电冰箱用全封闭型电动机-压缩机检测的重要性
全封闭型电动机-压缩机是电冰箱的核心部件,其性能直接影响制冷效率、能耗水平和设备寿命。由于压缩机长期处于高压、高温及频繁启停的工作环境中,任何设计缺陷或制造误差都可能导致系统故障甚至安全隐患。因此,针对其开展全面、精准的检测至关重要。检测不仅可验证产品是否符合国家标准(如GB/T 9098-2021),还能确保压缩机的可靠性、能效比和环保性,从而提升整机制造商的市场竞争力。近年来,随着行业对节能环保要求的提高,检测技术也在不断升级,覆盖电气性能、机械强度、密封性等多个维度。
核心检测项目及方法
1. 电气性能测试
包括绝缘电阻测试、耐压试验和启动性能检测。通过高阻计测量绕组与外壳间的绝缘电阻(通常要求≥100MΩ),并施加2500V交流电压1分钟验证耐压能力。启动测试需模拟低电压(85%额定电压)条件下压缩机的启动成功率,确保其在电网波动时的稳定性。
2. 机械性能测试
重点评估压缩机运行时的振动、噪声和温升。使用振动传感器测量不同负载下的振幅(一般要求≤0.3mm),并通过分贝仪检测运行噪声(标准值≤45dB(A))。温升试验需连续运行4小时后,测量电机绕组温度(限值≤125℃),避免过热导致材料劣化。
3. 密封性检测
采用氦质谱检漏法或浸水法对压缩机壳体及焊缝进行气密性检查,确保制冷剂泄漏量≤0.5g/年。对于R600a等易燃制冷剂机型,密封性要求更为严格,需通过正负压交替试验验证长期可靠性。
4. 制冷效率与能效测试
在标准工况下(蒸发温度-23.3℃,冷凝温度54.4℃),测量制冷量、输入功率及能效比(COP)。通过热平衡法或第二制冷剂量热器法获取精确数据,确保COP值达到国家标准(如定频机≥1.75,变频机≥2.10)。
5. 耐久性试验
模拟极端使用场景,进行10万次启停循环测试和累计2000小时连续运行试验。记录关键参数变化趋势,分析轴承磨损、润滑油碳化等潜在问题,评估压缩机的设计寿命是否满足10年以上的行业要求。
6. 安全保护功能验证
测试过载保护器、热继电器的动作精度和复位特性。例如,在电流超过额定值120%时,保护装置应在规定时间内切断电源;温度保护需在壳体温度达到安全阈值(如130℃)时触发停机,防止恶性故障发生。
检测技术的发展趋势
随着智能化检测设备的普及,高精度传感器、AI数据分析技术正逐步应用于压缩机检测领域。例如,通过振动频谱分析预测轴承寿命,或利用红外热成像实时监测温度场分布。未来,检测系统将向自动化、数字化方向发展,结合物联网技术实现远程监控和预测性维护,进一步提升产品质量控制效率。
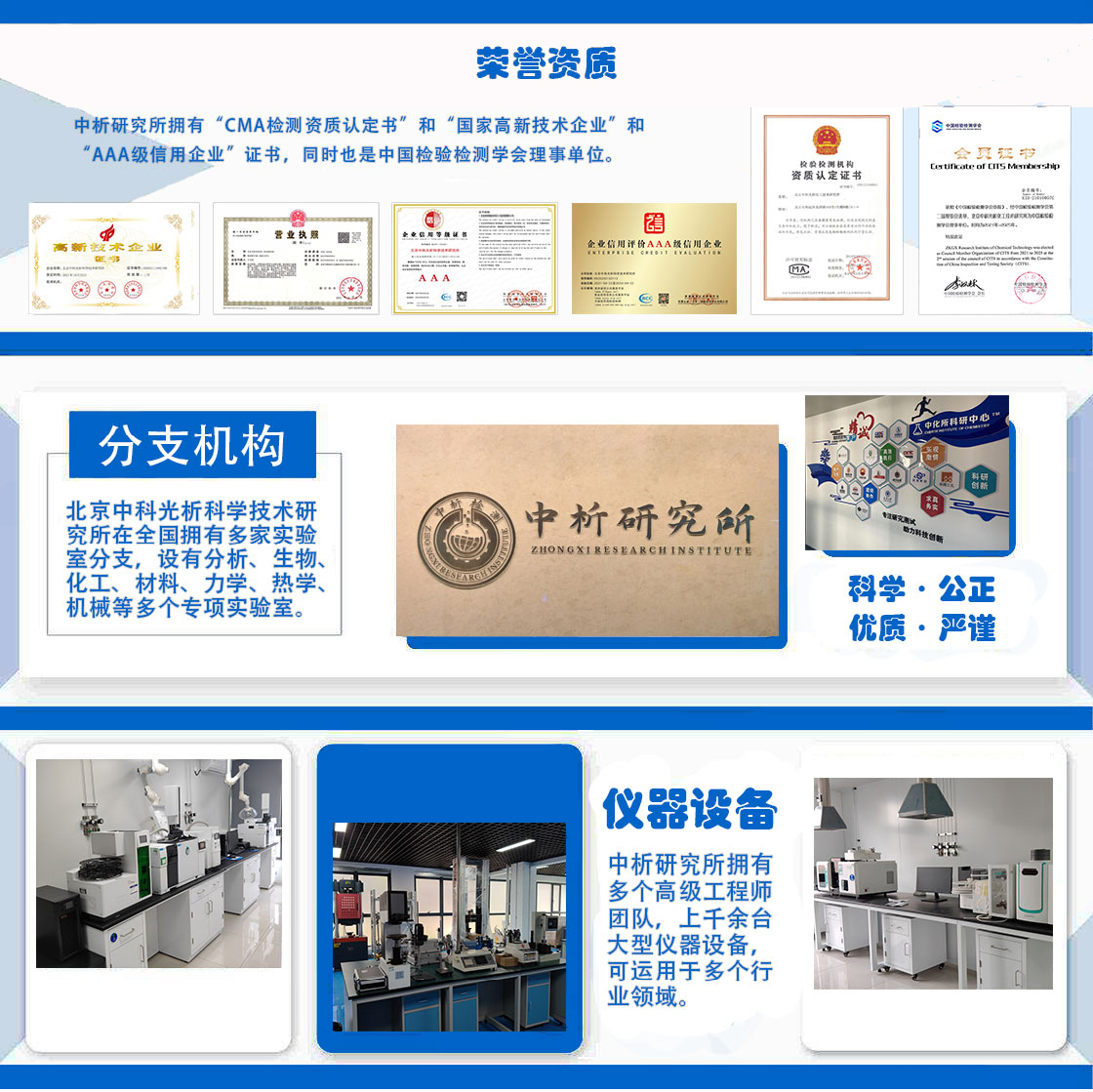
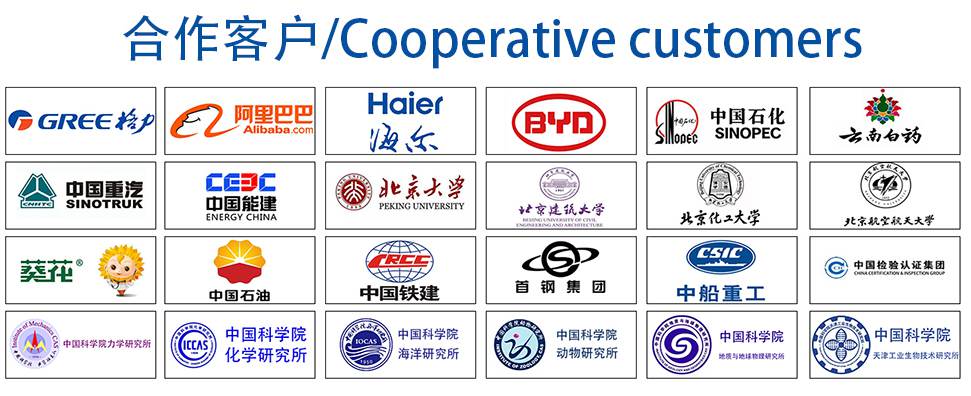