变形镁合金检测的重要性与应用领域
变形镁合金作为轻量化材料的代表,在航空航天、汽车制造、3C电子产品等领域广泛应用。其优异的比强度、减震性能和可加工性使其成为替代传统金属的理想选择。然而,镁合金的化学活性高、易腐蚀、成型工艺复杂等特点,使得材料性能的稳定性面临挑战。因此,系统化的检测项目是确保变形镁合金产品质量、优化生产工艺的核心环节。通过科学的检测手段,不仅能验证材料是否符合设计指标,还可为后续应用场景的可靠性提供数据支撑。
核心检测项目及方法
1. 化学成分分析
采用电感耦合等离子体发射光谱(ICP-OES)或X射线荧光光谱(XRF)对镁基体中铝、锌、锰等合金元素含量进行定量分析,同时检测铁、镍、铜等杂质元素的限量是否符合GB/T 5153或ASTM B93标准。精准的成分配比直接影响材料强度、耐蚀性及加工性能。
2. 力学性能测试
通过万能材料试验机开展拉伸试验(测定抗拉强度、屈服强度、延伸率)、硬度测试(布氏/维氏硬度)及压缩试验。针对不同变形工艺(轧制、挤压、锻造)的镁合金,需结合ASTM E8/E9标准评估各向异性特征,确保力学性能满足部件服役需求。
3. 显微组织观察
利用金相显微镜和扫描电镜(SEM)分析晶粒尺寸、第二相分布及动态再结晶程度。通过EBSD技术表征织构演变,结合XRD检测相组成,评估热处理工艺对材料微观结构的影响,为优化加工参数提供依据。
4. 腐蚀性能评估
执行盐雾试验(ASTM B117)、电化学阻抗谱(EIS)和动电位极化曲线测试,量化材料在典型环境中的耐蚀性。针对表面处理(阳极氧化、微弧氧化)样品,需额外检测涂层厚度、孔隙率及结合强度。
5. 成型性能检测
通过杯突试验、弯曲试验和高温拉伸试验评价材料的成形极限图(FLD),结合数值模拟分析其在冲压、旋压等变形过程中的开裂倾向,为复杂构件成型工艺开发提供关键数据。
6. 无损检测技术
采用超声波探伤(UT)检测内部缺陷,涡流检测(ET)筛查表面裂纹,工业CT扫描分析三维孔隙分布。结合ASTM E2375标准建立缺陷评级体系,确保关键承力部件的结构完整性。
检测技术发展趋势
随着原位检测、机器学习算法的应用,变形镁合金检测正向智能化、高精度方向发展。多尺度表征技术与服役性能预测模型的结合,将进一步提升检测效率并降低研发成本,推动镁合金在新能源、生物医疗等新兴领域的应用突破。
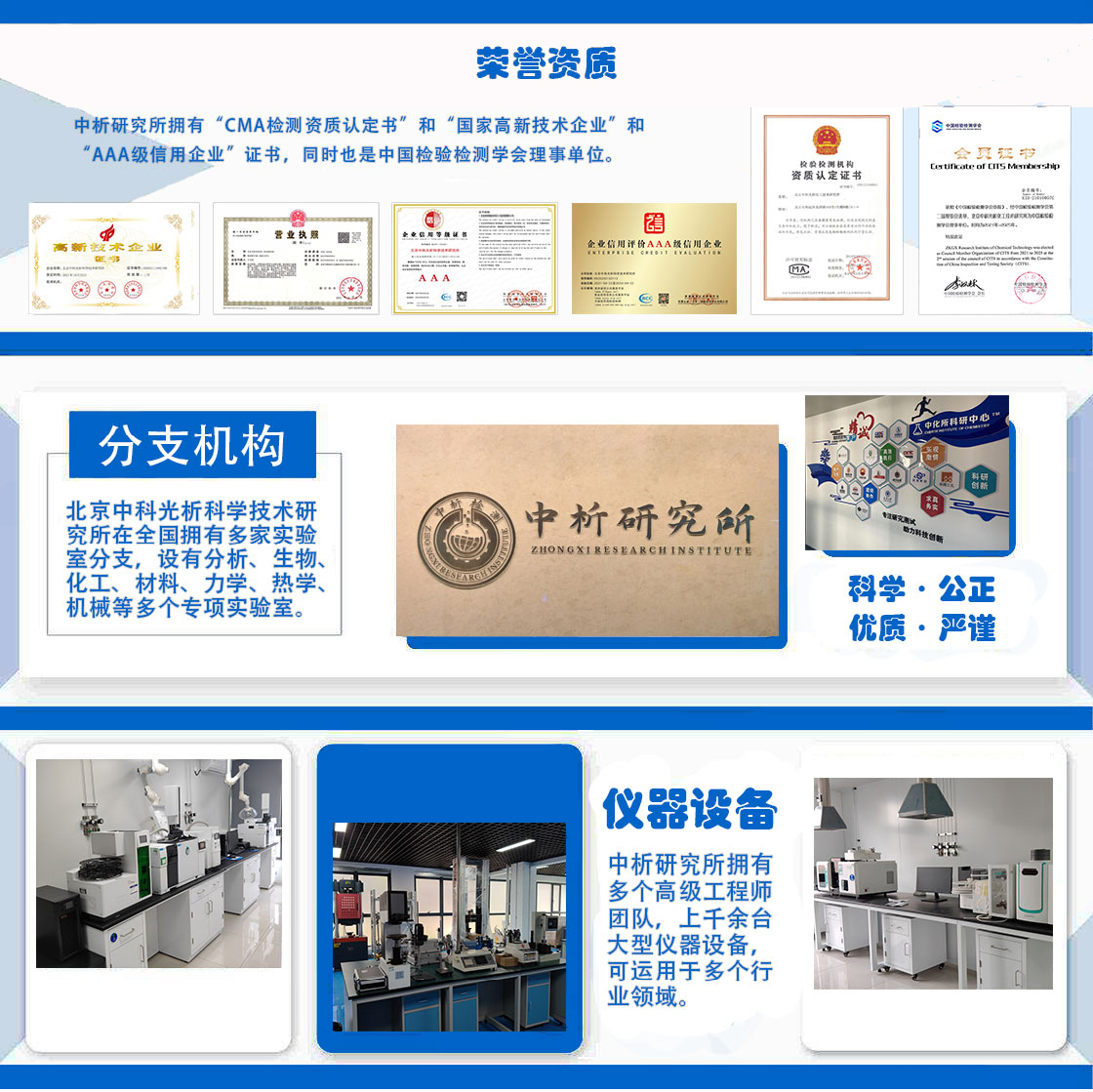
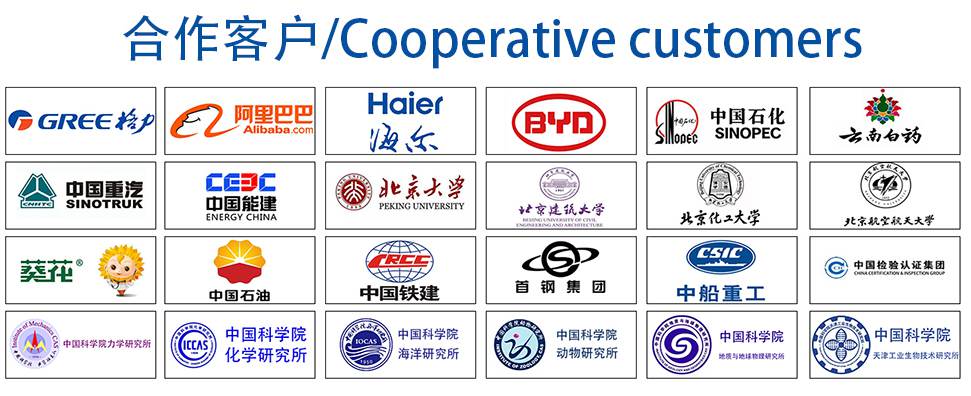