摩擦材料类检测的重要性与应用领域
摩擦材料是机械传动、制动及离合系统中不可或缺的核心组件,广泛应用于汽车、轨道交通、航空、工程机械等领域。其性能直接关系到设备的安全性、耐久性和能效表现。随着工业技术的发展和环保要求的提升,摩擦材料的检测项目日益精细化,涵盖物理性能、化学组成、摩擦学特性及环境适应性等多维度分析。通过科学规范的检测手段,可确保材料在极端温度、压力、湿度等复杂工况下的稳定性,同时满足低噪音、低磨损、无污染等现代工业需求。
摩擦材料类核心检测项目解析
1. 物理性能检测
包括密度、硬度、抗压强度、剪切强度等基础参数测定。采用邵氏硬度计、万能试验机等设备,评估材料在静态载荷下的机械性能。例如刹车片的洛氏硬度需控制在70-110HRB范围,保证制动时既能有效传递摩擦力又避免脆裂。
2. 化学成分分析
通过X射线荧光光谱(XRF)、热重分析(TGA)等技术,检测树脂基体、增强纤维(如钢纤维、芳纶)、填料(石墨、硫酸钡)及摩擦调节剂的配比。重点监控石棉等有害物质的零残留,符合RoHS、REACH等国际环保标准。
3. 摩擦性能测试
在专用摩擦试验机上模拟实际工况,测定摩擦系数(μ)、磨损率、热衰退性等关键指标。依据SAE J661、GB/T 5763等标准,进行常温至350℃的阶梯升温测试,记录摩擦系数波动幅度不超过±15%的稳定性要求。
4. 环境适应性验证
包括高低温循环试验(-40℃~300℃)、盐雾腐蚀测试、湿热老化试验等。模拟雨雪、沿海盐雾等恶劣环境,评估材料表面氧化、分层及摩擦性能衰减情况。例如离合器片需通过100小时5%盐雾喷洒后无可见腐蚀斑点。
5. 噪音与振动特性检测
采用声级计和振动传感器,在消音室内测试制动尖叫噪音(频率2-16kHz范围)及异常振动。通过模态分析和材料阻尼优化,将噪音级别控制在70dB(A)以下,满足ECE R90等法规要求。
6. 寿命与耐久性试验
通过惯性测功机进行台架试验,模拟10万次以上制动循环,监测厚度磨损量、摩擦系数衰减曲线及表面裂纹扩展情况。优质刹车片磨损率需≤0.15mm/万次,确保使用寿命达5-8万公里。
前瞻性检测技术发展
随着智能检测技术的进步,摩擦材料检测正朝着在线监测、大数据分析方向发展。采用红外热成像技术实时捕捉制动界面温度场分布,结合AI算法预测材料失效模式。同时,基于纳米压痕技术的微观摩擦学分析,为新型环保材料的研发提供更精准的数据支撑。
通过系统的检测体系,摩擦材料制造商可优化配方设计,终端用户能精准匹配使用场景,共同推动行业向高性能、低能耗、长寿命的方向发展。
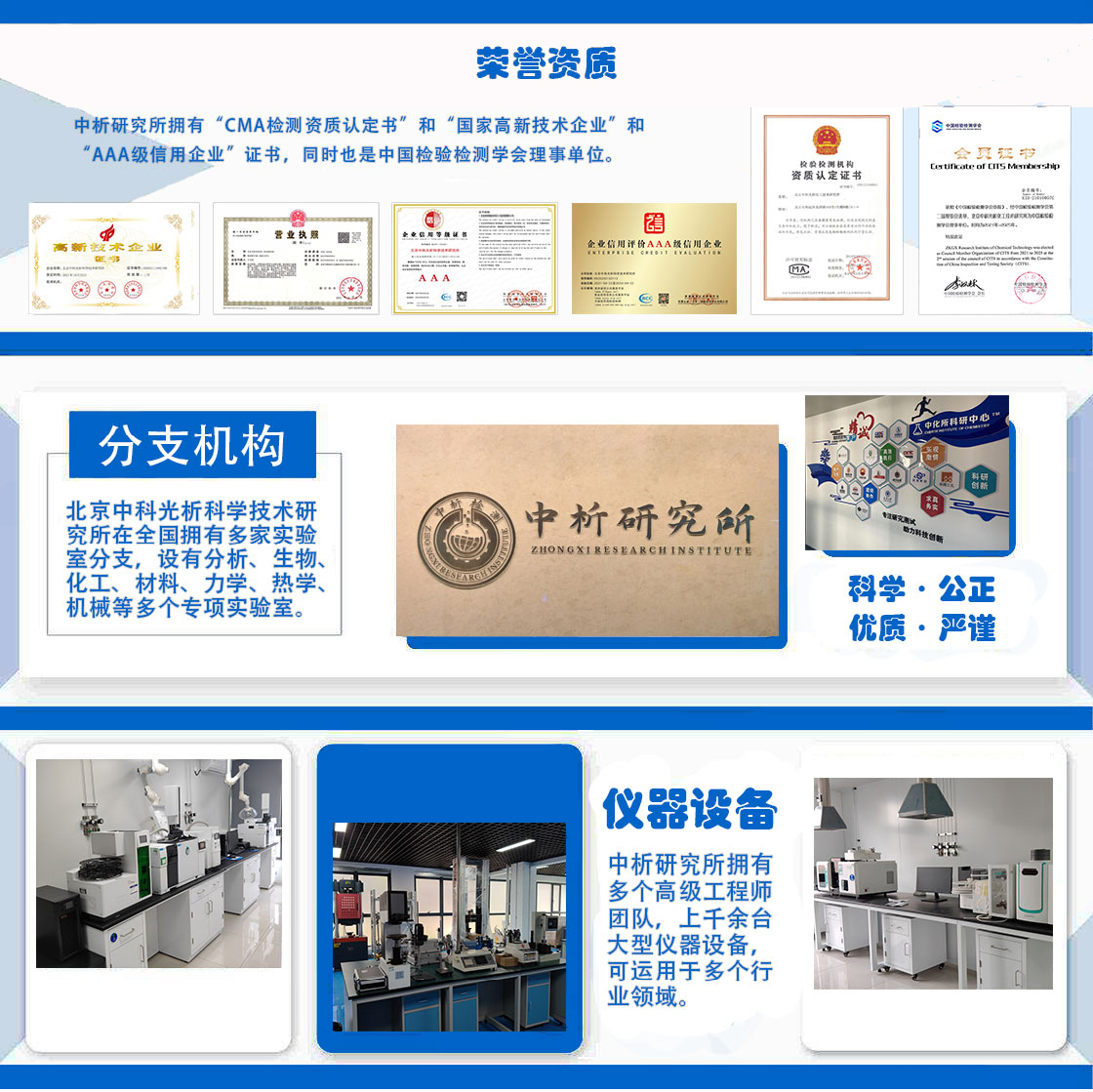
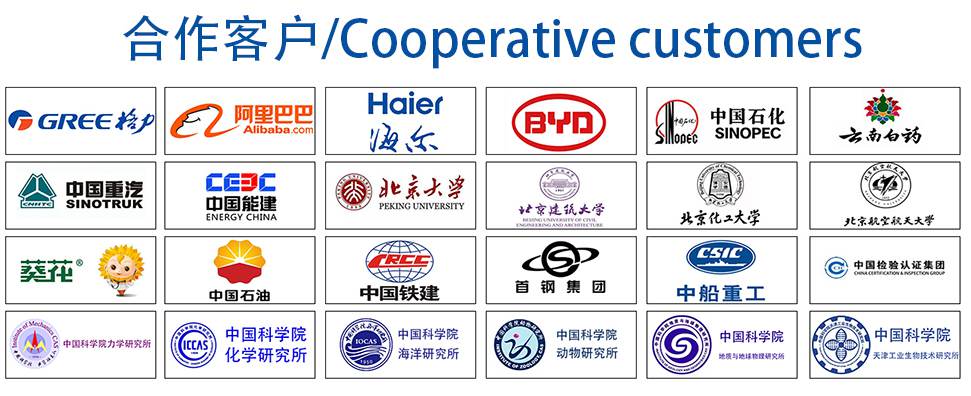