乘用车及其拖车用车轮检测的重要性
车轮作为车辆与地面直接接触的核心部件,其性能直接关系到行车安全、燃油效率及驾驶体验。随着汽车工业的快速发展,乘用车及其拖车用车轮的制造工艺和材料技术不断革新,但同时也对质量控制提出了更高要求。车轮检测不仅需要验证其结构强度、耐久性和动平衡能力,还需评估极端工况下的可靠性。据统计,因车轮质量问题引发的交通事故中,约30%与轮毂断裂、变形或动平衡失准相关。因此,国际标准化组织(ISO)、各国汽车工程协会及整车制造商均制定了严格的检测标准,覆盖从原材料到成品、从实验室到实际路况的多维度测试体系。
核心检测项目与技术规范
1. 结构强度测试
通过弯曲疲劳试验、径向载荷试验和冲击试验,模拟车轮在高速行驶、过载或遭遇路面冲击时的受力状态。例如,ISO 3006标准要求车轮需承受10^6次循环载荷测试,检测是否发生裂纹或永久变形。试验中需使用液压伺服系统精确控制加载力,并通过应变片实时监测应力分布。
2. 动平衡测试
采用高精度动平衡机检测车轮质量分布均匀性,残余不平衡量需符合GB/T 18505或SAE J267标准。测试时车轮以额定转速旋转,系统自动识别并标记不平衡点,指导配重块的安装。动态不平衡量过大可能导致车辆抖动、轮胎异常磨损,甚至影响悬挂系统寿命。
3. 尺寸精度检测
使用三坐标测量仪(CMM)或激光扫描仪进行三维几何检测,包括轮辋直径、偏距(ET值)、中心孔公差、螺栓孔分布圆(PCD)等关键参数。根据DIN 7817标准,轮辋径向跳动量需控制在0.6mm以内,轴向跳动量不超过1.0mm,确保与轮胎的装配密封性。
4. 材料性能测试
通过金相分析、硬度测试和拉伸试验验证铝合金/钢制轮毂的化学成分、晶粒结构和机械性能。例如,锻造铝合金轮毂的抗拉强度需达到320MPa以上,延伸率不低于8%。X射线探伤技术可检测内部气孔、夹杂物等缺陷,避免应力集中导致的早期失效。
5. 疲劳寿命与耐腐蚀性测试
在盐雾试验箱中模拟5-10年使用环境,评估涂层附着力及抗腐蚀能力。同时执行台架耐久试验,模拟车辆在复杂路况下的长期使用,要求车轮在完成等效20万公里测试后无功能性损伤。部分高端车型还需通过-30℃低温冲击试验,验证极端温度下的材料韧性。
智能化检测技术发展
随着工业4.0的推进,基于机器视觉的在线检测系统已被应用于轮毂生产线,实现缺陷实时识别与数据追溯。人工智能算法可分析海量检测数据,优化工艺参数并预测产品寿命。例如,采用深度学习技术识别X射线图像中的微裂纹,检测精度可达99.7%,相比传统方法效率提升40%以上。
通过上述多维度的检测体系,车企可有效控制车轮质量风险,同时推动轻量化、高强度的新型车轮材料研发。未来,随着新能源车对续航里程的严苛要求以及自动驾驶对安全性的极致追求,车轮检测技术将持续向高精度、智能化和全生命周期管理方向演进。
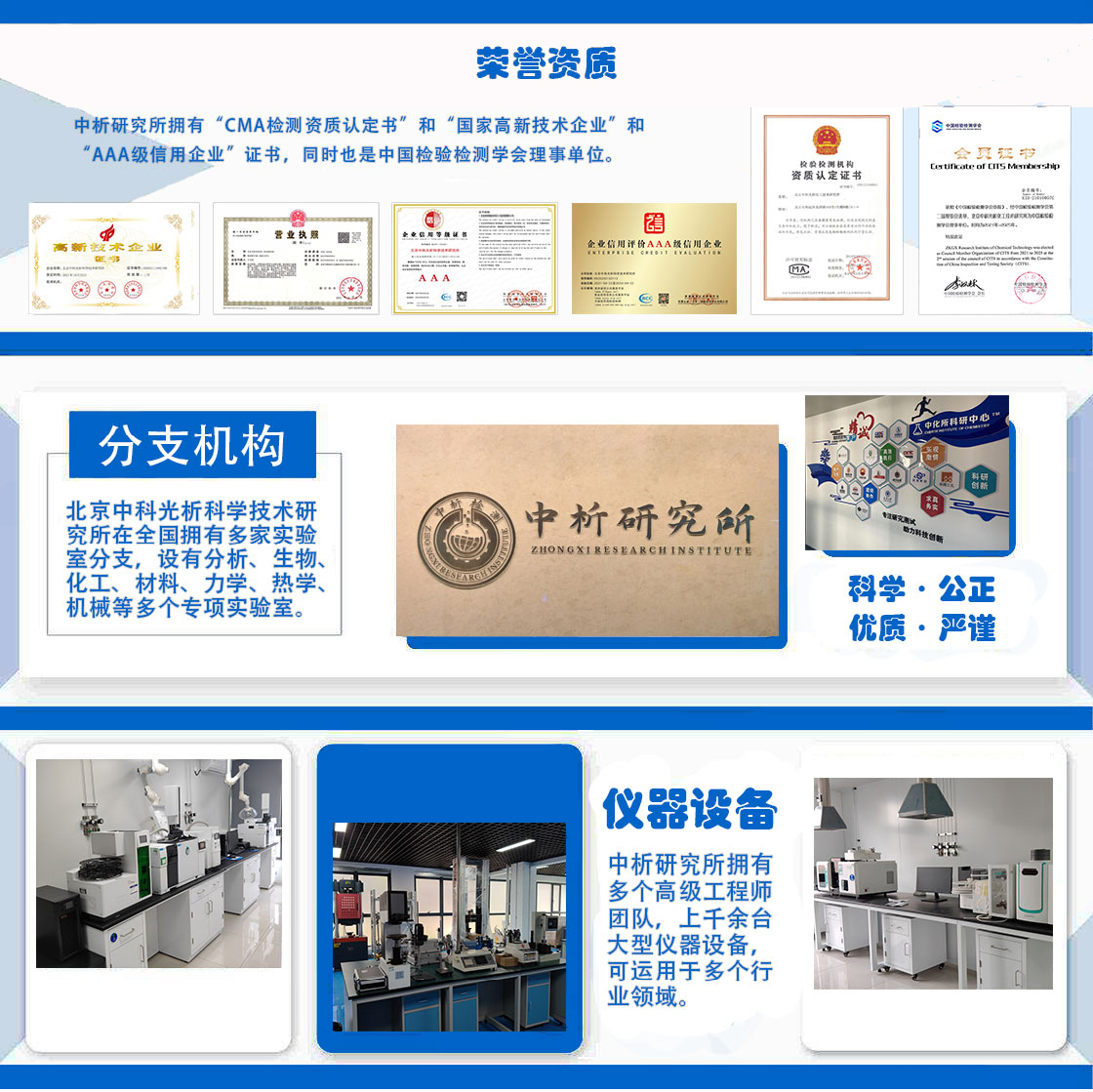
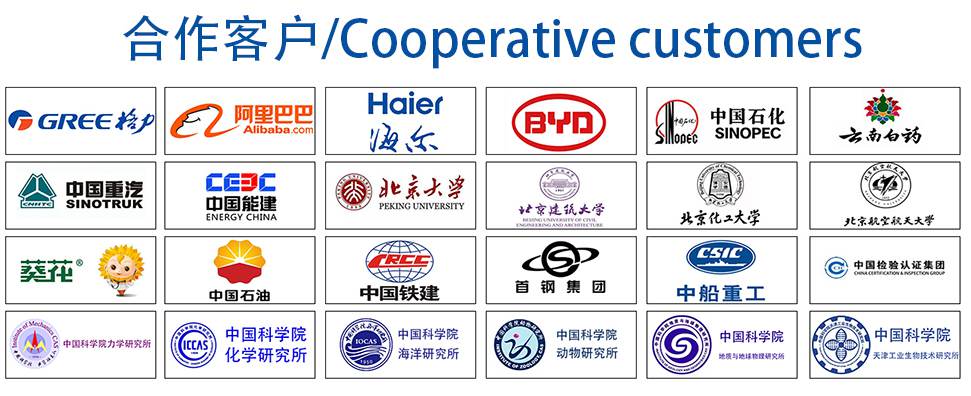