镁合金牺牲阳极检测技术要点解析
镁合金牺牲阳极作为阴极保护系统的核心材料,在油气管道、船舶防腐、储罐防护等领域发挥重要作用。其通过比被保护金属更负的电位特性持续释放电流,延缓金属结构的电化学腐蚀。为保障阳极性能达标,需依据GB/T 17731-2020《镁合金牺牲阳极》及ASTM B843标准建立完整的检测体系,涵盖化学成分、电化学参数、物理特性等6大核心检测维度。
一、化学成分分析
采用ICP-OES光谱法测定镁(Mg)、铝(Al)、锌(Zn)、锰(Mn)等主量元素含量,要求主成分镁含量≥99.5%,铝控制在5.0-7.0%,锌0.2-0.8%。同时使用火花直读光谱仪检测铁(Fe≤0.03%)、铜(Cu≤0.02%)、硅(Si≤0.10%)等杂质元素,确保晶间腐蚀敏感性符合标准。
二、电化学性能测试
通过恒电流法测定开路电位(需≤-1.55V vs.CSE)、电流效率(≥55%)及实际电容量(≥1230A·h/kg)。采用三电极体系在模拟海水介质中进行极化曲线测试,要求阳极极化率≤0.05mV/mA·cm²,确保电流输出稳定性。
三、金相组织检测
制备阳极横纵截面试样,使用金相显微镜观察α-Mg基体与β-Mg17Al12相的分布均匀性。通过Image Pro Plus软件分析第二相占比(5-8%为佳),晶粒度控制在50-100μm范围,避免粗大晶粒导致局部腐蚀加剧。
四、尺寸与表面质量检测
使用激光三维扫描仪校验阳极截面尺寸偏差(±1.5mm),质量公差控制在±2%。表面缺陷检测采用工业内窥镜与磁粉探伤相结合,要求裂纹深度<0.5mm,铸造气孔直径<1mm且单位面积不超过3个。
五、腐蚀速率测试
采用失重法在3.5% NaCl溶液中测试72小时,腐蚀速率应维持在2.5-3.8mm/年区间。同步进行盐雾试验(ASTM B117),2000小时试验后表面腐蚀产物应呈均匀层状分布,无局部剥落现象。
六、环境适应性检测
针对不同应用场景开展专项测试:海底阳极需进行20MPa静水压力测试,土壤用阳极检测-20℃低温脆性,高温环境阳极需考核150℃下电流效率衰减率(<15%)。所有测试数据需通过Weibull分布进行可靠性评估。
通过上述系统性检测,可确保镁合金牺牲阳极具备稳定的电化学活性、均匀的溶解特性以及长效的防护寿命。建议生产企业建立全流程质量追溯体系,特别是在熔炼工艺控制和铸造成型环节实施SPC过程控制,从源头上提升阳极产品合格率。
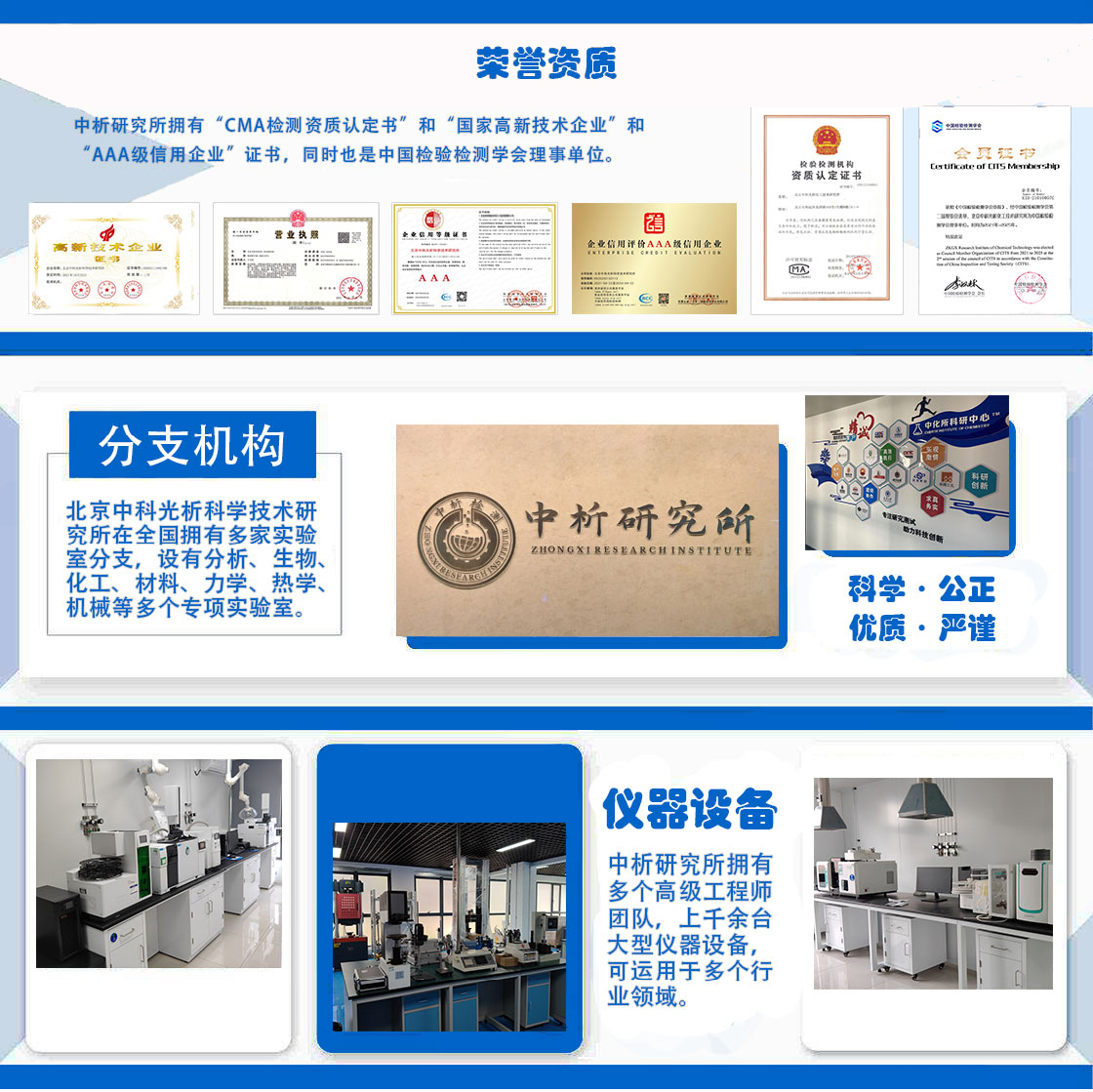
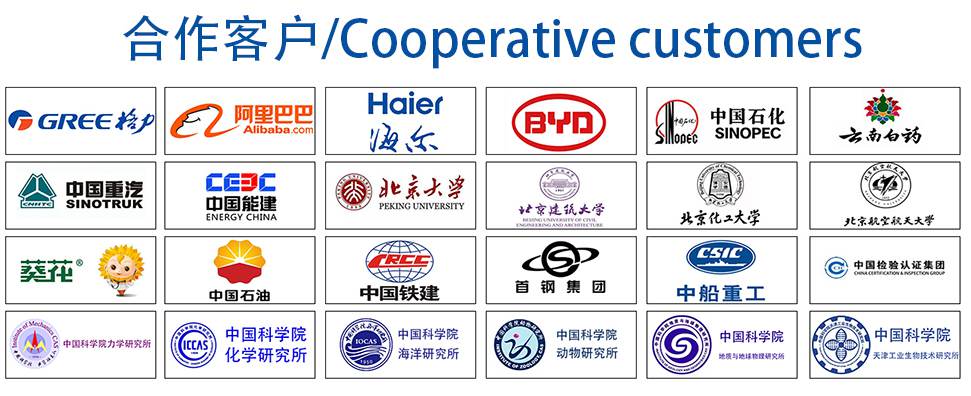