运行安全、平稳性和使用寿命。由于转向架长期承受复杂交变载荷和恶劣环境的影响,部件易出现疲劳裂纹、磨损变形、紧固件松动等问题。因此,定期开展转向架部件检测是铁路运输安全维护中不可或缺的环节。通过科学系统的检测,可及时发现潜在故障,避免因部件失效导致的脱轨、制动失灵等重大事故,同时还能优化维修周期,降低运营成本。
核心检测项目及方法
1. 构架结构完整性检测
转向架构架是支撑其他部件的基体,需重点检查焊接部位裂纹、母材腐蚀和变形情况。采用磁粉探伤(MT)或渗透探伤(PT)检测焊缝缺陷;通过三维激光扫描或全站仪测量构架几何尺寸,对比设计值判断形变量。
2. 轮对与轴箱状态检测
轮对方面,需测量轮缘厚度、轮辋宽度及轮径差,使用超声波探伤(UT)检测轮座内部缺陷。轴箱轴承则通过振动分析、红外热成像技术监测温升异常和润滑状态,必要时解体检查滚子磨损与保持架变形。
3. 悬挂系统性能测试
包括一系、二系悬挂装置的弹簧刚度、减振器阻尼特性检测。使用液压试验台模拟载荷变化,验证弹簧疲劳强度;通过动态位移传感器记录减振器衰减曲线,判断其是否满足设计要求。
4. 制动装置功能性验证
制动梁、闸瓦托及制动杠杆需检查裂纹与变形,重点采用涡流检测(ET)快速筛查表面缺陷。同时测试制动缸行程、闸瓦间隙及制动响应时间,确保制动力均匀分配且动作灵敏。
5. 紧固件与连接部件检查
所有螺栓、销轴及开口销需逐一确认紧固扭矩和防松标记状态,使用扭矩扳手复测关键连接点。对齿轮箱悬挂螺栓、电机吊杆等高速振动区域的部件,应用相控阵超声检测(PAUT)评估内部损伤风险。
检测技术创新与发展趋势
随着智能运维技术的普及,转向架检测逐步向自动化、数字化方向升级。例如,车载健康监测系统(HMS)可实时采集振动、温度数据;机器人视觉检测平台能高效完成轮对表面缺陷识别;大数据分析则帮助预测部件剩余寿命,推动检测模式从“定期修”向“状态修”转型。
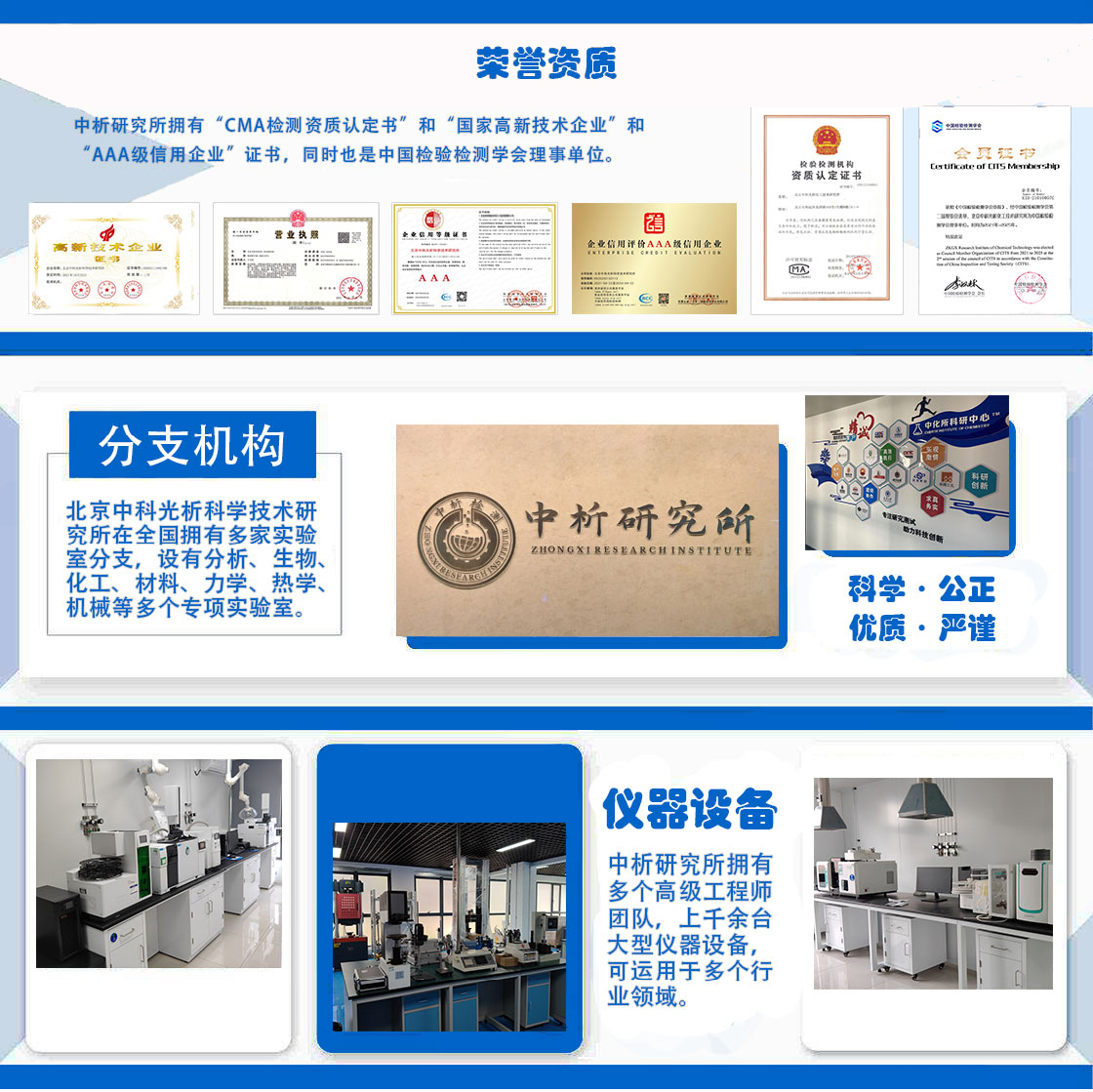
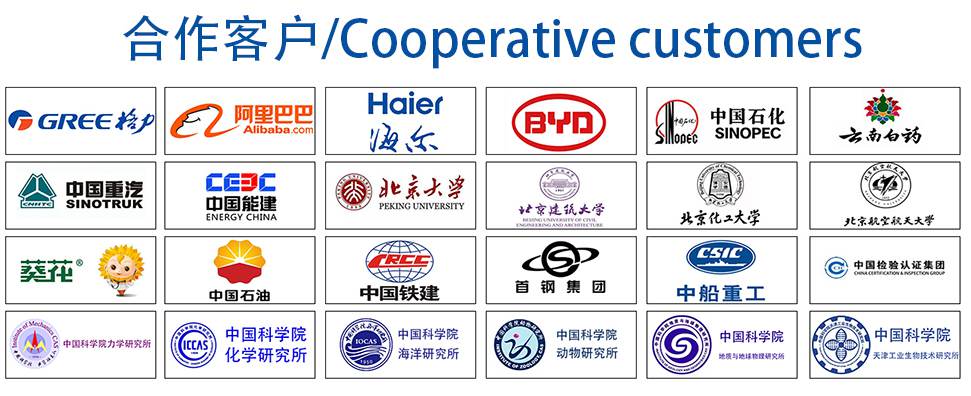