凿岩机械与气动工具用镁合金铸件通用技术条件检测解析
镁合金因其轻量化、高比强度、优异减震性及良好的铸造性能,在凿岩机械与气动工具领域得到广泛应用。然而,镁合金铸件在生产过程中易出现气孔、缩松、夹杂等缺陷,直接影响设备的可靠性、安全性和使用寿命。为确保产品质量符合行业标准(如GB/T 25745-2010《镁合金铸件》及相关行业规范),需通过系统性检测验证其技术条件。检测内容需覆盖材料性能、几何精度、表面质量和功能性指标,形成对铸件质量的全方位评价。
核心检测项目分类与要求
1. 化学成分分析
采用光谱分析法(如直读光谱仪)或化学滴定法,检测镁合金中主元素(Mg)及添加元素(Al、Zn、Mn等)含量是否符合牌号要求。需重点关注杂质元素(Fe、Cu、Ni等)的限量控制,避免因杂质超标导致耐蚀性下降。
2. 机械性能测试
通过万能试验机开展拉伸试验,测定抗拉强度(≥160MPa)、屈服强度(≥90MPa)和延伸率(≥3%)。配套布氏/洛氏硬度计测定硬度值(HB 50-90),冲击试验机验证低温环境下的冲击韧性(≥5J/cm²)。试样需取自铸件本体或同炉附铸试块。
3. 尺寸与几何公差检测
使用三坐标测量机、轮廓投影仪等设备,检测关键配合尺寸(孔径、轴径、安装面间距等)精度是否符合IT10-IT12级公差要求。同时验证平面度(≤0.1mm/100mm)、圆度(≤0.05mm)等形位公差,确保装配兼容性。
4. 表面质量检查
目视检查结合粗糙度仪,确认表面无裂纹、冷隔、粘砂等缺陷。铸造表面粗糙度Ra值需≤12.5μm,机加工面Ra≤6.3μm。特殊工况部件需进行荧光渗透检测(FPI)或磁粉探伤(MT),识别微米级表面缺陷。
5. 无损检测(NDT)
采用X射线实时成像系统或超声波探伤仪,检测铸件内部缺陷。气孔直径需≤1mm且间距≥3mm,单个缩松面积不超过3mm²,总缺陷面积占比应<2%。对承受交变载荷的部件(如冲击活塞),需执行100%射线检测。
6. 耐腐蚀性验证
通过中性盐雾试验(NSS)评估防护涂层性能,未涂层铸件需满足48小时无红锈要求。对含Cl⁻环境使用的铸件,应增加循环腐蚀试验(CCT),模拟实际工况下的腐蚀速率和氧化膜稳定性。
检测流程标准化建议
建议按照"来料初检→过程抽检→终检全测"的三阶管控模式,结合统计过程控制(SPC)技术建立质量数据库。对于批量生产件,抽样方案应执行GB/T 2828.1-2012标准,AQL值按关键/重要/一般特性分级设置为0.65/1.0/2.5。检测报告需包含原始数据、检测图谱及符合性,实现质量追溯的完整闭环。
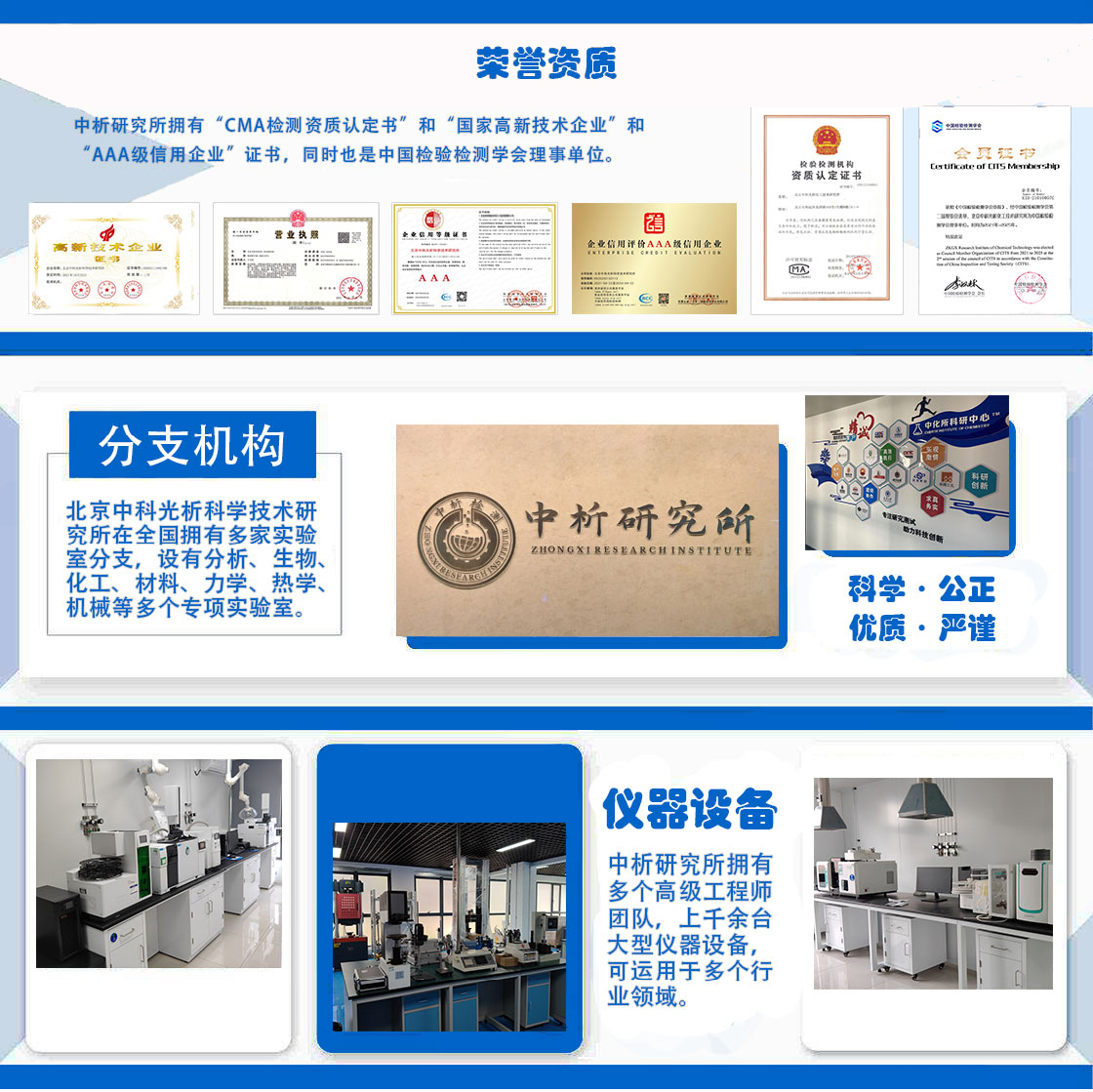
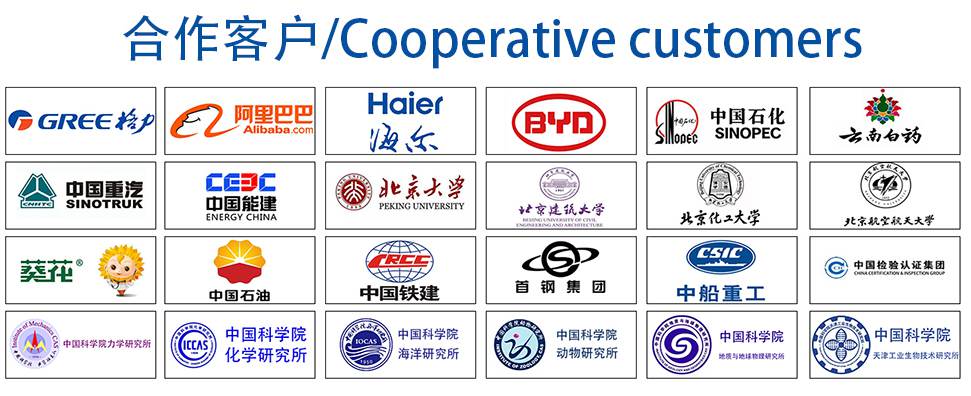