危险货物小型气体容器检测的重要性
危险货物小型气体容器广泛应用于医疗、消防、工业及日常生活领域,如便携式氧气瓶、灭火器、气雾罐等。由于其内部通常储存高压、易燃或有毒气体,一旦发生泄漏、爆炸或材料失效,可能引发严重的安全事故。因此,针对这类容器的检测显得尤为重要。各国法规(如《联合国关于危险货物运输的建议书》)及行业标准均对小型气体容器的设计、生产和运输提出了严格的技术要求,而定期检测则是确保其安全性的核心环节。
主要检测项目及技术要求
1. 压力测试与耐压性评估
通过水压试验或气压试验模拟极端工况,验证容器在额定压力下的结构完整性。检测需记录容器的形变量及是否存在裂纹、鼓包等缺陷,确保其能承受使用和运输中的压力波动。
2. 泄漏检测
采用氦质谱检漏法或浸水气泡法,对阀门、焊缝和密封接口进行高精度检查。根据标准(如GB/T 18443),泄漏率需控制在10⁻⁶ Pa·m³/s以下,以防止气体缓慢逸出导致安全隐患。
3. 材料化学分析与耐腐蚀性测试
通过光谱分析、金相检验等手段确认容器材质(如铝合金、复合材料)的合规性。同时进行盐雾试验或酸碱环境模拟,评估材料的抗腐蚀性能,避免因材料劣化引发强度下降。
4. 密封结构与阀门可靠性验证
检测密封圈的耐温性、弹性变形能力,并通过反复启闭阀门测试其操作的稳定性和气密性。对于可重复充装容器,还需验证快速接头的防误开设计是否符合规范。
5. 爆炸与冲击试验
针对可燃气体容器,需模拟高温、碰撞或跌落场景,验证防火防爆设计的有效性。例如,通过自由落体试验(高度通常≥1.5米)检验容器在意外冲击下的抗破裂能力。
6. 标识与包装检查
核查容器表面的危险类别标识、充装介质、生产日期等信息是否清晰完整。同时检查运输包装的缓冲性能及危险品标志,确保符合ADR、IMDG等国际运输规范。
检测流程与监管要求
检测需由具备CMA/ 资质的实验室执行,依据GB 13075、ISO 11513等标准进行全项目覆盖。定期检测周期通常为3-5年,高风险环境使用的容器需缩短检测间隔。检测报告须包含原始数据、缺陷分析及整改建议,监管部门可通过二维码或RFID技术实现全生命周期追溯。
总结
危险货物小型气体容器检测是一项系统性工程,需综合运用物理测试、化学分析和数字化监控技术。通过严格的检测流程,既能保障用户安全,也能避免因产品缺陷引发的法律风险,对维护公共安全及行业可持续发展具有重要意义。
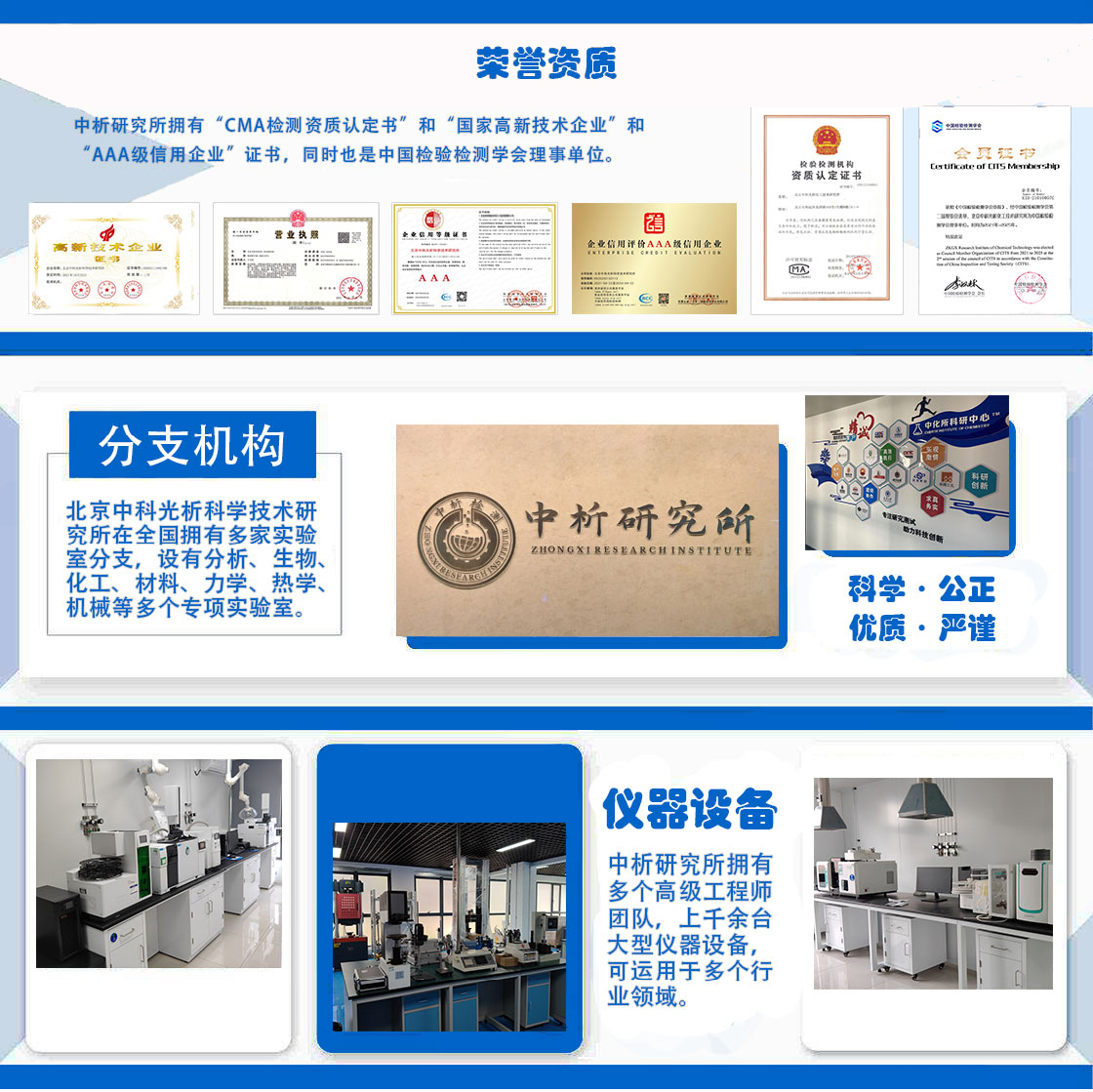
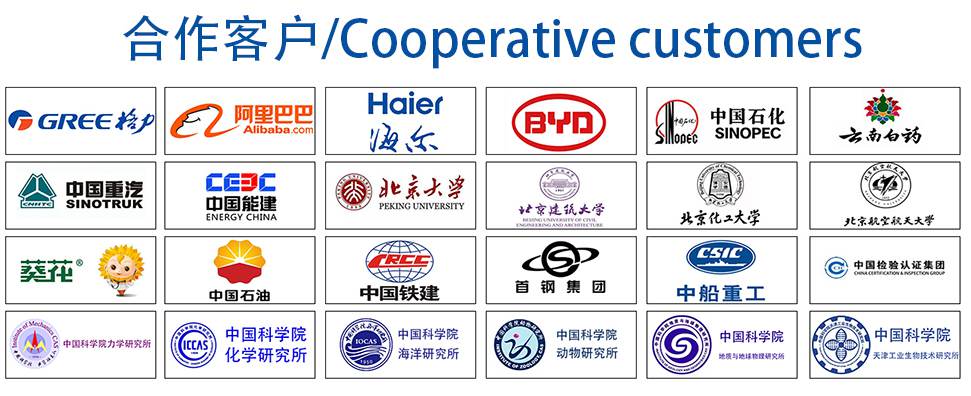