蒸压釜检测的重要性与必要性
蒸压釜是一种广泛应用于建材、化工、冶金等行业的高压容器设备,主要用于蒸压加气混凝土制品、硅酸盐制品等材料的成型固化。其工作环境长期处于高温、高压状态,设备材质易受腐蚀、疲劳及应力集中等因素影响,若缺乏定期检测与维护,可能导致泄漏、爆炸等严重安全事故。根据《固定式压力容器安全技术监察规程》(TSG 21-2016)要求,蒸压釜必须进行定期检测,以确保其安全运行。检测不仅是对设备性能的全面评估,更是保障生产安全、降低企业风险的核心手段。
蒸压釜检测的主要项目
1. 外部宏观检查
通过目视或辅助工具对蒸压釜本体、法兰、焊缝、密封面等部位进行外观检查,重点观察是否存在变形、裂纹、腐蚀、鼓包等缺陷。同时检查保温层、支吊架等附属设施的完整性,确保设备整体结构稳定。
2. 安全附件及仪表的校验
包括安全阀、压力表、温度计、爆破片等安全附件的性能测试: - 安全阀:校验开启压力及回座压力是否符合标准; - 压力表:检查量程、精度及指针灵敏度; - 温度监测装置:验证其显示准确性与响应速度; - 联锁保护系统:测试超压、超温报警及自动泄压功能是否有效。
3. 壁厚测定与腐蚀评估
利用超声波测厚仪对釜体、封头等关键部位进行多点厚度测量,对比设计厚度评估腐蚀减薄程度。若局部减薄超过标准允许值,需进行强度校核或修复处理。
4. 无损检测(NDT)
采用磁粉检测(MT)、渗透检测(PT)或射线检测(RT)等方法,对焊缝、开孔周围及应力集中区域进行探伤,排查表面及近表面裂纹、气孔等缺陷。对可疑区域进行复检,并记录缺陷的位置、尺寸及性质。
5. 耐压试验与密封性试验
在检测周期内,需进行水压试验或气压试验,验证釜体在1.25倍设计压力下的强度和密封性。试验中需监控压力变化,检查是否存在渗漏或异常变形,确保设备承压能力符合安全标准。
6. 材料理化性能分析
对釜体材料(如Q345R钢板)取样进行金相分析、硬度测试及化学成分检测,评估材料是否因长期高温环境发生劣化,如晶间腐蚀、脱碳等现象。
7. 自动化控制系统检查
验证蒸压釜的压力、温度、时间等工艺参数的自动控制逻辑,确保程序运行稳定,避免因控制失效导致超压或超温事故。
检测周期与标准依据
蒸压釜的全面检验周期一般为3年,首次检验需在投入使用后1年内完成。检测过程需严格遵循TSG 21-2016、GB/T 16508-2013《锅壳锅炉》及NB/T 47013-2015《承压设备无损检测》等标准,确保检测结果的权威性和可靠性。
结语
蒸压釜作为高风险特种设备,其检测需由具备资质的第三方机构实施,并形成完整的检测报告与整改方案。企业应建立设备档案,定期跟踪隐患整改情况,从源头杜绝安全事故,实现生产安全与效益的双重保障。
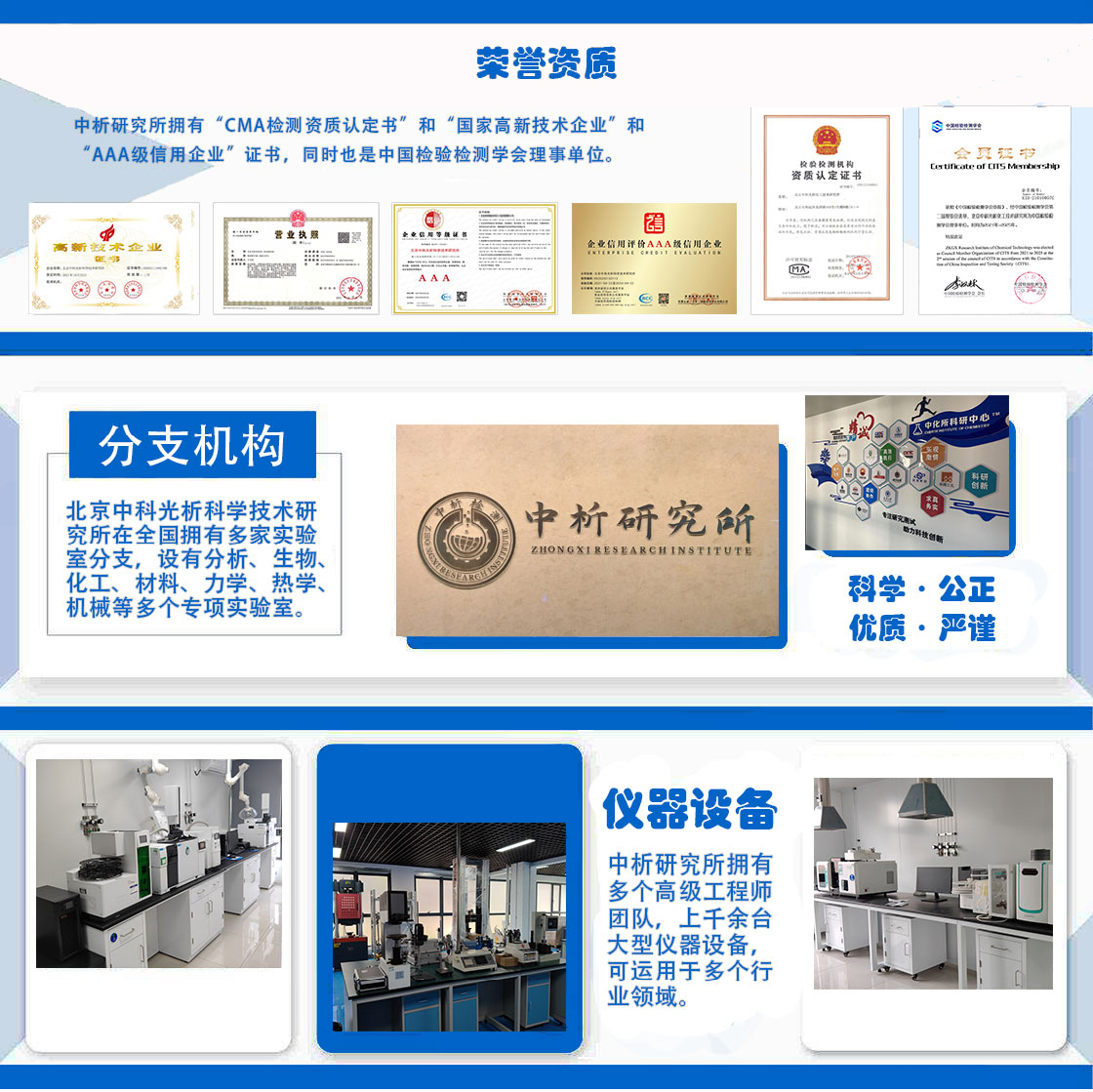
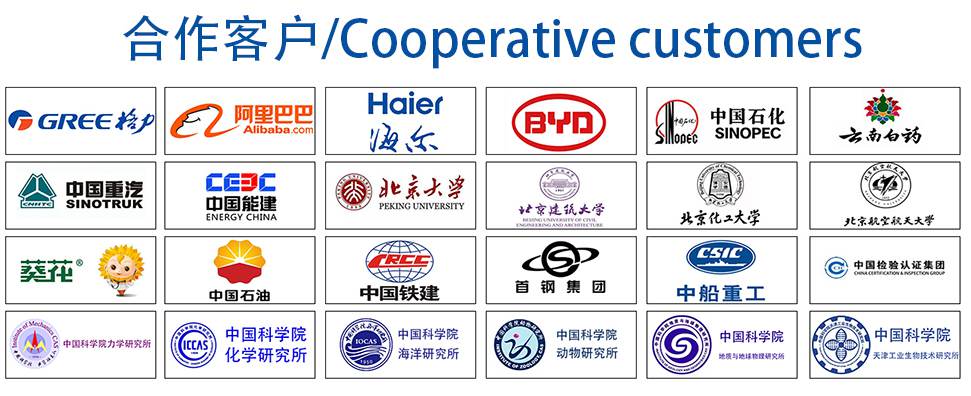