钢制闸阀检测的重要性与流程概述
钢制闸阀作为工业管道系统中控制介质流动的核心部件,广泛应用于石油、化工、电力等领域。其质量直接关系到生产安全与运行效率,因此严格的检测流程和规范的检测项目成为保障阀门性能的关键。根据GB/T 12234《石油、天然气工业用螺柱连接阀盖的钢制闸阀》及API 600等标准要求,检测需覆盖材料性能、密封性、强度等维度,同时结合工况需求开展针对性试验。一套完整的检测体系通常包含10大类目、30余项细分检测内容,贯穿从原材料验证到成品验收的全生命周期。
关键检测项目详解
1. 外观与尺寸检测
通过目视检查阀体表面是否存在砂眼、裂纹等铸造缺陷,使用卡尺、测厚仪等工具验证法兰间距、流道直径等关键尺寸是否符合设计图纸要求。重点检测密封面粗糙度(Ra≤0.8μm)和闸板导向槽的平行度偏差(≤0.02mm/m)。
2. 材质成分分析
采用光谱仪对阀体、闸板、阀杆等主要部件的材料进行化学成分验证,确保碳钢、合金钢等材质符合ASTM A216 WCB、A182 F6a等标准要求。硬度检测使用布氏硬度计,阀杆表面硬度需达到HB180-250范围。
3. 密封性能试验
依据API 598标准进行低压密封(0.6MPa)和高压密封(1.5倍公称压力)测试。采用煤油渗透法检测阀座密封面,要求30分钟内无可见渗漏。对于双向密封阀门,需分别进行进口端和出口端密封试验。
4. 壳体强度试验
使用液压试验台向封闭阀腔施加1.5倍公称压力的试验压力,保压时间不少于5分钟。检测过程中阀体不得出现永久变形,各承压部位无渗漏现象,试验后残余变形率应小于0.03%。
5. 操作扭矩测试
在模拟工况条件下,通过扭矩扳手测量全开/全关过程中的最大操作力矩。DN300口径闸阀的启闭扭矩通常不应超过400N·m,同时需验证手轮转动圈数与阀门开度的线性对应关系。
6. 无损探伤检测
对承压焊缝实施100%射线探伤(RT)检测,符合JB/T 4730 II级合格标准。关键部位采用超声波探伤(UT)检测内部缺陷,磁粉探伤(MT)用于表面裂纹检测,渗透探伤(PT)验证密封面完整性。
7. 耐腐蚀性能评估
通过盐雾试验(500小时NSS测试)评估镀层防腐性能,晶间腐蚀试验验证不锈钢材料的抗敏化能力。对于酸性工况阀门,需按照NACE MR0175标准进行硫化氢应力腐蚀开裂(SSC)试验。
8. 高温高压循环测试
模拟实际工况进行200次以上热循环试验,温度变化范围涵盖-29℃至425℃。检测阀门在热胀冷缩过程中的密封保持能力,阀杆填料函泄漏量需稳定控制在<100ppm。
9. 防火安全试验
依据API 607标准进行30分钟火烧试验,验证阀门在650℃高温下的应急密封性能。试验后需保持额定压力的密封能力,外部泄漏量不超过ISO 5208的B级标准。
10. 文件与标识审查
核对产品铭牌信息与质量证明文件的符合性,包括材质报告、热处理记录、无损检测报告等。确认流向箭头、压力等级等标识的完整性和准确性,确保符合ASME B16.34标注规范。
检测技术发展趋势
随着工业4.0技术的应用,智能检测设备与数字孪生技术正在革新传统检测模式。三维激光扫描可实现0.05mm精度的形位公差检测,声发射技术能够实时监测微泄漏,大数据分析平台可预测阀门剩余寿命。这些新技术推动钢制闸阀检测向智能化、在线化方向发展,为工业装置安全运行提供更可靠的保障。
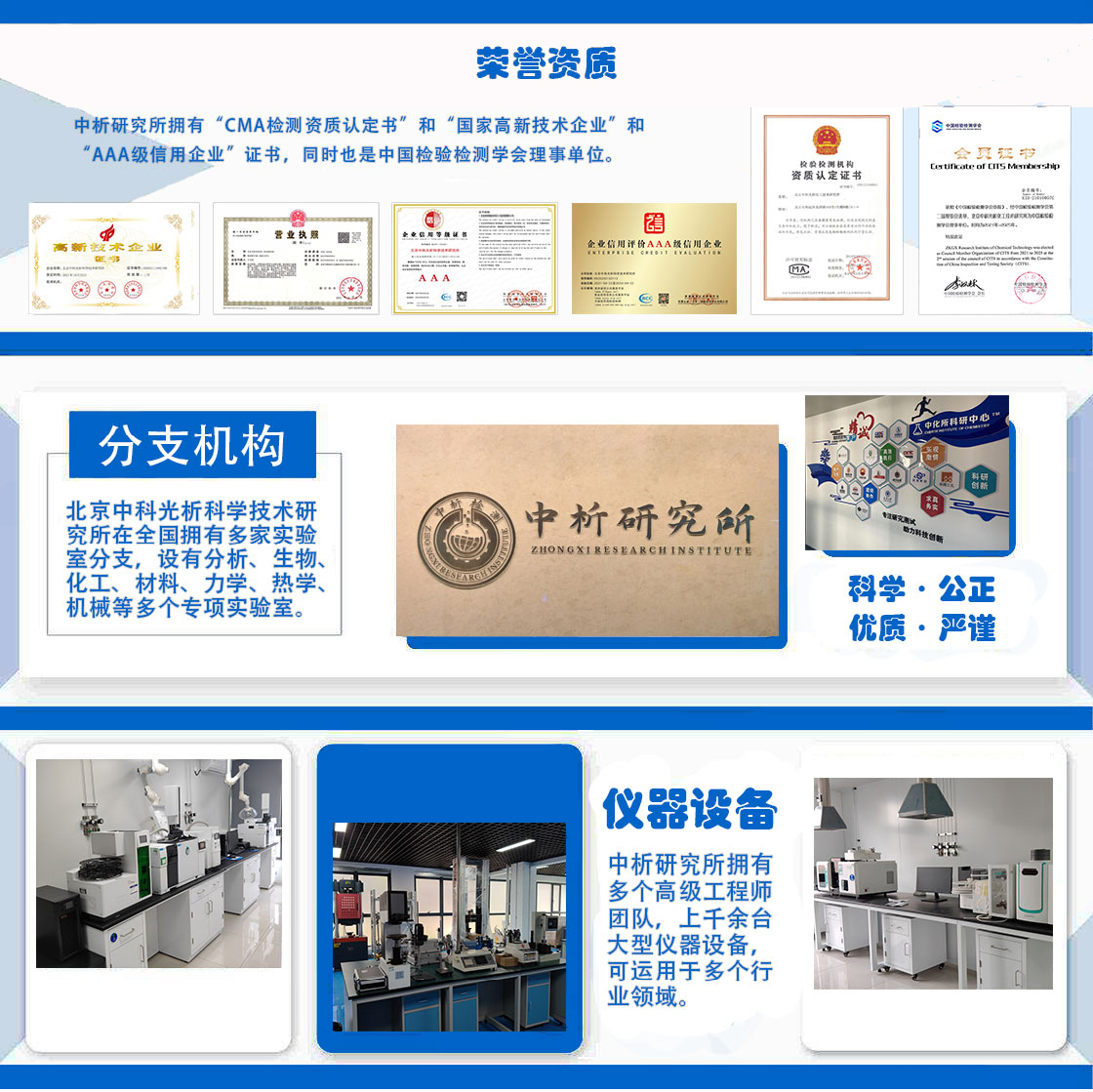
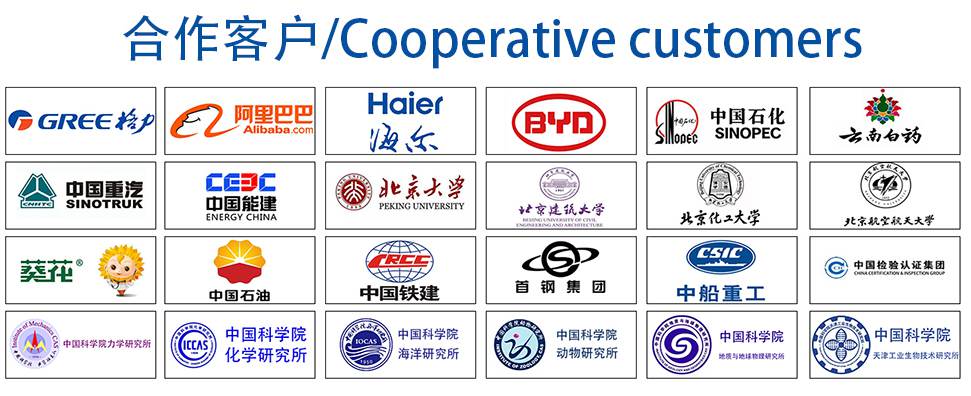