水泥工业用回转窑检测技术与关键项目解析
作为水泥生产核心设备,回转窑的稳定运行直接关系到产品质量、能源消耗及企业经济效益。其长期处于高温、重载、腐蚀的恶劣工况中,易出现筒体变形、耐火材料脱落、支撑装置磨损等典型问题。针对水泥工业用回转窑建立系统化检测体系,可精准识别设备隐患,实现预测性维护,有效降低非计划停机风险。根据GB/T 32994-2016《水泥工业用回转窑》等行业标准,检测项目需覆盖机械性能、热工参数及安全指标三大维度。
一、筒体几何尺寸与结构完整性检测
采用激光测距仪与经纬仪进行筒体椭圆度测量,重点检测轮带支承区段的径向变形量,行业标准要求椭圆度偏差不超过0.15%D(D为筒体直径)。通过超声波探伤(UT)检测环向焊缝质量,磁粉检测(MT)排查筒体表面裂纹,尤其是温度交变频繁区域的应力裂纹。筒体直线度检测使用全站仪测量轴向偏差,确保每段筒体中心线偏移量≤5mm/m。
二、耐火材料状态评估
运用红外测温仪扫描窑衬表面温度分布,异常高温区域提示耐火砖脱落风险。通过敲击法结合声波分析系统,检测窑皮附着状态与材料空隙率。定期测量窑口、烧成带等关键部位耐火材料残余厚度,使用专用测厚仪确保数据精度,当厚度低于设计值60%时需计划更换。
三、支撑装置运行监测
检测托轮与轮带接触面磨损量,使用卡尺测量凹槽深度,磨损超过原始尺寸10%需修复。采用振动分析仪检测托轮轴承异常振动频率,轴承温度监控应设置双重报警阈值(通常一级报警85℃,二级报警95℃)。测量轮带间隙时需在冷态和热态分别记录数据,间隙变化超过3mm需调整垫板。
四、传动系统动态检测
使用激光对中仪确保齿轮副啮合精度,齿侧间隙控制在0.25-0.35mm范围内。大齿圈径向跳动检测采用百分表多点测量法,跳动量不应超过1.5mm/m。减速机振动值监测需符合ISO10816-3标准,同时对润滑油进行铁谱分析,检测齿轮磨损颗粒浓度。
五、密封装置性能验证
采用负压检测法评估窑头/窑尾密封效果,漏风率需控制在1.5%以下。检查鱼鳞片密封的磨损补偿能力,弹簧压力应保持均匀分布。使用热成像仪检测密封区域温度分布,异常热点可能预示密封失效或冷风侵入。
六、热工系统配套检测
燃烧器定位精度检测需保证中心线偏差<3mm,火焰形状通过工业内窥镜进行可视化检查。三次风管耐磨衬里厚度测量需结合停机检测与在线监测数据,旋风筒压力损失检测需比对设计参数,压差上升15%提示系统阻力异常。
七、智能化监测系统建设
现代回转窑检测正朝着智能化方向发展,通过安装无线应变传感器网络实时监测筒体应力分布,结合DCS系统建立热机械耦合模型。基于大数据分析的预测性维护平台可提前40天预警主要部件故障,检测周期从传统每月1次延长至季度巡检+实时监测模式。
通过上述系统性检测项目的实施,企业可建立回转窑全生命周期健康档案,检测数据与生产参数的交叉分析能有效提升设备管理水平。据统计,严格执行检测标准可使回转窑运转率提高至92%以上,吨熟料维修成本降低35%,为水泥企业创造显著的经济效益与安全保障。
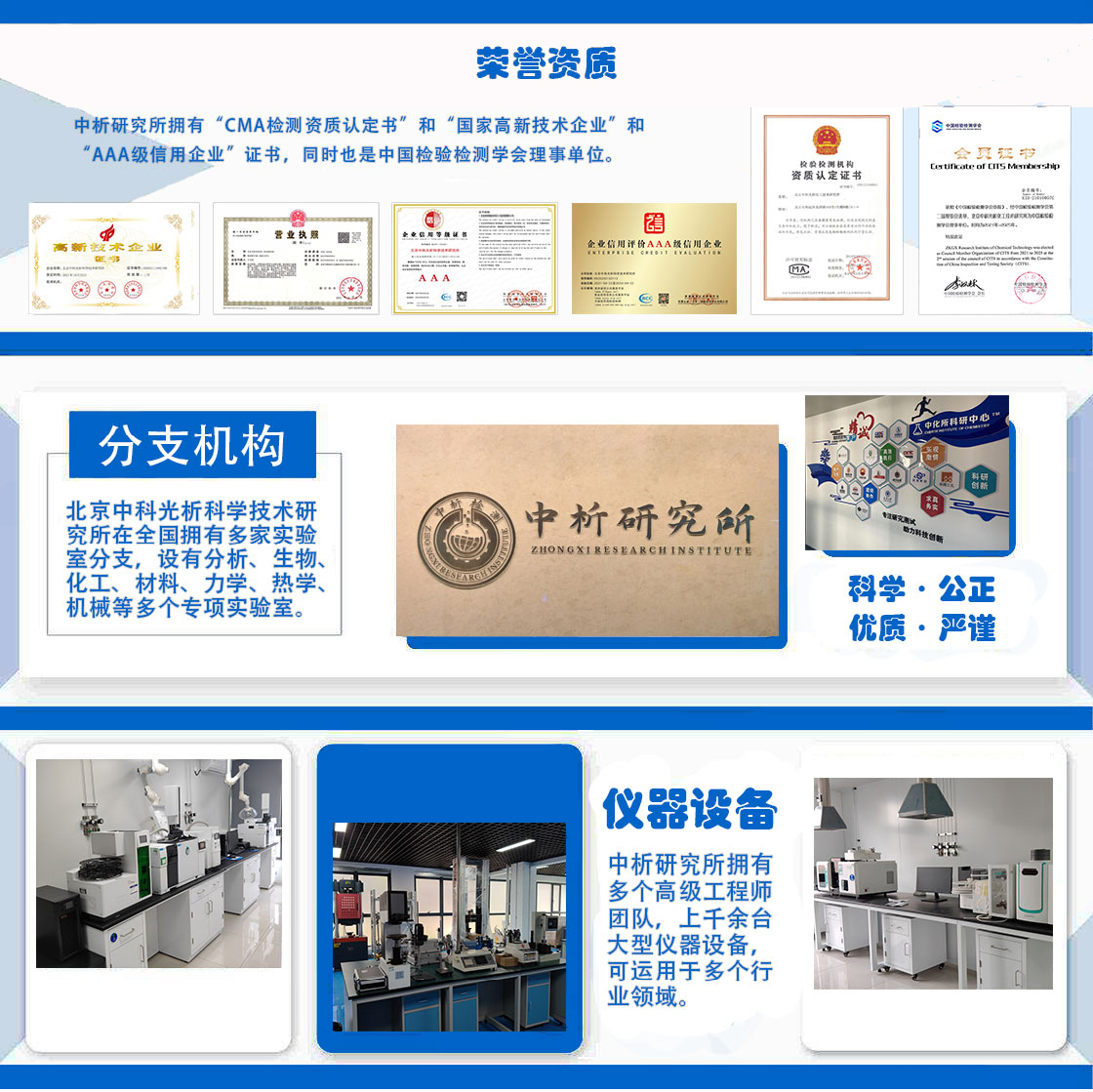
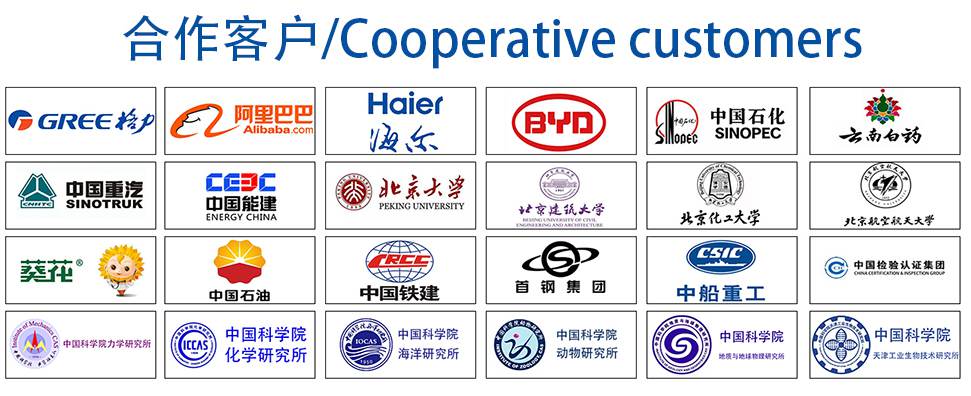