聚对苯二甲酸乙二醇酯(PET)瓶坯检测的重要性
聚对苯二甲酸乙二醇酯(PET)瓶坯作为食品、饮料、日化等行业广泛使用的包装容器基础材料,其质量直接影响最终成品的密封性、耐压性及安全性。随着对包装材料环保性、卫生性和耐用性要求的提高,PET瓶坯的检测已成为生产流程中不可或缺的环节。通过科学规范的检测,可以确保瓶坯在注塑成型、吹瓶加工及后续灌装过程中满足性能要求,避免因材料缺陷导致的渗漏、变形或化学污染等问题。
PET瓶坯核心检测项目
PET瓶坯的检测需覆盖物理性能、化学性能及卫生指标三大维度,具体包括以下关键项目:
1. 物理性能检测
壁厚均匀性:通过激光测厚仪或X射线检测设备,分析瓶坯各部位的壁厚分布,确保吹瓶后瓶体强度与耐压能力达标。
重量偏差:称重法检测单个瓶坯质量,控制批次内重量波动范围(通常要求±0.5g以内),避免生产能耗浪费和成品容量误差。
尺寸精度:利用三维测量仪验证瓶坯高度、螺纹直径等关键尺寸是否符合设计标准,确保与吹瓶模具的匹配性。
2. 化学性能检测
乙醛(AA)含量:气相色谱法测定瓶坯中乙醛残留量(一般要求≤4ppm),避免高温灌装时迁移影响饮品风味。
特性粘度(IV值):通过乌氏粘度计检测PET材料的分子链长度,控制IV值在0.70-0.85dL/g范围,保障吹瓶成型时的熔体强度。
残留催化剂检测:原子吸收光谱法测定锑(Sb)等催化剂的迁移量,确保符合FDA、EU等法规限值。
3. 卫生与安全指标
微生物限度:针对食品级瓶坯,需通过菌落总数、霉菌等微生物检测,确保无菌化生产环境达标。
重金属溶出:模拟酸性环境(如4%乙酸溶液)下的铅、镉等重金属溶出实验,验证是否符合GB 4806.7等食品安全标准。
紫外吸收剂检测:对添加抗UV剂的瓶坯,需验证其成分稳定性及迁移量,防止光氧化导致的材质劣化。
行业标准与检测技术发展
目前PET瓶坯检测需遵循ISO 9001质量管理体系、ASTM D2562机械性能标准及GB/T 17931食品接触材料规范。随着智能化检测技术的普及,近红外(NIR)光谱快速分析、机器视觉在线检测等新技术正逐步替代传统人工抽检模式,实现更高效率与更精确的数据追溯。
通过系统化的检测流程,PET瓶坯生产企业不仅能提升产品合格率,更能为下游包装商提供合规性保障,满足市场对高品质、可持续包装的严苛需求。
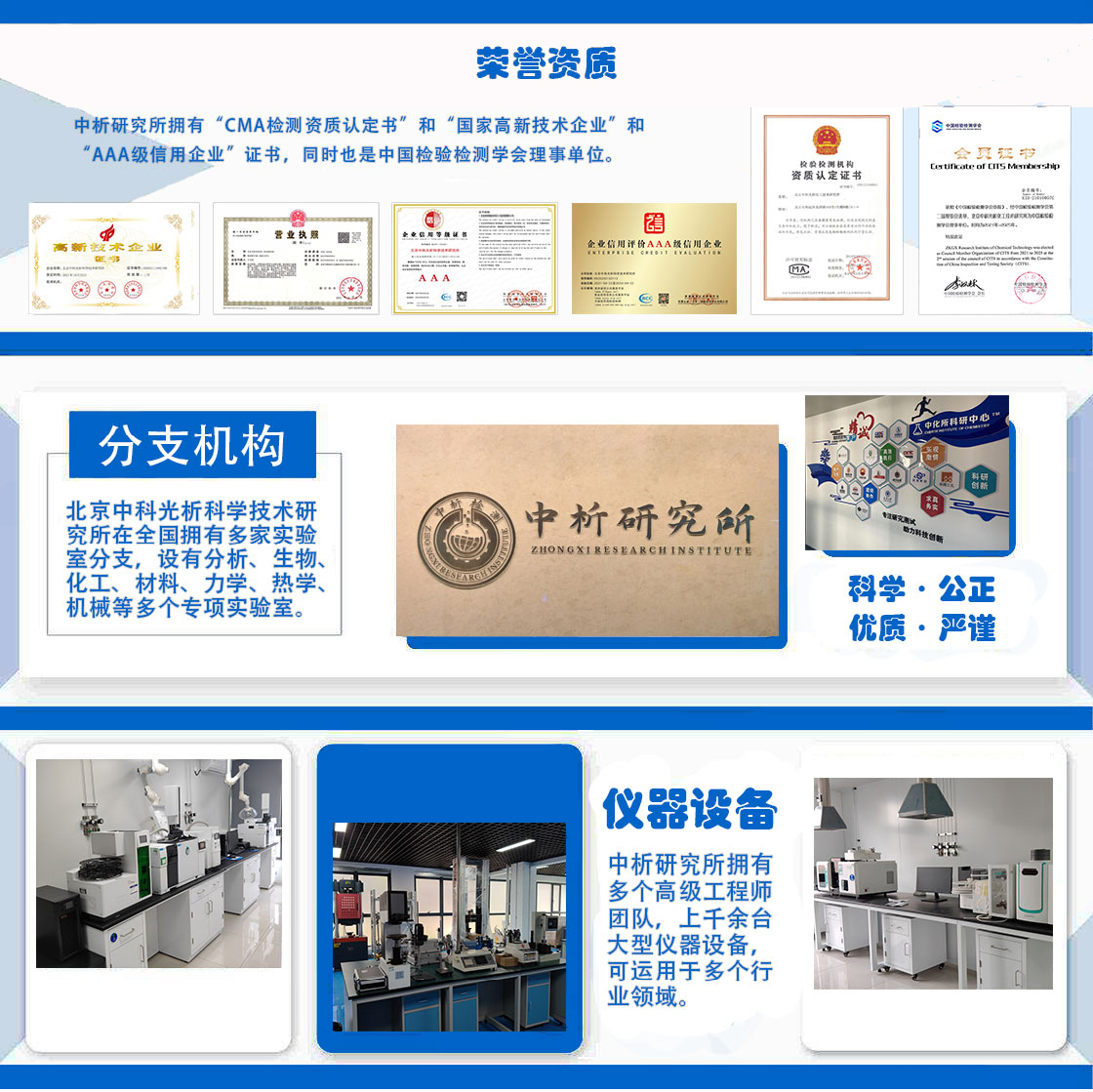
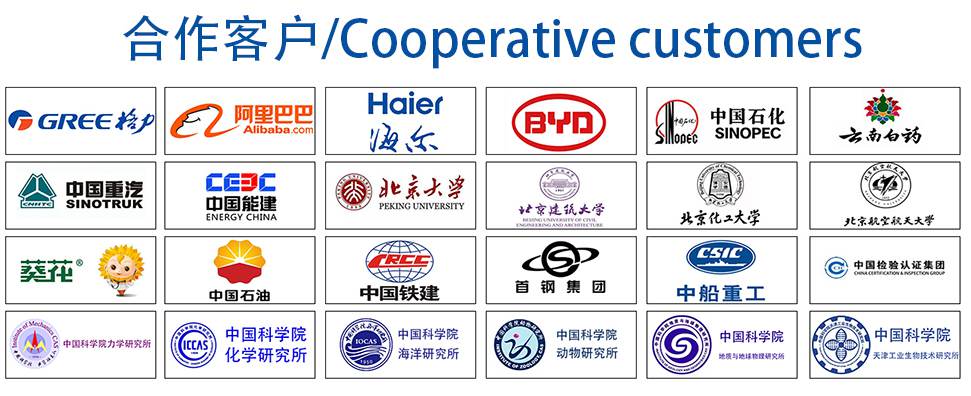