镁合金作为21世纪最具发展潜力的轻量化金属材料,因其密度低、比强度高、电磁屏蔽性能优异等特点,在航空航天、轨道交通、3C电子等领域获得广泛应用。热挤压成型工艺通过高温高压使镁合金材料产生塑性变形,可制备复杂截面型材并改善材料机械性能。但受镁合金室温塑性差、挤压工艺窗口窄等因素影响,型材在成型过程中易出现裂纹、褶皱、尺寸偏差等缺陷,严格的检测体系成为确保产品质量的关键环节。
一、化学成分检测
采用直读光谱仪对镁合金主元素(Mg、Al、Zn、Mn等)和杂质元素(Fe、Ni、Cu等)进行定量分析,确保合金成分符合GB/T 5153或ASTM B107标准要求。重点监控铁含量(<0.005%)和镍含量(<0.002%)等易引发晶间腐蚀的有害元素,通过电感耦合等离子体发射光谱仪(ICP-OES)进行二次验证。
二、力学性能测试
依据GB/T 228.1标准开展室温拉伸试验,检测抗拉强度(≥220MPa)、屈服强度(≥110MPa)和延伸率(≥8%)。使用布氏硬度计(载荷187.5kgf)检测型材表面及截面硬度(HBW 55-75)。对承受动态载荷的型材需增加冲击韧性试验,采用夏比V型缺口试样进行检测。
三、尺寸与形位公差检测
运用三坐标测量仪(CMM)进行全尺寸检测,包括型材截面轮廓度(±0.15mm)、直线度(≤0.5mm/m)、平面度(≤0.3mm)等关键参数。对具有装配功能的导轨、卡槽等特征部位,使用专用通止规进行配合间隙检测。根据GB/T 14846标准评估整体尺寸合格率。
四、表面质量检测
通过目视检测和20倍放大镜观察表面裂纹、起皮、气泡等缺陷,每米长度内允许存在≤3个直径<0.5mm的点状缺陷。采用便携式粗糙度仪测量表面Ra值(≤3.2μm),使用涡流探伤仪检测皮下夹杂物。对阳极氧化处理的型材需额外进行膜厚测试(8-15μm)和色差分析。
五、金相组织分析
制备纵向/横向金相试样,通过光学显微镜观察晶粒形貌(平均晶粒尺寸≤50μm)和第二相分布。使用扫描电镜(SEM)分析β-Mg17Al12相的形态与占比(5-15%)。通过X射线衍射(XRD)检测织构强度,评估挤压工艺对材料各向异性的影响。
六、耐腐蚀性能测试
执行中性盐雾试验(GB/T 10125),在5%NaCl溶液中连续喷雾96小时后,单位面积质量损失应≤0.8mg/cm²。采用电化学工作站测量自腐蚀电位(>-1.5V)和腐蚀电流密度(<5μA/cm²)。对表面处理试样还需进行CASS铜加速盐雾试验。
七、无损检测
采用超声波探伤(UT)检测内部裂纹和分层缺陷,要求回波幅度不超过DAC曲线的50%。对复杂截面型材使用工业CT进行三维缺陷重构,空间分辨率达到0.05mm。荧光渗透检测(PT)用于发现表面开口缺陷,显示痕迹长度应<1.6mm。
通过建立涵盖原料、工艺、成品的全流程检测体系,采用数字化检测设备与智能化数据分析技术,可有效提升镁合金挤压型材的质量稳定性。当前检测技术正朝着在线实时监测、人工智能缺陷识别方向发展,为镁合金在新能源汽车电池包结构件等高端领域的应用提供可靠保障。
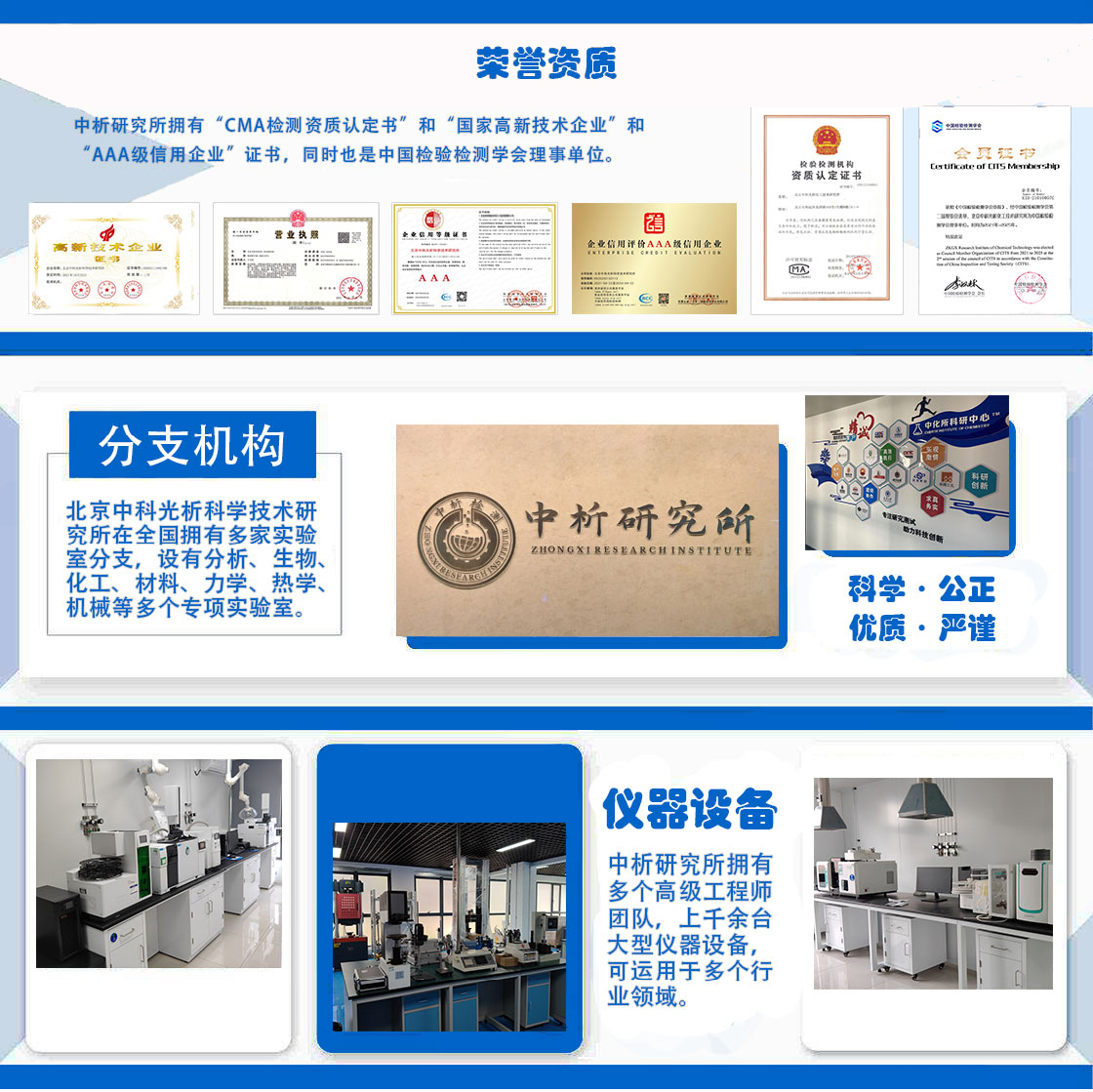
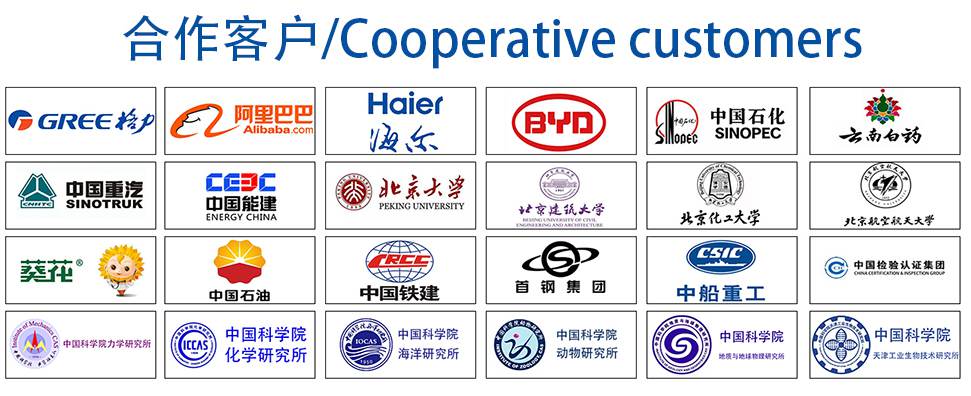