半导体制冷器具检测的重要性与应用场景
半导体制冷器具作为新型制冷技术的代表,凭借其无压缩机、体积小、低噪音等优势,在车载冰箱、医疗冷柜、实验室设备等领域得到广泛应用。然而,其性能稳定性、能效比及安全性高度依赖半导体材料和热电模块的质量。因此,系统性检测成为保障产品合规性和用户体验的核心环节。通过科学检测可验证制冷效率、温控精度、耐久性等关键指标,同时规避漏电、过热等安全隐患,为企业优化设计和市场准入提供技术支撑。
核心检测项目与技术要求
1. 能效与制冷性能测试
通过高精度温度传感器和功率分析仪,在标准环境(如25℃±1℃)下测量器具的制冷温差、COP(性能系数)及输入功率。要求最大温差≥55℃(冷热端),COP值需符合GB/T 23133-2020标准,同时验证低电压启动能力和温控系统响应速度。
2. 电气安全检测
依据IEC 60335-2-89标准,执行耐压测试(1500V/60s不击穿)、接地电阻(≤0.1Ω)及泄漏电流(≤0.75mA)检测。重点排查模块焊接点绝缘性能和异常温升情况,要求温升不超过标准限值15K。
3. 结构耐久性验证
包含2000次以上开合寿命测试、振动测试(模拟车载环境3G加速度)以及72小时盐雾试验。需确保散热器与半导体制冷片接合面无明显形变,防护等级达到IP34以上要求。
4. 环境适应性评估
在-20℃至50℃宽温域范围内测试制冷效率衰减率,要求高温工况下制冷量下降不超过标称值30%。同时进行85%RH高湿环境连续运行测试,验证控制系统防结露能力。
5. 材料环保与EMC测试
依据RoHS指令检测重金属含量,重点监控制冷剂载体材料的VOC释放量。电磁兼容性需满足EN 55014标准,确保对车载电子设备无干扰。
检测流程与认证体系
完整检测需经过样品预处理(48小时老化)→基础性能测试→加速寿命试验→破坏性检测四阶段。通过 认证的实验室可颁发CE、FCC、CCC等市场准入证书,检测周期通常为15-25个工作日。企业应重点关注半导体模块与散热系统的匹配度检测,这是影响整机效率的关键因素。
行业发展趋势与检测技术创新
随着新型热电材料(如Bi2Te3基复合材料)的应用,检测设备正向多参数同步采集方向发展。红外热成像技术已实现制冷面温度场分布的实时分析,AI算法开始用于预测器件寿命衰减曲线。未来检测标准将强化对瞬态响应(<3秒温差建立)和能源之星能效等级的考核要求。
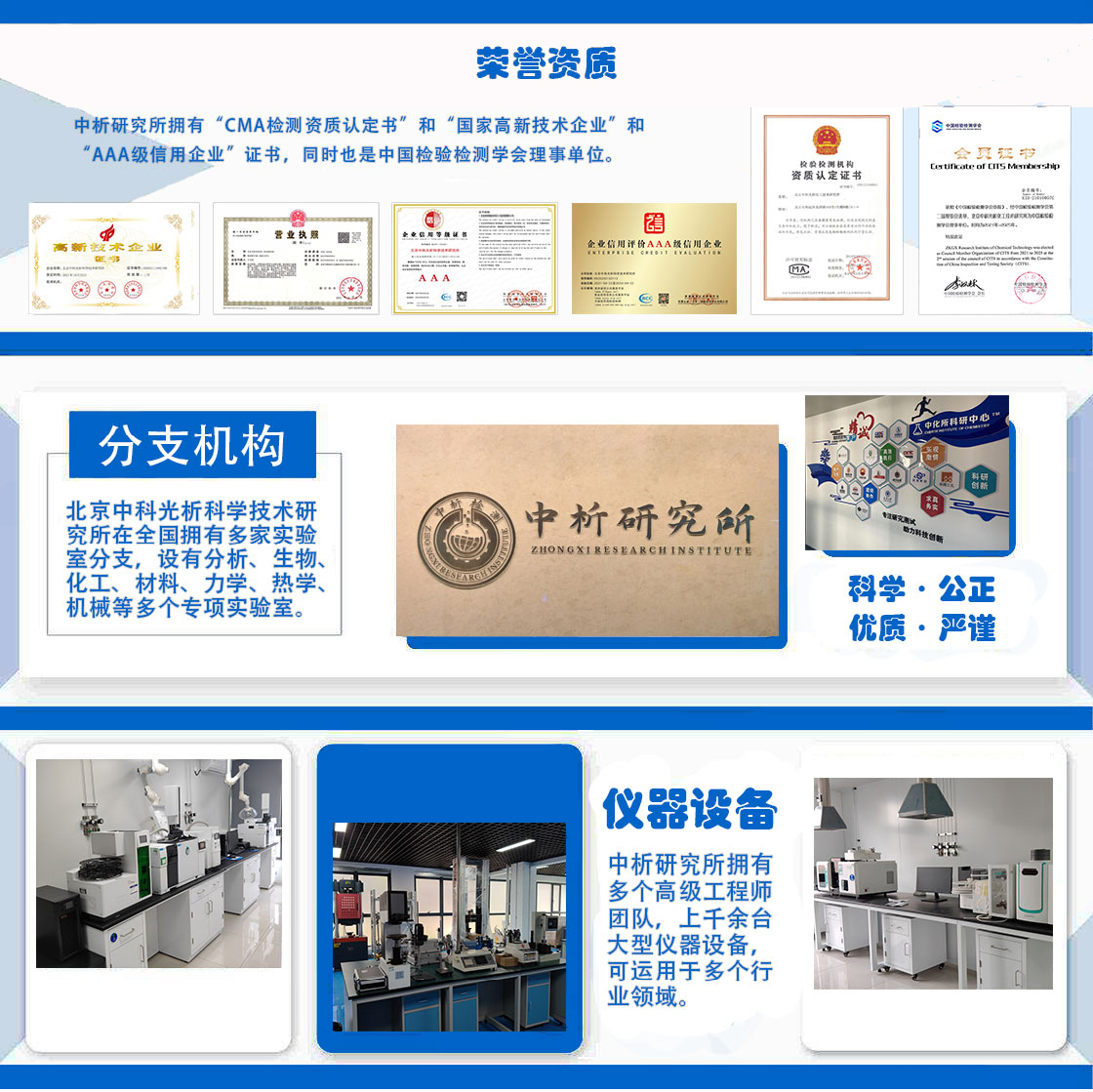
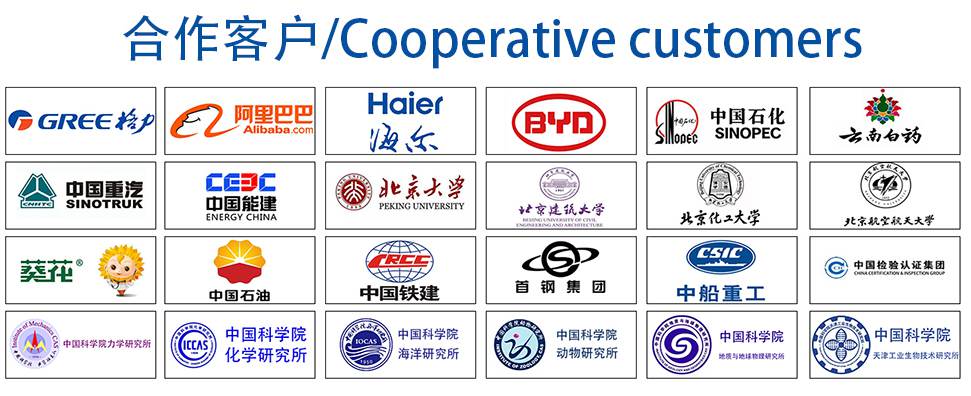