电力金具钢铁件热镀锌层质量检测的重要性
在电力输变电系统中,电力金具作为连接、固定和保护导线的关键部件,其制造质量直接影响电网的安全性与耐久性。钢铁件热镀锌层是电力金具防腐的核心技术之一,通过将钢铁基体浸入熔融锌液中形成合金镀层,可有效隔绝腐蚀介质,延长设备使用寿命。然而,镀锌层的厚度、均匀性及附着力等参数若未达到标准,可能导致局部锈蚀、机械强度下降,甚至引发断线等严重事故。因此,在电力金具制造过程中,热镀锌层质量检测是保障产品性能不可或缺的环节。
热镀锌层检测的核心项目
依据GB/T 2694-2018《电力金具通用技术条件》及相关标准,钢铁件热镀锌层检测主要包括以下关键项目:
1. 镀锌层厚度检测
采用磁性测厚仪或金相显微镜法测量,要求平均厚度≥85μm,局部最小厚度≥70μm。取样需覆盖工件不同部位(如边缘、孔洞等易腐蚀区域),确保镀层均匀性符合DL/T 768.7标准要求。
2. 镀层附着力测试
通过划格试验或弯曲试验验证:使用硬质刀片在镀层表面划出1mm×1mm网格后,胶带粘贴剥离无脱落;或弯曲试样至180°后,镀层无剥离、起皮现象。
3. 硫酸铜试验验证镀层致密性
将试样浸入硫酸铜溶液(36g/L CuSO4·5H2O+64mL浓硫酸)中4次,每次1分钟,镀层表面不得出现红色金属铜沉积,证明镀锌层无孔隙缺陷。
4. 外观质量检查
目视检测镀层表面应连续光滑,无漏镀、气泡、流挂、结瘤等缺陷。重点检查焊缝、棱角等工艺难点部位的覆盖完整性。
检测结果判定与质量追溯
检测机构需建立完整的质量档案,对不合格品进行原因分析(如酸洗过度、浸锌时间不足等工艺问题)。批次抽检合格率低于95%时,应启动全检程序并追溯原料锌锭纯度、前处理工艺参数等环节。通过X射线荧光光谱仪(XRF)可快速分析镀层成分,辅助质量管控。
当前行业正推动智能化检测技术应用,例如基于机器视觉的镀层缺陷自动识别系统,以及物联网数据平台实现检测结果的实时监控与预警,为电力金具的长期可靠运行提供技术保障。
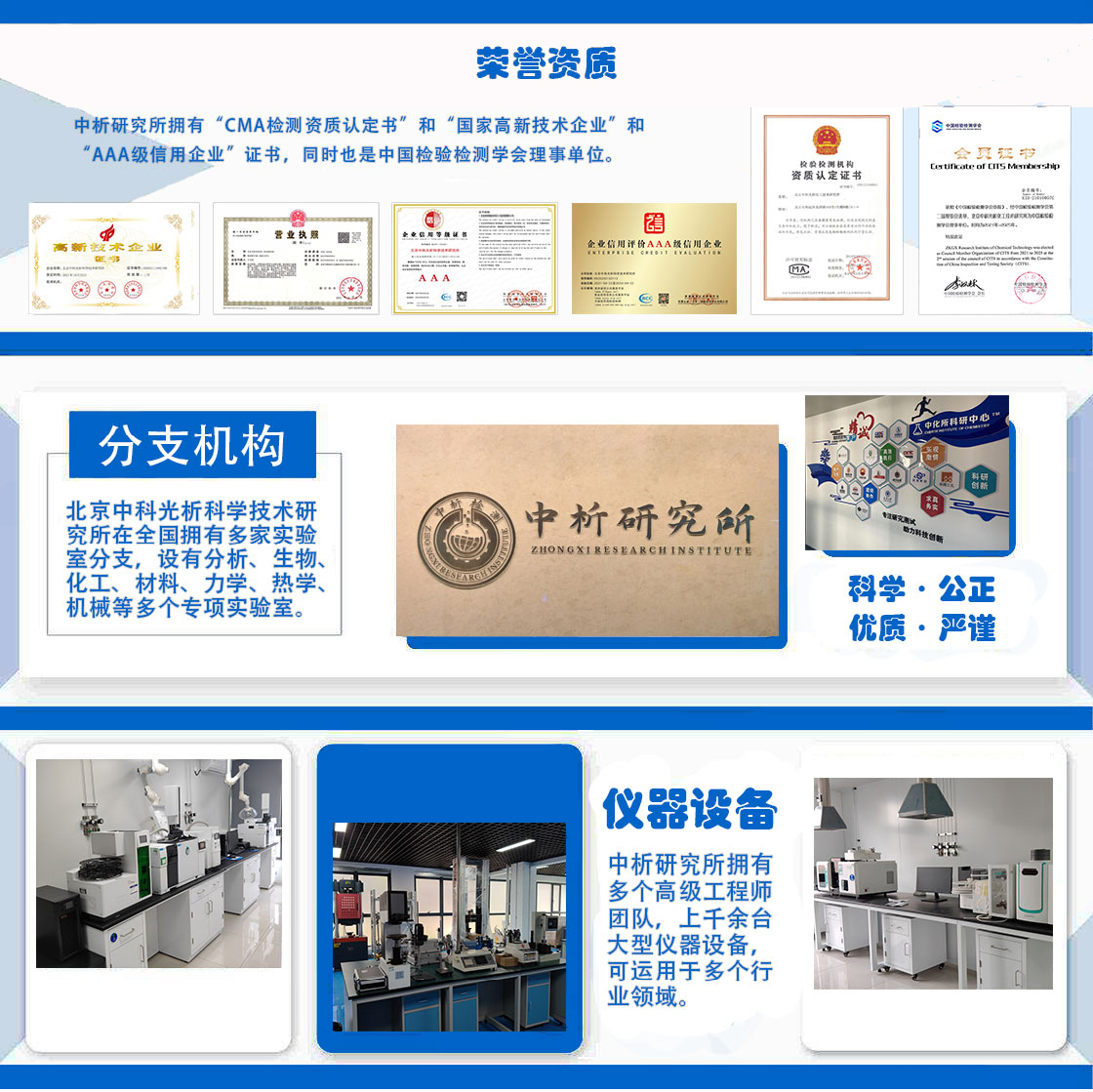
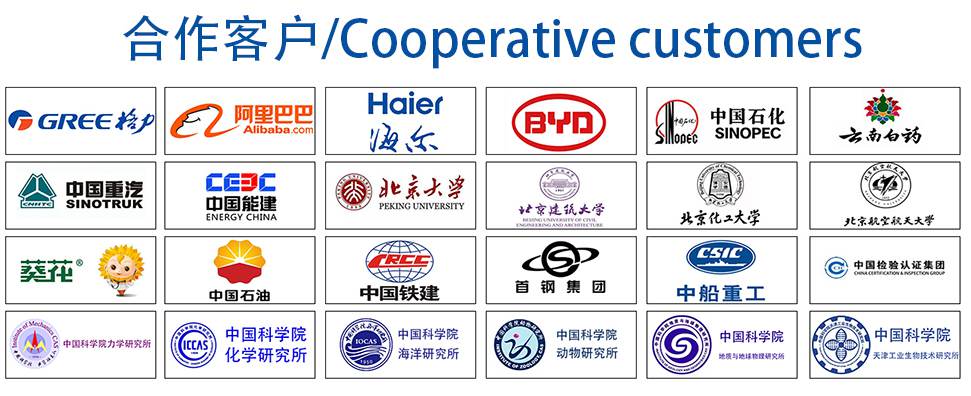