热交换器用铜合金无缝管检测的重要性
热交换器作为能源、化工、电力等领域的核心设备,其传热效率和使用寿命直接依赖于关键部件——铜合金无缝管的性能。铜合金因其优异的导热性、耐腐蚀性和机械强度,成为制造热交换器管材的首选材料。然而,在复杂工况下,管材可能面临高温、高压、介质腐蚀等挑战,轻微的缺陷或性能不达标都可能引发泄漏、爆管等安全事故。因此,对铜合金无缝管进行严格的检测是保障热交换器安全运行、延长设备寿命的关键环节。
核心检测项目及技术要求
1. 化学成分分析
通过光谱仪或化学滴定法检测铜(Cu)、锌(Zn)、镍(Ni)、铝(Al)等元素的含量,确保符合GB/T 5231-2012《加工铜及铜合金化学成分》或ASTM B111标准,避免因成分偏差导致材料性能劣化。
2. 力学性能测试
采用万能材料试验机进行拉伸试验,测定抗拉强度(≥245MPa)、屈服强度(≥80MPa)及延伸率(≥15%)。同时需进行硬度测试(维氏硬度HV90-130),验证材料的承压能力和形变耐受性。
3. 尺寸与几何精度检测
使用高精度卡尺、激光测径仪等工具测量管材的外径公差(±0.1mm)、壁厚均匀性(允许偏差≤±10%)及直线度(每米≤1.5mm)。内壁粗糙度需通过表面轮廓仪检测(Ra≤3.2μm),以确保流体流动效率。
4. 无损检测
采用涡流探伤(ET)全覆盖扫描,检测表面及近表面裂纹、夹杂等缺陷,灵敏度设定为φ0.5mm人工缺陷。对于厚壁管材,需辅以超声波探伤(UT)检测内部缺陷,确保符合JB/T 4730.3标准。
5. 耐腐蚀性能验证
通过盐雾试验(ASTM B117标准,72小时)和晶间腐蚀试验(GB/T 4334),评估管材在含Cl⁻、SO₄²⁻等腐蚀性介质中的抗点蚀、应力腐蚀开裂能力。特殊工况下需模拟实际介质进行加速腐蚀试验。
6. 金相组织分析
利用金相显微镜观察晶粒尺寸(平均晶粒度≥0.015mm)、第二相分布及夹杂物含量,确保材料经过合理的热处理工艺,避免因组织异常导致脆性断裂风险。
质量控制的特殊要求
针对核电站等严苛环境,需增加氢脆敏感性测试(ASTM F1940)和残余应力检测(X射线衍射法)。对于船舶用热交换器,还要求通过海水全浸试验(周期≥30天)验证长期耐蚀性。所有检测数据需形成可追溯报告,确保每批次管材符合TSG 21-2016《压力容器安全技术监察规程》要求。
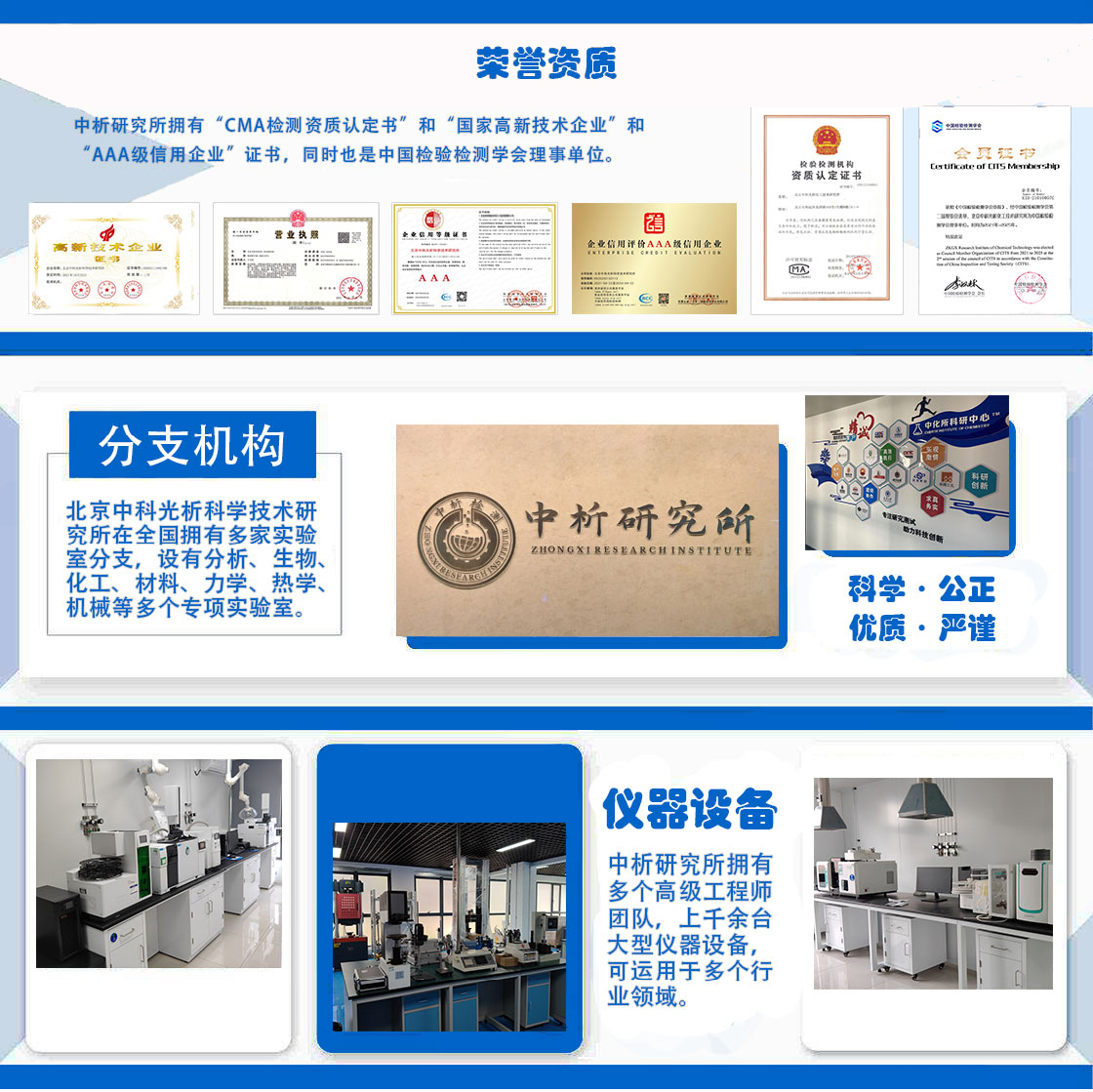
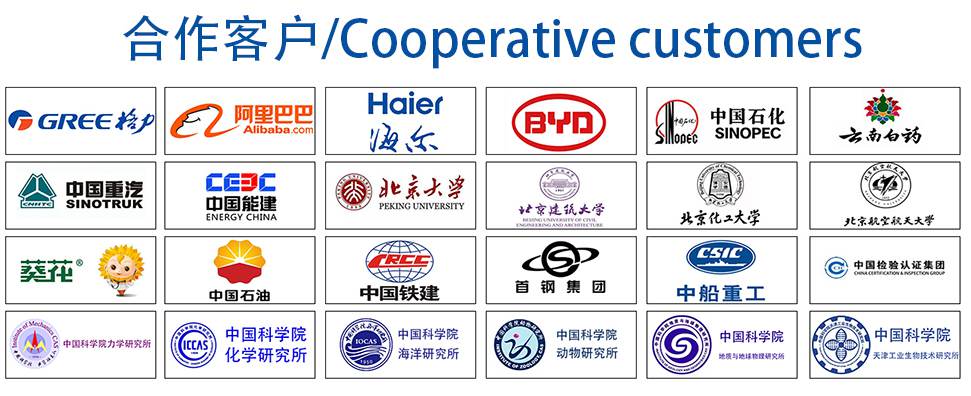